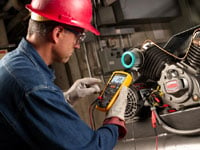
Variable frequency drives (VFD) keep on gaining in popularity. Applied to blowers and pumps, they offer energy savings, and in mechanical applications they allow fine adjustments that wouldn't be possible by other methods. Yet they are not simple plug-in-and-forget devices; they're full of electronics, and they're susceptible to all sorts of problems, from incoming power disturbances to environmental hazards to wrong operation - and one or two unexpected things. The motors they drive present their own challenges.
Dan Orchard has been in maintenance almost 24 years, starting in the Navy. He's now a senior technician at INTIGRAL, Inc., a maker of sealed insulating glass window panels in Walton Hills, Ohio, where he deals with motors - from 300 hp down to 1/16 hp - and variable speed drives on a daily basis. All those years of practical experience have taught him a great deal about how to keep motors running and what to do when they stop. Here's Dan's list of things to do and errors to avoid.
Start with baseline readings of the motor
Don't just take a motor out of the box, throw it in place, and hope for the best. Before putting a motor into full operation, measure the resistance of the windings phase to phase and measure the insulation resistance of the windings phase to ground. Orchard uses a Fluke 1587 Insulation Multimeter to get his baseline readings.
Measure the starting and running amperage, the running voltage and the leg-to-leg balance.
Measure the temperature at first startup, unloaded, loaded and after a period of use. A motor may run hot because it's been used hard, is in a high-temperature area, or has a problem. Without knowing its normal temperature it's difficult to tell which is the case. "It's nice to know are they running hot or is that normal for them," says Orchard. "A lot of times we won't see any problems until the heat really builds up, because the inside temperature near the glass tempering ovens in my plant in the summer time is normally about 130°F."

Orchard measures temperature using a Fluke 61 Infrared thermometer or a thermocouple connected to his 1587 or a clamp meter, and will often compare results between the various methods.
Make other measurements periodically
Depending on your PM schedule, and the cost of unscheduled downtime, take additional amperage, resistance and insulation resistance readings. Compare these readings to previous readings. If the measurements deviate by more then 5 to 10 percent, start looking for bad electrical connections or loose or ill-fitting mechanical connections. Has the load increased, the frequency of use changed, or ambient temperatures increased/decreased?
Find out if the motor matches the application and was specified for the system, or if upgrades are needed.
Check the protection
Look at the protection systems, the overload contactors and fusing. Is the overload set for full load amperes or set too high or low?
Is the fusing correct for the application? Overload contactors are designed to take care of overloads, while fuses and circuit breakers are intended for short circuit protection. Are they sized according to the load? Do the fuses blow without tripping the overload? Are the fuses rated properly? If the fuses blow repeatedly there's a temptation to replace them with higher-rated fuses, But if some time later the overload decides to short across itself and doesn't trip any more, suddenly those fuses that are too high will make the motor cook. That means a lot of back-checking, pulling out the manuals (if they're available), or looking at the nameplate data.
Don't change parts instead of troubleshooting the actual problem
Some technicians will change out parts until the trouble goes away. This is an expensive way to troubleshoot, since most motors and drives start at $500 and up. It's not unusual to find that the same motor/drive that had failed may start working in another application.
This makes the job of finding the original problem harder, since the failure was only temporary. Was it the loading, application or a combination of things that lead up to the failure?
Cabling can be an issue, too
Check the line at the motor, not just at the panel on the wall, which may be a hundred feet away. Power lines in hostile (i.e., high-temperature) areas, even when protected by conduit, may fail. Checking the voltage at the panel and not at the motor may result in replacing a perfectly good motor when the problem is in the wiring.
Look at the drive's setup and parameters. Check the accel/decel times. Are you running at line frequency, higher or lower?
Make sure it's the right motor
Sometimes motors are put into applications for which they are not designed. Inverter rated motors make a big difference in the longevity of the system. Running a standard-duty motor at 50 Hz, for example, often leads to overheating. Similarly, running it at 90 Hz or 120 Hz may work for a while, but the motor can't accept that as a steady diet.
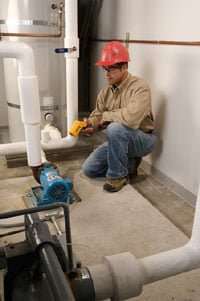
The duty cycle of the motors will help determine where and what application they are suited for. A motor designed to run eight hours a day, five days a week will fail prematurely if it has to run 24/7.
Nameplate data is an important troubleshooting tool. It will tell the motor's service factor, the duty cycle and more. It will also provide useful information about the protection circuits and fusing.
Check for power problems
Many drive failures come from power spikes, phase loss or undervoltages. After a power issue it's important to measure the power to see if the problem has been corrected or is still happening. If you don't check the power after an outage the drives will pay the price. When the power comes back after an outage, the machine operators may just automatically restart and try to run again. "Suddenly you start popping drives, burning up motors, because of singe phase conditions, because a lot of the machines will try to start," says Orchard.
Most newer drives have settings that will not let the system re-start after a fault has occurred. Orchard sets his up so that something like a missing leg of 480 V ac is not overlooked, using phase loss indicators to help the maintenance staff look for problems.
In summary
Dan could keep talking. You can find him on the Test Tool Talk community forum at Fluke Nation