A thermal imaging program is a powerful tool in both preventive maintenance and when troubleshooting critical equipment; both of which can save time and money. Adding thermal imaging inspections is a huge upgrade in your ability to detect and fix issues before unexpected downtime occurs.
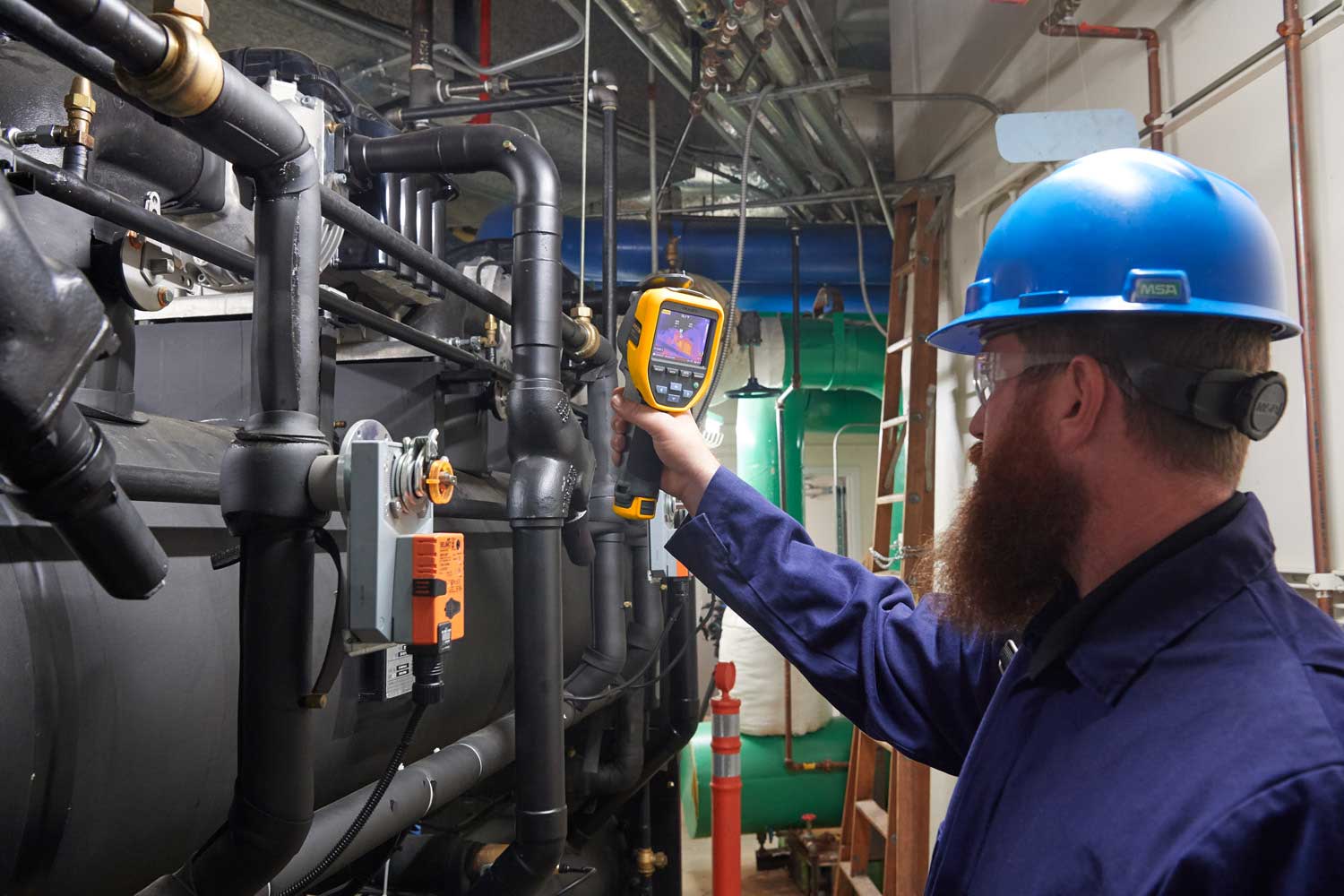
Thermal imaging in your business
Working in maintenance, you already have broad experience with many types of equipment and failure scenarios. Your experience, combined with a thermal camera and some basic training, adds incredible value to see potential issues before failure and to troubleshoot the root cause easily and more quickly. Thermal imaging is commonly used to inspect critical mechanical and electrical equipment with great success.
To properly inspect equipment and interpret the results, thermal imaging training from a reputable trainer is recommended. Look for courses that train you on:
- How to use the thermal camera
- Applications with the greatest return on investment
- How to properly perform inspections
- How to interpret results and generate meaningful and actionable reports
- How to safely conduct thermography inspections in an industrial work environment
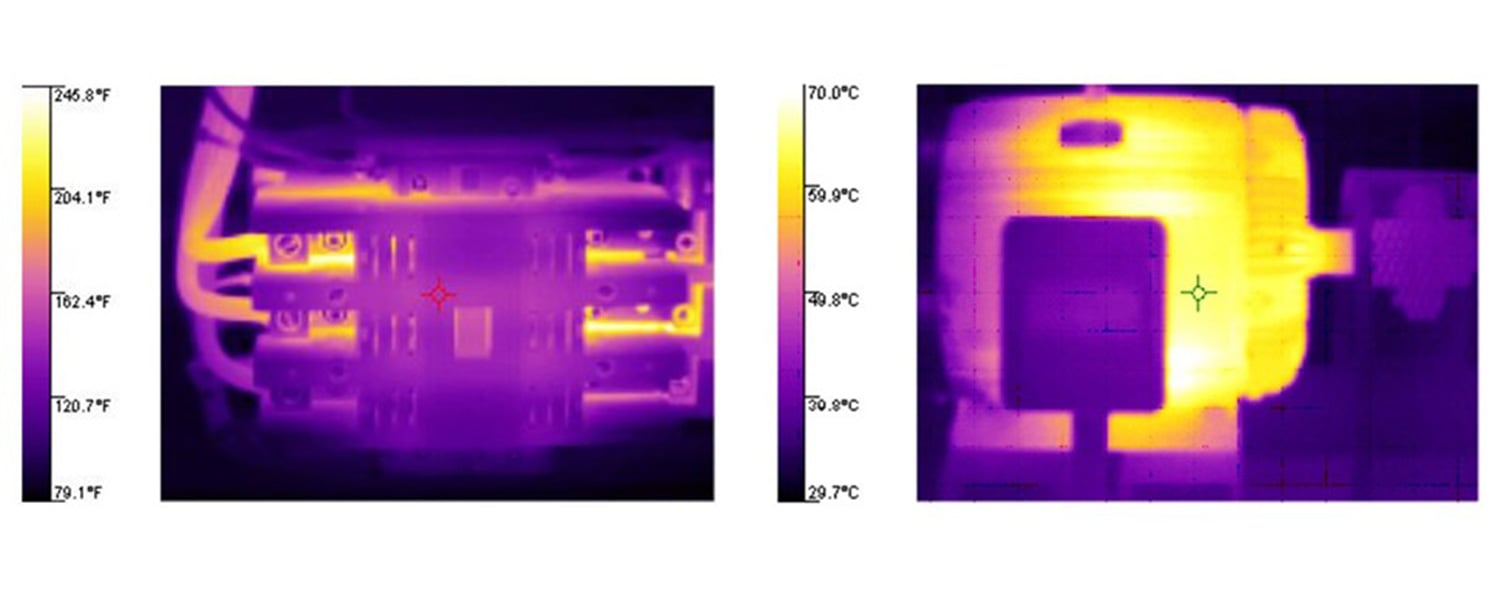
Thermal imaging inspections
Electrical contractors typically use thermal cameras for preventive maintenance, troubleshooting, sometimes during installation, and home inspections. Electricians are uniquely qualified to work in live voltage situations. Specialty thermographers are often not qualified for these situations and require assistance from an on-site electrician, technician, or engineer to access those areas. You can be a double threat as an electrician and thermographer.
Preventive maintenance with a thermal camera
As part of regular preventive maintenance, take thermal images of key units (panels, drives, motors, etc.) at least once a year if not more often. Compare those images with the new ones each visit to catch issues early. Hot spots that weren’t there last time indicate problems in the making to investigate before they cause failure. Thermal imaging software helps you align your images time after time, so that you’re making consistent comparisons.
While conducting your regular preventive maintenance walkthrough, thermography becomes an incredibly valuable way to find problems before they become too large. Keep in mind:
- Most equipment’s failure mechanisms involve a significant rise in operating temperature long before catastrophic failure occurs.
- Thermal measurements help detect problems in nearly all types of equipment, from electrical to mechanical, process, electronic, etc.
- Thermal images are best taken while equipment is operational. No shutdowns needed.
- Thermal images can access components and units often too far away or hard to get to for traditional temperature measurements.
- Thermal images are taken at a safe distance. Minimal safety risk (except for live voltage—that still requires full electrical safety precautions).
- Because thermal inspections are fast, they can cover more ground and find problems in areas that would typically be ignored.
Troubleshooting with a thermal camera
For troubleshooting, using a thermal camera for electrical inspections of a malfunctioning unit can often identify the source of the problem: electrical hotspots can tell you which phase or connectors to check, motor hotspots can narrow it down to bearings, etc. This helps show you where to begin when making repairs.
After repairs are completed, follow up with another thermal inspection to verify the fix; that the component is no longer overheating—or that something else isn’t now overheating.
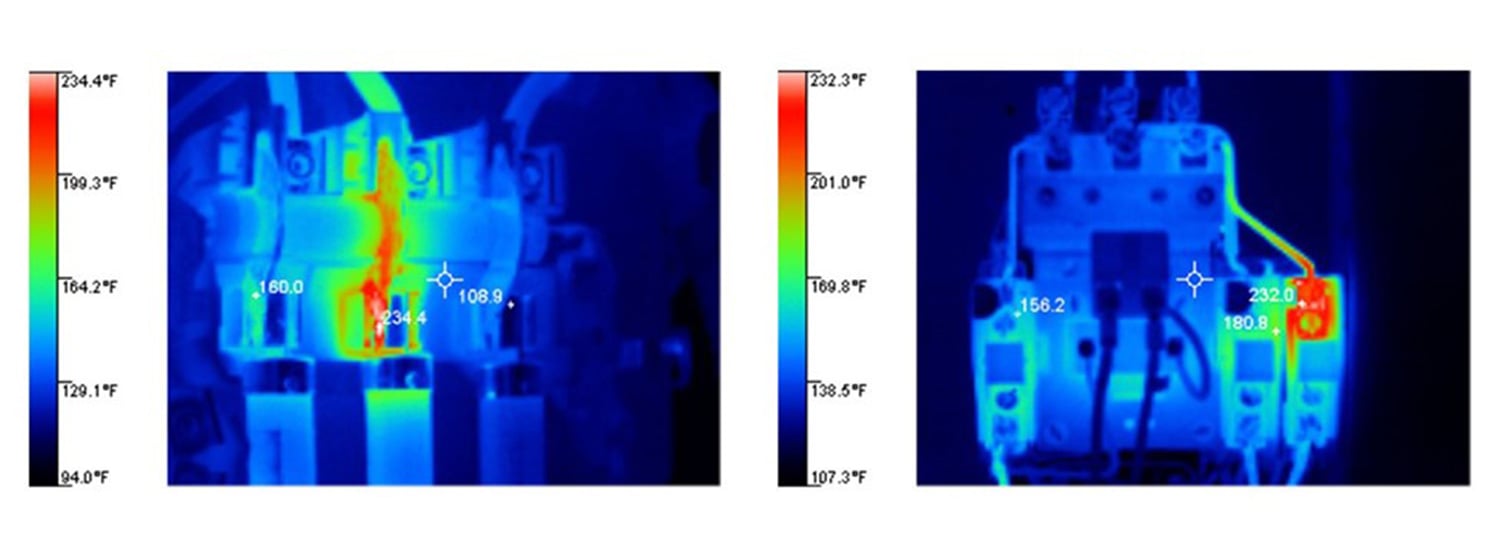
Installation with a thermal camera
Using a thermal imaging camera for electrical installation can help verify everything is working as it should be. Whether you’re adding to an existing electrical panel or breaker, or starting a new installation, taking a thermal image of the panel before and after can help make sure the work is on-track. This step allows you to catch any hot spots or problems while the work is ongoing.
Home inspection with a thermal camera
As a contractor, home or building inspections may be a part of your business. Thermography fits right in to find heat loss and energy waste in HVAC systems, find electrical issues, or even spot water damage.