Surge arresters play a key role in protecting electrical devices and equipment in high-voltage electrical substations. Like other devices, they must be periodically diagnosed. The most common method is visual inspection: checking that the arrester has no visible external mechanical damage.
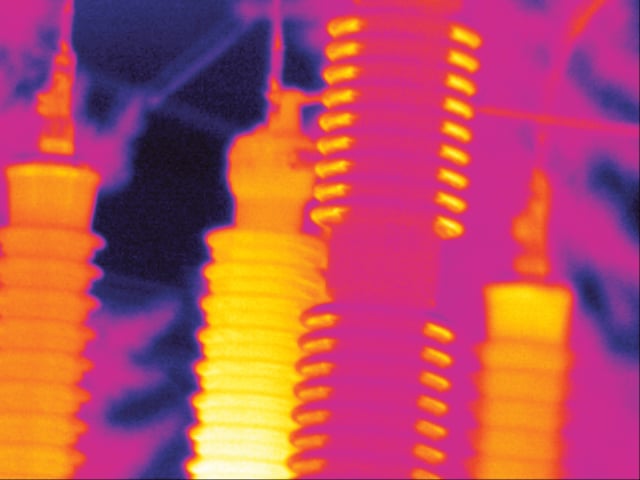
However, an arrester with no visible external damage can sometimes suffer internal damage. As a result, it may not be able to protect against a surge or overvoltage. Doble Engineering makes monitors for detecting leakage currents in surge arresters and got together with Fluke Europe. We used Fluke’s handheld thermal imaging cameras to create a reliable diagnostic solution to this challenge.
Testing high-voltage surge arresters
The IEC60099-5 international standard includes an overview of methods used for diagnosing high-voltage surge arresters. We developed the LCM500 Leakage Current Monitor precisely for this purpose. It performs non-invasive diagnostics of varistor-type surge arresters (with metal-oxide blocks) during operation.
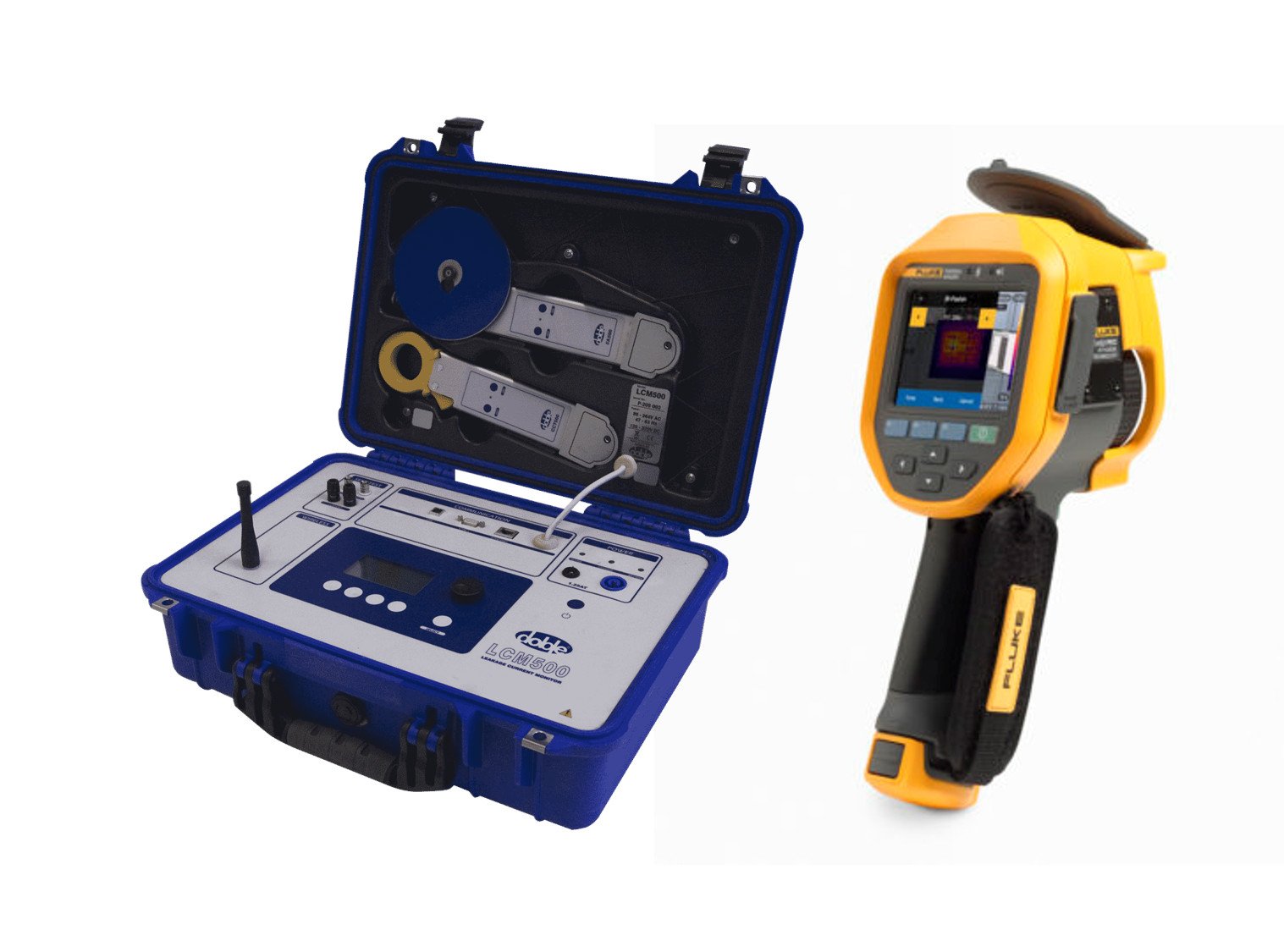
This instrument measures the quality of the metal oxide blocks to help manage the risk of failure. Specifically, it uses IEC60099-5 method B2, analyzing the leakage current’s 3rd harmonic with harmonics compensation in the grid voltage. According to the international standard, this is the most reliable method of diagnosing high-voltage surge arresters during operation.
We tested the LCM500 at a 110kV/6kV overhead power line substation. The station, which has two transformer fields, is fitted with valve-type surge arresters. Table 1 (below) shows the measurements we took from the LCM500. Valve-type arresters should give low total values of leakage current, and current values of same-type arresters should be similar. As shown, though, the L2 phase leakage current was considerably higher than for the other two phases. That suggested that the L2 phase arrester might be damaged.
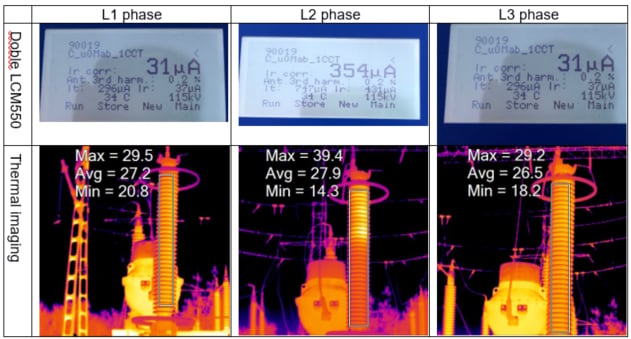
Confirming our results with a thermal imager
We then wanted to make sure thermal imaging cameras could help us to verify the findings of the LCM500. The Fluke Ti450 Pro Infrared Camera seemed like the right choice, since it can capture (and visualize) very small temperature differences. This particular camera is extremely sensitive and gives accurate, sharp onscreen images. It does this even when the surge arresters are high up or far away. Examples of thermal images from the field study are shown in below. The temperature difference Delta-T of 10°C in the arrester’s upper part shows additional local heating.
This approach of measuring the leakage current using the LCM500 and then using the Ti450 Pro infrared camera clearly showed damage in the L2 phase surge arrester. Our tests also confirmed that the LCM500 can effectively assess the technical condition of high-voltage, valve-type surge arresters. We concluded that this complementary method of verifying the possible damage to surge arresters provided the reliable diagnostics solution we were looking for.
*Please note that the Fluke Ti450 Pro Infrared Camera has been updated to the Ti480 since the original publication of this case study.
Related resources