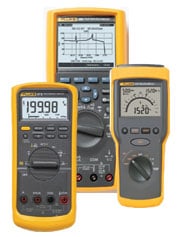
Palm Beach County, Florida, with a population of 1,274,013 (2006 figures), produces a lot of wastewater. To handle it, the Palm Beach County Water Utilities Department's Southern Region Water Reclamation Facility operates around the clock to process up to 35 million gallons per day. About half of that is recycled for use in the County's Reclaimed Water Program, mostly to irrigate water to golf courses and residential lawns in the surrounding areas, and some to feed the nearby Wakodahatchee Wetlands. Another recently constructed 100-acre wetland is available to recycle another two to three million gallons per day.
The treatment facility employs close to 30 people, half in operations and half in maintenance, including two electricians, two instrument technicians, four mechanics, two general maintenance workers and a supervisor of maintenance.
The facility has its own 4160-volt power distribution system for its nine or ten buildings spread over 130 acres; each building has redundant transformers that step the 4160 V down to 480 V for use.
Control equipment includes 120 V control panels and about 20 Allen-Bradley PLC-5s communicating between buildings via Data Highway Plus (DH+) with fiber-optic converter modules and within buildings using the Data Highway network's twin axial Blue Hose cable. The PLCs control the equipment through 24 V Remote I/O, 4-20 mA inputs and outputs, and LAN to a SCADA system with information about flows, levels, pressures, temperatures, conductivity, chlorine content, pump speeds, and so forth.
Plant equipment includes a large number of 480 V motors running pumps and blowers. Motor controls include 700 hp reduced-voltage starters, 400 hp soft starts, and variable frequency drives (VFDs) ranging from 1 hp to 500 hp.
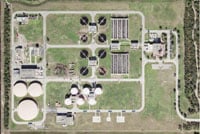
To keep the motors running the facility has a preventive maintenance (PM) program, a big portion of which involves periodic measurements to get ahead of any trend that might go in the wrong direction.
On the VFDs, says instrument technician Bill Moreno, those measurements include monitoring the incoming voltage and tracking both the secondary voltage out to the motors and the amperage to provide a reference for troubleshooting. Moreno also does periodic insulation resistance checks on the motors. "We're finding that's not always as necessary," he says, "as sensitive as the drives are getting, but as a practice I still keep track of the megs historically." At one time, he used a hand-cranked instrument for this, but for the past five years has been using a Fluke 1520* MegOhmMeter. Another of the staff electricians uses a Fluke 1503 Insulation Resistance Tester.
Chasing an intermittent fault
Up until recently, the instrument Moreno used most frequently was a Fluke Model 87 digital multimeter (DMM), which he found especially useful in solving an elusive problem with a motor driven by a 500 hp variable frequency drive. The motor would run fine for 12 or 24 hours, then begin indicating an intermittent short circuit. Preliminary tests suggested that the problem might be either in the VFD or a short in the motor. The VFD manufacturer was leaning toward the motor, so Moreno did an insulation resistance check on it. "Every time we checked the motor," he says, "it was reading 80, 100 megs." While that might seem a little low to some people, he continues, "it's an outside motor, it's very humid down here, so... we don't get a real high reading." And the reading was relatively constant when compared with earlier readings taken as part of the preventive maintenance program.
He then called in the motor company, which ran a surge test on the motor and found it healthy - a good thing, Moreno says, because pulling out a 500 hp motor is a lot of work. That left the drive, but how to prove it?
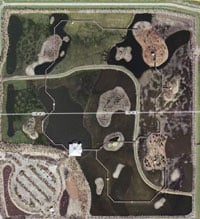
The tech support people from the drive company suggested a diode test, which showed that the diodes were good. The next suggestion was to isolate the drive from the motor and check to see if the phase-to-phase voltages were within 1 to 2 percent of each other. Isolating the motor was simple: just de-energize the output contactor. But Moreno didn't have any way to measure phase-to-phase voltage. There was a power analyzer in stock, but it measured only phase-to-ground voltages, which were no help.
He then got an idea: He gathered up three Fluke 87 DMMs, stuck them to the panel using their ToolPak accessories, and connected them between phases. He then ran the drive at 25, 50, 75 and 100 percent, and found "about a 3 to 4 percent voltage imbalance." He reported this back to the drive manufacturer, which concluded the problem was a bad board in the drive and put one on order. Problem solved, without having to pull out the motor.
Looking for a new meter
While the 87 DMM is a fine and versatile instrument, Moreno had been feeling the need for something with a recording function and a low-pass filter for more accurate voltage and frequency measurements on VFDs and other electrically noisy equipment. He decided to order a Fluke 289 True RMS Industrial Logging Multimeter with TrendCapture.
Solving a tough vibration problem
The new 289 DMM proved its worth when Moreno was faced with a puzzling problem. A 500 hp motor that drives a pump had just come back from the motor shop, where it was rebuilt and supposedly balanced. But when connected to the pump and started up it would get to about 95 % of full speed and then trip out from vibration. Trying to find the cause of the tripping, Moreno looked first at the 120 V ac control circuitry for the VFD, which is mounted in a panel next to the VFD itself and connects to things like low water level cutout floats and a vibration/temperature monitoring system. But the voltage readings didn't make any sense. Even when the enabling relay was open there was still about 90 V on the line. What did that mean, and where was it coming from?
The 120 V control lines share a duct with 480V power wiring. Perhaps that was the source of the mysterious voltage. Moreno then switched his 289 DMM to the LoZ mode, which puts a low impedance across the meter's input terminals and is intended to eliminate ghost voltages. As soon as he did this, the stray voltage vanished. None of his previous meters had come with the LoZ feature, and tracking down the stray voltage would have been a real challenge, but with the 289 DMM it was easy.
One problem was solved, but the motor was still tripping out. So Moreno started to look for the exact speed at which the trip-out occurred. He connected his 289 DMM to the output of the VFD that drove the motor and engaged the meter's low-pass filtering function. The output of a VFD has all sorts of odd wave shapes and harmonics extending into the kHz region that make it quite difficult to get an accurate frequency reading with a conventional DMM. With the low-pass filter turned on, the 289 sees only the power frequency components of the output (see below) and gives an accurate frequency reading.
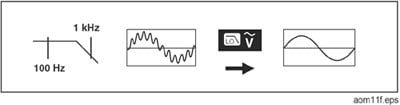
Moreno also used the min/max frequency function with time stamp to determine the exact frequency at which the trip occurred, and finally discovered that the problem wasn't the motor itself, but the way it was used. The pump is located about 20 feet below the motor, and it turned out that even though the motor itself was properly balanced, the combination of pump and motor was not. The answer was to balance the pump and motor together.
Moreno has also used the 289 DMM to check the calibration on a valve actuator, by measuring the unit's 4-20 mA feedback signal - the first time he had used that option. "Once I got it set up it's been working like a champ," he reports. Moreno's overall impression? "This meter has been very nice; I've been pleased with it."
- Tools: 87 DMM, 289 DMM, *1520 Insulation Resistance Tester
- Operator: Instrument technician Bill Moreno for Palm Beach County Water Utilities Department's Southern Region Water Reclamation Facility
- Measurements: VFD output filtering, Min/Max frequency measurements, phase-to-phase voltage imbalance, motor insulation resistance checks