Vibration, on a basic level, is just a back and forth movement - or oscillation - of machines and components in a motorized equipment. Sometimes vibration in industrial equipment is a symptom or even a cause of trouble; other times, it is part of normal machine operation. Oscillating sanders and vibratory tumblers, for example, rely on vibration in order to function. In other cases, such as internal combustion engines and gear drives, vibration is to an extent unavoidable. However, most devices are engineered to avoid vibration rather than to produce it.
Causes of vibration
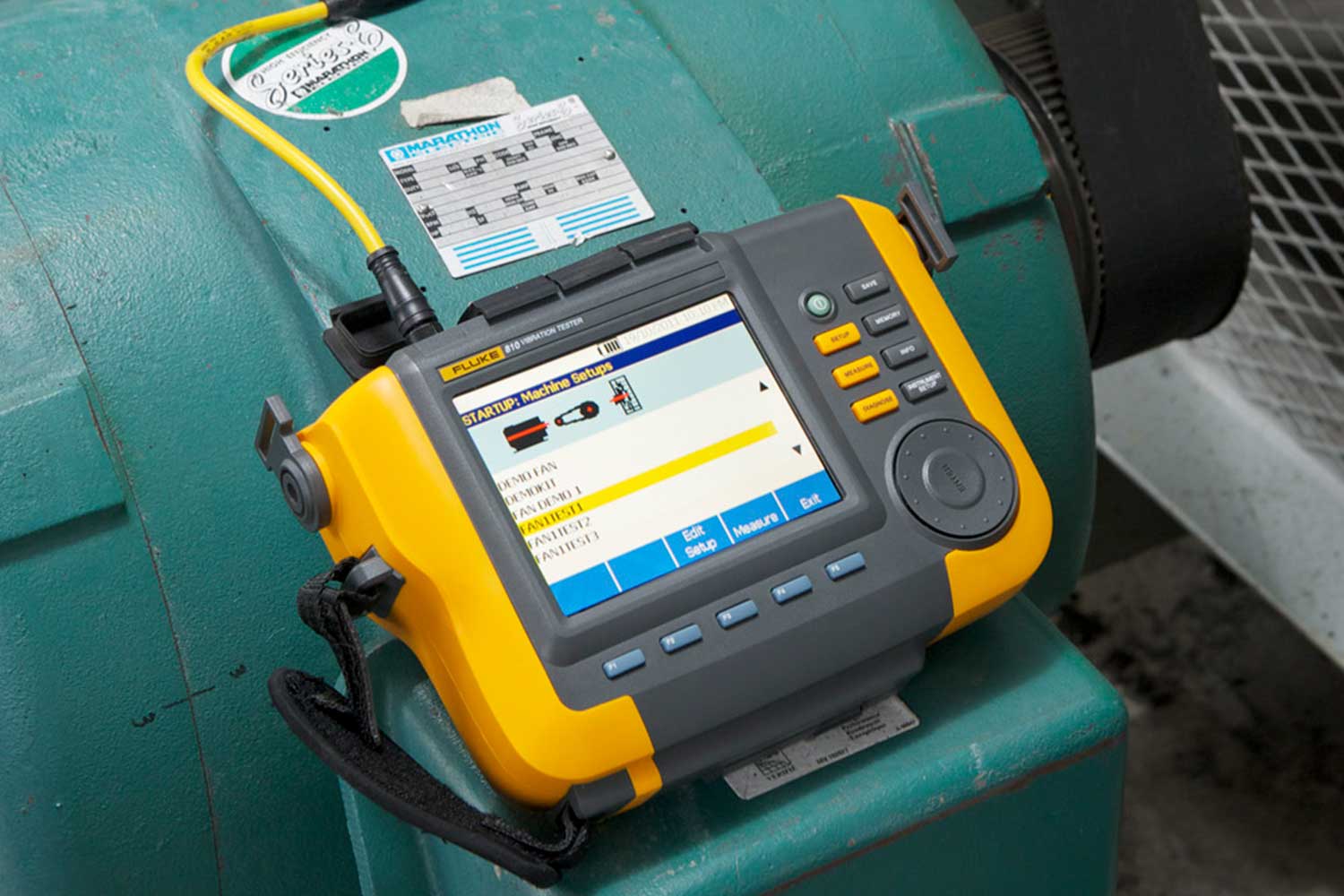
Where not desirable, vibration can indicate a problem in the equipment; left unchecked, vibration can cause damage or deterioration to equipment over time. A number of factors, alone or in conjunction with one another, can cause vibration. Unbalance occurs when a "heavy spot" develops in a rotating component. This can be the result of a manufacturing defect or a maintenance issue. The effects of unbalance increase along with machine speed, and can reduce bearing life or cause machine vibration.
Misalignment or shaft runout is when machine shafts are not in line. This can happen during assembly, or develop over time as a result of thermal expansion, shifting components, or improper reassembly following maintenance. Vibration can be radial, axial, or both.
Wear can produce vibration when components such as bearings, drive belts, or gears become worn or damaged. A heavily worn or chipped gear tooth, for example, can cause vibration when in use. Looseness can leave vibration to cause more extensive damage. If a vibrating component has loose bearings or is loosely attached to its mounts, it can become destructive through added wear and fatigue.
Vibration effects
Where undesirable, vibration can accelerate machine wear and consume excess power, and result in other severe side effects, such as safety problems and worsened plant working conditions. Vibration can even damage equipment to the extent that it must be taken out of service, halting plant production.
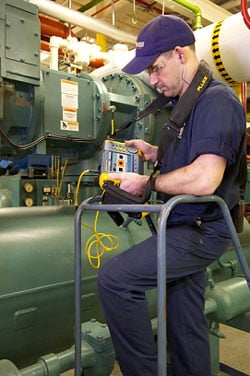
When measured and analyzed properly, however, vibration can play an important role in preventive maintenance programs. It can serve as an indicator of machine condition and allow plant maintenance professionals to act before damage or disaster strike.
When analyzing vibration, variables such as direction (for example, radial or axial) and amplitude (severity) should be taken into account. Another factor to consider is frequency, which is how often the machine moves back and forth as a result of the factor or factors that are causing the vibration. Frequency is typically expressed in cycles per minute or hertz (CPM or Hz). One Hz is equivalent to one cycle per second or 60 cycles per minute.
It is important for plant maintenance professionals to be able to tell when vibration is normal, and when vibration signals a need for immediate attention. Equipped with a basic understanding of vibration and its causes, along with the Fluke 810 Handheld Vibration Tester, plant maintenance professionals can quickly and reliably find the root and the severity of machine vibration, and determine whether there is cause for service or repair.
The Fluke 810 Vibration Tester
The Fluke 810 Handheld Vibration Tester provides the needed information on equipment without requiring extensive monitoring over the long term. The advanced handheld device is designed and programmed to discover and diagnose common mechanical problems. It can detect vibration along three planes of movement (vertical, horizontal, and axial) and provide a plain-text diagnosis with a recommended solution.
Vibration testers and software are typically designed for monitoring machine condition over the long term, and can be expensive and require special training. Many industrial maintenance teams operate with strict limits on their budgets and time; the resources required for the training and implementation associated with long-term vibration analysis programs may simply be out of reach.
This is where the Fluke 810 steps in, and is part of why it is a valuable tool. It is designed to help maintenance professionals determine machine condition and get to the root of any problems quickly. It fills the gap that exists between high-end, complex vibration analyzers, and low-end vibration pens, which sacrifice accuracy for cost and ease of use. The Fluke 810 offers the diagnostic capabilities of the higher-end analyzers along with the speed and convenience of the lower-end testers, at a reasonable price.
It is programmed to diagnose unbalance, looseness, misalignment and more, and can be used to test a wide variety of mechanical equipment, including motors, fans, blowers, drives, gearboxes, couplings, pumps, compressors and spindles.
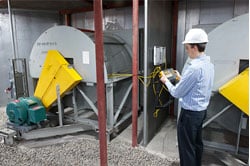
More than just a vibration detector, the Fluke 810 offers maintenance professionals comprehensive diagnostics and problem solving. The diagnostic technology analyzes machine condition and identifies faults by comparing vibration data to an extensive set of rules and algorithms developed over years of field experience. The Fluke 810 determines fault severity by simulating a fault-free condition and establishing a baseline for instant comparison to gathered data. Thus every measurement is essentially compared to a "like new" machine.
When a fault is detected, the Fluke 810 identifies the problem, along with its location and severity, in order to help maintenance professionals prioritize necessary maintenance tasks. It also recommends repairs and uses context-sensitive on-board help to provide users with guidance and tips in real time. This precision allows maintenance teams to act when needed to keep mechanical equipment in peak condition, and to keep facilities productive.
Be the first to learn about the newest Fluke vibration meter