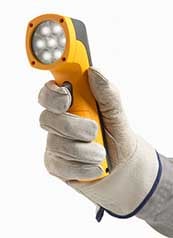
Like old people, old machines tend to slow down as they age. Unless they speed up.
The question for technicians is how much a machine's speed changes, and why - and is it a problem? And it's not just older machines. Almost any device that rotates or reciprocates has an optimal operating speed that can be affected by multiple causes.
Let's start with the basic question: exactly how fast IS this thing turning? The new Fluke 820-2 Stroboscope provides the answer. By lighting up a spinning or reciprocating part with powerful flashes from its seven light-emitting diodes (LEDs), the Fluke 820-2 can make a machine moving from 30 RPM to 300,000 RPM appear to halt in its tracks - and tell the user exactly how rapidly the target is rotating or oscillating.
This is the "stroboscopic effect," a visual phenomenon that occurs when continuous motion is viewed as a series of brief samples that make the moving object appear to slow or stop. And it's all possible without shutting down the machine or production line, and without making contact with the device under test, as other test methods require.
Precisely measuring machine rotation and oscillation are key capabilities for frontline mechanical troubleshooting teams, machine operators and production and quality control groups. The Fluke 820-2 Stroboscope is designed for field work in manufacturing facilities for textiles, food and other products, automotive and aerospace operations and in the mining, metals and petrochemical industries. And it is just as useful in repair facilities and on test benches. In all these applications the ability to see what is happening - and how fast - can provide vital insights into machine performance.
Putting the stroboscope to work
The primary application for the Fluke 820-2 is measuring the speed of a rotating or reciprocating device: a shaft, fan, pump, belt or gear train. Is the mechanism operating within specifications? If it's running too slow, what is the cause? Excess load, bearing drag or vibration, power problems - the causes could be many. If it's running too fast or speed is varying, that could signal other issues. But there's more the Fluke 820-2 can do.
"There's a lot more to this than just a strobe," said Fluke product specialist John Bernet. "Think of this as not only for identifying the speed of rotating machines. It's also able to ‘freeze' moving parts for inspection and troubleshooting. A piston, a fan, a bottling line, a manufacturing line - you can freeze it and find out whether there's a problem. Say you've got a fan blade, but you don't want to shut it down. You can freeze it and read the part number."
Every vibrating object has a certain shape for each frequency at which it vibrates, called a ‘mode shape.' When the stroboscope is flashed to match the frequency of a mode shape, the object appears to stand still, and the shape becomes visible. The resonance frequency of that vibration mode can then be read on the Fluke 820-2 display.
Drive belts are another likely target. Inspecting belt condition ordinarily means a machine must be turned off, but sometimes this is not possible. A stroboscope set to match belt speed makes the belt appear to stand still, so it can be inspected for wear even while operating.
"It isn't just freezing things for inspections or troubleshooting," Bernet added, "it's also to look for timing problems. You can look for quality control issues, say a hammer or a cutting head is supposed to hit at a certain time. You can find out if it really is."
Simple and Fluke-tough
The Fluke stroboscope has several advantages over alternative tools.
Touch-free testing is an important benefit. A laser tachometer (a competing technology) requires that you stop the machine, attach a piece of reflective tape to the shaft, then re-energize the system before you can read RPMs. Such a break in system operation could be tough or impossible to schedule. A contact tachometer (another approach) requires you to place the instrument in contact with the shaft, a practice that could be extremely dangerous, if not literally out of reach. But the bright LEDs of the Fluke 820-2 can light up and "stop" machinery from a safe distance, with virtually never a need for a shut-down.
Another key advantage: The Fluke 820-2 is ready for shop-floor duty. Thanks to the low power requirements of its seven LEDs, three AA batteries provide ample power for months of use. Its solid-state LEDs use no filaments, gases, hollow cavities or glass, and the tool is tested to survive a one-meter drop.
That Fluke-class durability provides a huge advantage over earlier xenon-bulb stroboscopes, which use the same technology found in automotive timing lights, according to Bernet. "The xenon bulb is the expensive part and when that goes, you throw away your device," he said. "Typically those strobes come in a big plastic box that does not protect the xenon bulb at all, so you do not carry these out in the field. You would have to stop what you're doing, go back to your office, get the strobe and drag it out there."
But the compact Fluke 820-2 fits as comfortably in the technician's tool bag as it does in his or her hand. A multi-line digital display reports the flash rate. Buttons on the back of the tool speed the process of matching flashes to machine speed by boosting the flash rate 2X, or cutting the rate in half. For final synchronization, a two-way trigger on the front of the tool allows the user to precisely adjust the flash rate up or down with the move of a finger.
A useful addition
The tool also includes advanced features: the duration of light pulses can be trimmed to make for greater clarity at very high test speeds. By decreasing flash duration, objects have less time to move and the image will appear sharper. The quartz control system delivers accuracy of 0.02 percent.
The Fluke Stroboscope can be used to inspect gear teeth, roller bearings and other machine components under load - even freeze motion to help diagnose the frequency and cause of vibration in building foundations. It's a highly useful addition to the team of Fluke test tools used to diagnose and fix everything from input power to variable-frequency motor drives, electric motor condition and temperature, vibration, shaft alignment and more.