An electrician had a customer with a very common problem—an overheated electrical panel. What made the situation somewhat unusual was the fact that the overheating didn't result from any of the usual causes.
The electrician was called in to troubleshoot an electrical panel with 42 circuit breakers that supplied power to dozens of servers and other non-linear loads. The IT tech at the customer site noticed that the face of the 225A main circuit breaker, which was supposed to be white, was noticeably yellow. When he felt the face he found that it was not only discolored—it was seriously warm to the touch.
Although there had been no outages, the resources powered through this panel are mission critical, so the customer couldn't afford to wait until things went bad to address the problem.
Troubleshooting with the power on
Since even a planned shutdown would have been very difficult to schedule, all troubleshooting was done with the power on. In an initial survey of the environment, the electrician noted that the neutral conductor consisted of two 4/0 conductors, an oversized neutral commonly found in panel boards that serve non-linear loads. That told him the system was designed properly.
His next task was to bring out his Fluke 1587 Insulation Multimeter to measure the phase-to-phase and phase-to-neutral voltage on the line side of the 225A main circuit breaker. He was looking for any anomalies that could point to a problem. Those measurements all were well within the normal range—nothing too high or too low.
Next he looked at the current draw on each of the incoming phase conductors with the Fluke 376 Clamp Meter and found that the current was well below 225A on all three phases—ranging from 108.9A to 130.3A. Because the panel powered non-linear loads, the next logical step was to look for current harmonics. The electrician clamped the 376 on the neutral conductor and found the current to be quite low—just 38.9A. If harmonics were causing a problem, the current on the neutral would have been equal to or higher than one of the phase currents.
Ruling out harmonics
What about the loads served by the panel? Maybe there were voltage harmonics there? This time the electrician brought out his Fluke 434 Energy Analyzer to check the harmonic content of the loads served by the panel in question. The harmonic content was consistent with the type of loads served. The voltage was good and there wasn't a lot of extra high current or harmonics; once again he hit a dead end.
But he wasn't finished. Next he recorded the voltage drop across the line and load side phase conductors of the main circuit breaker (See Table 1). A loose or bad connection or an internal problem with the circuit could produce a large voltage drop—something greater than 100 millivolts.
Measurements | |
---|---|
A phase: 51.1 millivolts | A phase: 122.9 amps |
B phase: 41.6 millivolts | B phase: 108.9 amps |
C phase: 137.1 millivolts | C phase: 130.3 amps |
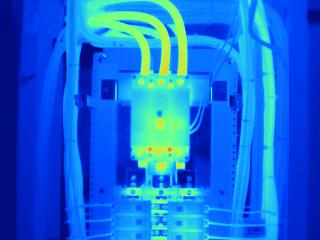
The voltages measured across the "A" and "B" phases were well within range. However, when he got to the "C" phase the 137 mV measurement made it pretty obvious where the heat was coming from. Since the problem still didn't warrant a shutdown, the electrician brought out his Fluke Thermal Imager, which not surprisingly showed the C phase was significantly warmer than the A and B phases (See Figure 1).
At the top of the circuit breaker the wire was very warm and grew cooler as the camera moved farther way from the circuit breaker. This indicates that the problem was most likely at the lug or where the lug connects to the circuit breaker.
Before leaving the site, the electrician attached the Fluke 1735 Three-Phase Power Logger to the conductors feeding the 225A main circuit breaker and left it for a week to measure current. That didn't show any anomalies with the current. (See Figure 2)
Because the troubleshooting isolated the location of the problem but didn't pinpoint the exact cause, the customer and electrical consultants decided to replace the entire guts of the panel—including all of the circuit breakers—and pull new conductors. "We're going to that extent because the cost of down time and criticality of the system are so significant that the customer wants it fixed. They don't want to have to arrange another outage anytime soon," the electrician explains.
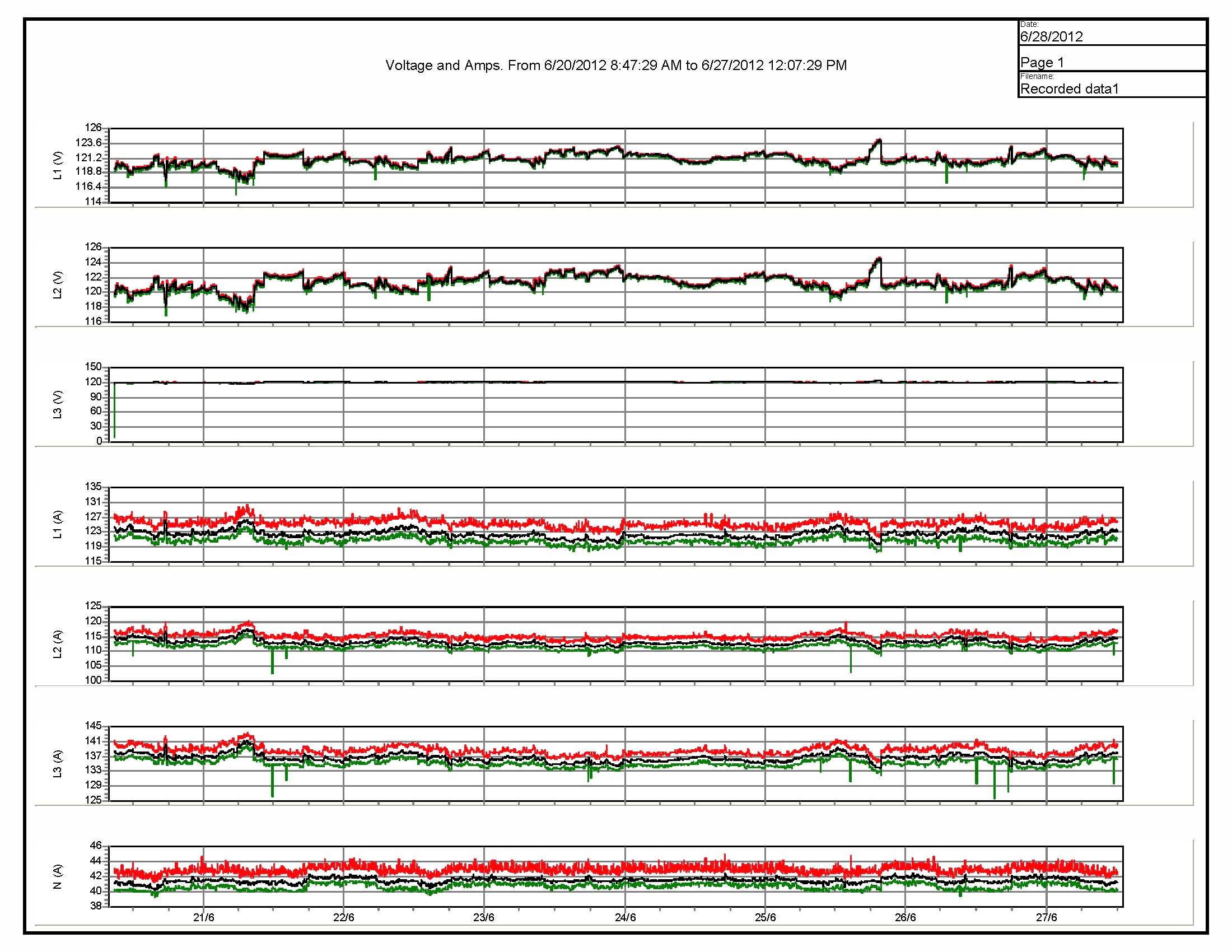
The resolution
Later on the customer found a window of opportunity to shut down the panel and replace it. The electrical consultants weren't taking any chances, though. Before the panel shutdown was scheduled, the new panel interior—complete with branch circuit breakers and main circuit breaker—was sent to an independent testing company. The testing company torqued all the internal connections to specifications and performed a digital low resistance ohmmeter test to verify the integrity of the internal connections.
With a clean bill of health on the new panel, the consultants went to work. They de-energized the old panel, disconnected all the conductors, and removed the guts. At that point they did a visual examination and found that there were signs of severe overheating at the point where the A phase bus connects to the main circuit breaker. [See Figure 3]
Next the electricians installed new interior phase bussing, branch circuit breakers, main circuit breaker, and phase conductors, and reconnected all the conductors. After re-energizing the panel, they tested it to verify that the new panel was working as specified. Using the Fluke 1587 Insulation Multimeter they took a series of voltage measurements including the voltage drop across the line and load side of the main circuit breaker, which showed the following voltage drops:
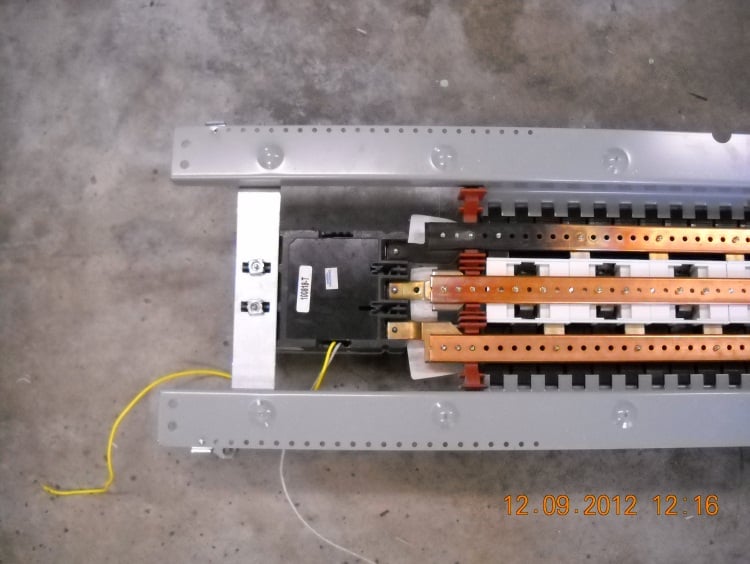
- A phase: 50.4 millivolts
- B phase: 48.8 millivolts
- C phase: 41.4 millivolts
These measurements were well within the normal range so next they measured the amp load on the phase conductors with the Fluke 376 Clamp Meter:
- A phase: 144.1 amps
- B phase: 133.7 amps
- C phase: 132.6 amps
Those readings were also within the acceptable 80 percent rating requirement.
Finally, they scanned the phase conductors of the main circuit breaker under load using a Fluke Thermal Imager. The scan showed balanced loads across all three phases.
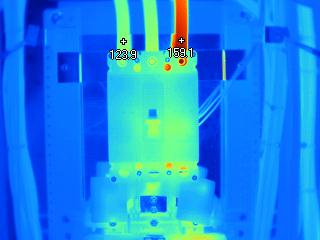
Going forward
Although the measurements showed that the new panel is functioning within the 80 percent load rating, the consultants expect it to approach the 80 percent threshold soon. As the load increases so does the heat, so they recommended that the customer monitor the situation and plan to install a new power feeder in the not-too-distant future.