Sudden production stops can be expensive. Preventing production line stoppage needs well maintained equipment with regular inspections at pre-defined intervals. Monitoring your supply to the EN50160 standard gives you valuable information on the power quality and can quickly repay the cost of the monitoring instrument.
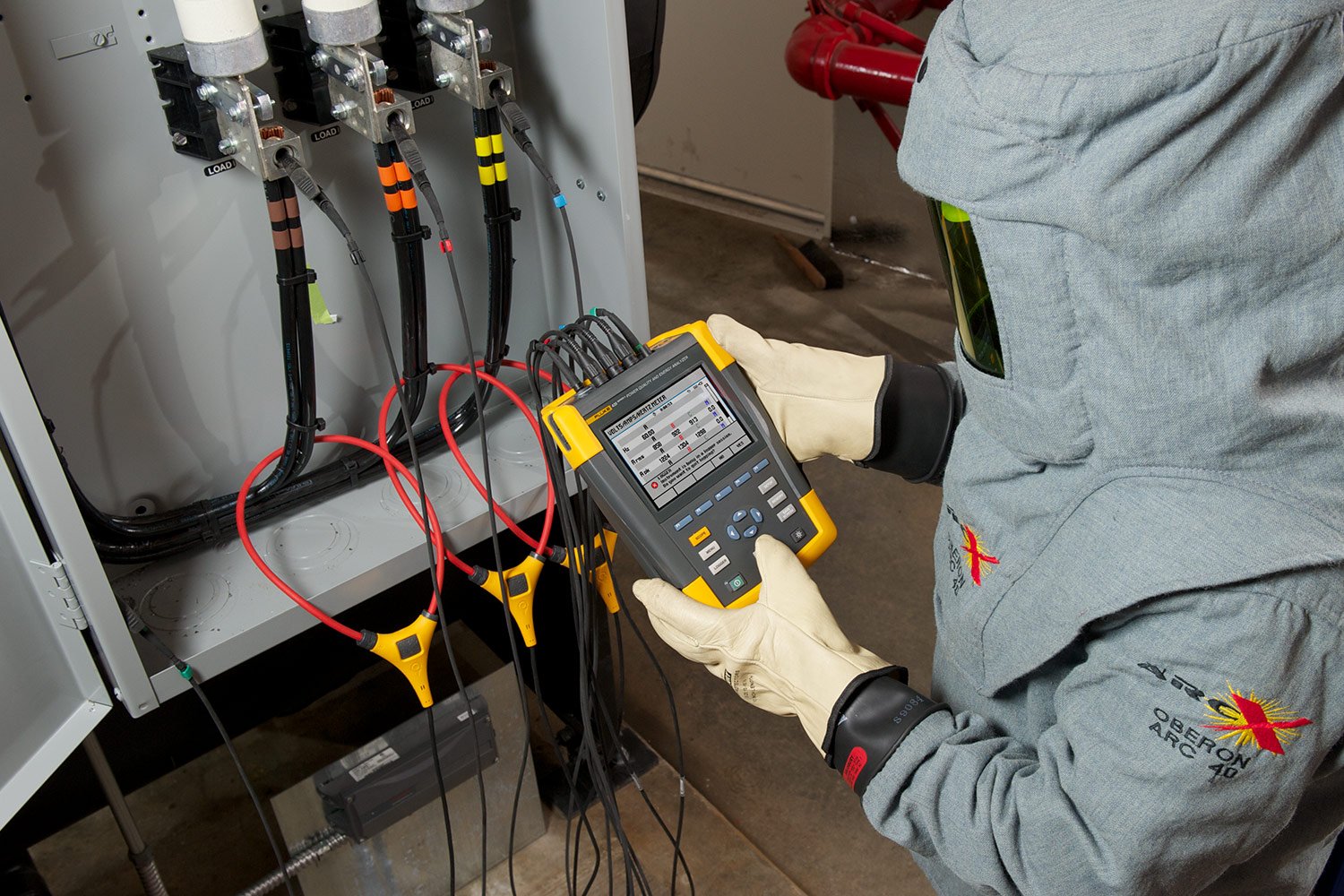
Intermittent production stops can often be simply rectified by a general reset. Easy to solve, but these kinds of interruptions still cost valuable production time and scrapped end of line products. Electricians checked the cables but couldn’t find the root cause.
Was the electricity supply of good quality?
The EN 50160 European standard (Voltage Characteristics in Public Distribution Systems) defines several voltage parameters. The most important are:
- Power frequency
- Supply voltage magnitude
- Flicker
- Harmonics and inter-harmonics
- Dips,sags and swells
- Interruptions
- Supply voltage unbalance
- Mains signaling
- Rapid voltage changes
It is important to monitor the voltage at the point of coupling, which is where the cable enters the facility. This can be behind the revenue meter or at a distribution transformer.
Monitor the supply
To find intermittent problems, you need to monitor the supply on a power quality meter like the Fluke 430 series. This has a monitoring mode, with one screen showing whether the supply voltage meets the EN50160 standard. The statistical screen shows bars that are colored green during measurements if the parameters stay within their limits. If any parameter exceeds its limit, the bar turns red. The pictured screen shows five categories:
- Rms voltage
- Harmonics
- Flicker
- Dips, interrupts, rapid voltage changes and swells
- Unbalance, frequency and mains signaling
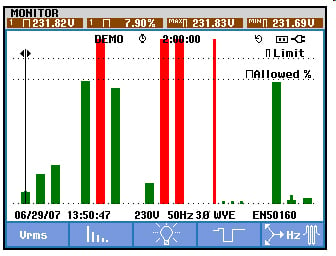
Any of these parameters going outside limits can result in poor power quality and can cause expensive production losses. You can prevent them by checking the power quality at regular intervals.
Related resources
- Electric motor efficiency and reliability: New testing approach matches real-world conditions
- Case study: Three-phase motor failure
- Case study: Low power factor
- 5 reasons to monitor power consumption