No electricity provider in the world can guarantee an electrical supply that is free from voltage and frequency variations. The possibility of faults occurring in users' installations or in the public distribution system remains undeniable and unpredictable.
Since information technology (IT) installations are particularly sensitive to power supply fluctuations and distortions, they typically rely on an uninterruptible power supply (UPS) to compensate. Some installations even include a second UPS supplied by a separate feeder, and a standby generator that can be set to start automatically three minutes after detecting a power interruption. If the risk from weather or other local occurrences is great enough, some facilities will manually switch over to backup generation, ahead of time.
Figure 1 illustrates a typical contingency supply system for critical installations.
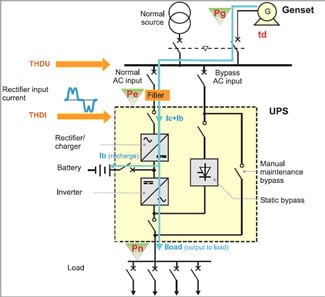
To help your contingency supply systems function as designed, perform the following tests during installation and then periodically (monthly or quarterly, depending on contractual agreements) after the system is commissioned. Tests during installation phase are divided into two stages:
- Pre-installation - test before connecting the critical loads.
- Combined - connect critical loads and test while cutting standby generator in and out.
Pre-installation
1. UPS functional and alarms tests
Purpose of the test: Check the UPS functionality, LED display, and alarm messages.
2. UPS specification test
Purpose: Check and measure UPS specifications (Note: Two Fluke-435 are required.).
Procedure: Record voltage, current, real power, apparent power, power factor, voltage and current total harmonic distortion (THD) at both the input and output.
Vary the loads from 0 to 100% in 25% steps for balanced load testing. For unbalanced load testing, follow this load matrix:
Sequence | Phase 1 | Phase 2 | Phase 3 |
---|---|---|---|
1 | 100% | 100% | 0% |
2 | 0% | 0% | 100% |
3 | 100% | 50% | 100% |
4 | 50% | 100% | 50% |
Figure 2. Unbalanced load testing sequence.
3. UPS burn-in test
Purpose: Verify the UPS system can operate at the rated load under ambient room temperature conditions.
Procedure: Load the UPS to rated load and operate for 8 hours to 24 hours, depending on contractual requirements.
4. UPS step load & bypass loss transient tests
Purpose: Demonstrate the transient response of the UPS module.
Procedure: Measure UPS transient response for:
- 0% to 100% to 0% load steps
- 0% to 50% to 0% load steps
- 50% to 100% to 50% load steps
- UPS running with loss of bypass mains
In the example demonstrated in Figure 4, the three phase voltage waveform hardly varied, despite the 100% change in load current.
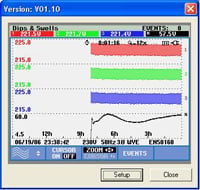
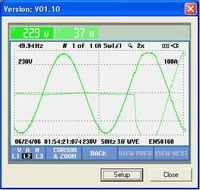
5. UPS start and stop test
Purpose: Demonstrate correct operation when the UPS is switched on and off with full load.
Procedure: With the module running at 50% and 100% load, switch the inverter OFF and ON. Record transients, load voltage, load current, mains 2 current, and mains 1 current.
6. UPS full load battery discharge test
Purpose: Demonstrate correct UPS operation for 15 minutes at full load during a power failure.
Procedure: Measure battery cells before and after discharge using a battery monitoring system.
7. UPS loss and return of mains test
Purpose: Demonstrate correct operation during loss and return of the mains.
Procedure: Run module at normal load and switch the UPS main input ON and OFF.
Record transients, load voltage, load current, and mains 1 current.
8. UPS loss and return of battery test
Purpose: Demonstrate correct operation during loss and return of UPS batteries.
Procedure: Run module at normal load and switch the UPS main battery breaker ON and OFF. Record transients, load voltage, load current and mains 1 current.
9. UPS load transfer test
Purpose: Demonstrate correct operation during load transfer. Procedure: Run module at normal load and switch UPS OFF and ON until the load is on static bypass. This procedure is reversed from static bypass to UPS.
Record load voltage, load current and bypass current.
10. UPS transfer to bypass and back test
Purpose: Demonstrate correct operation with external bypass. Procedure: Transfer the load to external bypass and back to UPS. Record load voltage and load current.
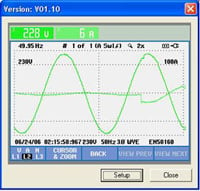
Combined test
Connect the critical loads and standby generator and repeat the same tests at 0% and 100% load conditions. Monitor transfer between the mains supply, UPS, and standby generator to ensure that transients and waveform distortion stays within acceptable limits.
Maintenance test
Conduct periodic (monthly) maintenance tests throughout the life of the contingency supply system. Follow the combined test procedure for everything except the standby generator - it only needs to be tested once a year.
Conclusion
Many tests are involved when commissioning and maintaining a contingency supply system. Many parameters (three phase voltage and current, power, power factor, harmonics and transients) must be logged simultaneously over 8 hours to 24 hours and documented in report format. Use a power quality analyzer with data logging and reporting capabilities, such as the Fluke 435 used by the project team (responsible for site assessment and installation) and the service team (post-sales maintenance) in this example.