Images provided by the Snell Group
Predictive maintenance (PdM) programs monitor equipment condition, with the goal of identifying problems in advance and avoiding equipment failure. One powerful tool for monitoring rotating equipment is thermal imaging.
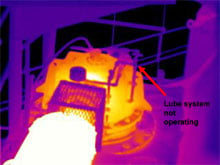
Thermal imagers capture heat-based images, using color to correlate every pixel of the electronic image to a specific surface temperature. For motors and gearboxes in mechanical drives, overheating often signals impending breakdown. A thermal image makes immediately clear what part of the motor is overheating, to what extent.
- Standard practice follows three basic methods: Regularly compare the operating temperatures of like equipment, performing similar functions.
- Regularly compare the operating temperature of a single unit to manufacturer's standards.
- Regularly compare the operating temperature of a single unit to previous images of the same unit.
Following are more specific inspection guidelines.
Motors
Ideally, you should check a motor while it is running at a minimum of 40% of its typical load. That way, measurements can be properly evaluated compared to normal operating conditions. By capturing an image of a whole motor, you can determine the operating temperatures of bearings as well as the temperature and temperature variations of the unit's entire surface.
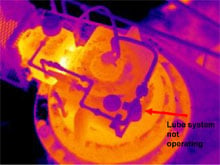
All motors have a normal thermal pattern. Training and experience with both motors and thermal imagery makes a thermographer familiar with motor heat patterns and how they relate to operation. An experienced thermographer can use thermal imaging to identify conditions such as inadequate airflow, unbalanced voltage, impending bearing failure and insulation degradation in a motor's rotor or stator. An experienced thermographer can also identify a misalignment in a shaft coupling associated with the motor. And even a novice can spot anomalies in a motor compared to other similar motors under similar loads and then flag that deviant motor for further investigation.
Troubleshooting motors
If overheating appears to be due to one of the following situations, consider the action described:
- Inadequate airflow. If a brief shutdown is possible without affecting vital processes, shut off the motor long enough to perform minor cleaning on the air intake grills. Under any circumstances, schedule a thorough motor cleaning during the next planned facility shutdown.
- Unbalanced voltage or an overload. The usual cause - a high-resistance connection in the switchgear, disconnect, or motor connection box, can usually be pinpointed by an infrared inspection and confirmed using a multimeter, clamp meter or a power quality analyzer.
- Impending bearing failure. When the thermal images indicate an overheating bearing, generate a maintenance order to either replace or lubricate the bearing. Vibration analysis will help you determine the best course of action.
- Insulation failure. If it will not too greatly impact production, de-rate the motor in accordance with NEMA standards. Under any circumstances, generate a work order to replace the motor as soon as possible.
- Shaft misalignment. In most cases, vibration analysis will confirm a misaligned coupling. If a shutdown is possible, dial indicators or laser-alignment devices can be used and the misalignment can be corrected then and there.
Gearboxes
The lifeblood of any gearbox is the oil in it that lubricates the gears. If the oil level in a gearbox gets too low or loses its ability to lubricate, the gearbox will eventually fail, preceded by overheating. Traditionally, preventive maintenance for gearboxes has consisted of regularly checking their oil levels and replenishing lost oil. Some maintenance departments add a predictive element to gearbox maintenance in the form of oil sampling and analysis. Oil analysis, usually performed by an outside laboratory, reveals if the oil in a gearbox has lost its ability to lubricate and will detect any metal particles in the oil, a telltale sign of gear wear that foreshadows a possible failure.
These gearbox maintenance measures are time consuming and expensive and require shutting down the equipment. Also, gearboxes often are inaccessible or in unsafe locations, making oil-level checking and oil sampling difficult. Fortunately, thermal imaging is an alternative PdM approach. Since gearboxes generally overheat before they fail, an IR camera can detect when a gearbox is running hotter than normal and/or hotter than similar gearboxes performing similar work in similar environments.
Because thermography is a non-contact, non-destructive technology, even inaccessible gearboxes in dangerous locations can be scanned while they are running. Capture thermal images as well as visible-light digital images of all critical gearboxes that are running hotter than normal. Look, too, for leaking seals. Thermal images can reveal hot oil running down gearbox cases.
Be aware that while all excessive heat generated in mechanical gearboxes is the result of friction but may have a source other than inadequate lubrication. For example, its source might be friction caused by faulty bearings, misalignment, imbalance, misuse, or just normal wear. Thermography is a good first step toward a complete analysis of a critical gearbox's condition.
Troubleshooting gearboxes
When you find an overheating gearbox, its thermal image may offer hints as to the cause of its abnormal operating temperature. For example, if an oil pump has failed, its inlet and outlet temperatures will be the same. But whatever the suspected cause of overheating, maintenance personnel can arrange to follow up by checking the oil level, oil quality and metal-particle content of the oil or perform acoustical testing or vibration analysis.
In general, it is a good idea to create a regular inspection route that includes all critical motor/drive combinations. Then, save a thermal image of each one on a computer and track measurements over time, using the software that comes with the thermal imager. That way, you'll have baseline images to compare to, that will help you determine whether a hotspot is unusual or not, and, following repairs, to help you verify if the repairs were successful.