Kiln-drying wood is a 24/7 process. That is why Zena Forest Products mill owner Ben Deumling was so anxious to ensure that the new dry kiln he was setting up was as energy-efficient as possible. Deumling started with a 24-foot kiln built from a repurposed refrigerated shipping container, and installed a set of three ¼-horsepower single-phase fans to move the warm air over the wood.
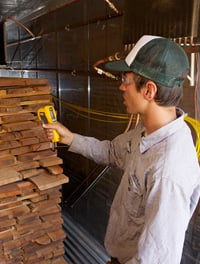
That setup worked well enough but was too small to handle the growing capacity of the Zena mill, so he built a larger kiln from a 40-foot container. In the larger kiln he installed five ½-horsepower three-phase fans to increase the airflow. The stainless steel and aluminum interiors and insulated construction made the refrigerated container ideal for a humid acidic environment. In addition to the fans he added a small pump to move hot water through the radiators to generate the warm air for the fans to distribute.
However, since the fans in the larger kiln required three-phase power, Deumling needed to convert the single-phase power coming into the mill to three-phase power to power the fans. Those fans run 24/7 during the drying period, so he did not want to add that load to the large rotary phase converter.
"The rotary phase converter is designed to run a 30-horsepower motor, so the extra amp draw at idle over the course of days and weeks would add up," says Deumling. "Also, running the rotary phase converter around the clock for the dry kilns would dramatically increase the duty cycle and increase the maintenance required for bearings and capacitors."
Sizing the solution to the job
After researching his options, Deumling installed a variable frequency drive (VFD) to convert single-phase power to three-phase power for the five fans in the large kiln. Typically VFDs are set up to run a single motor, but he did some research and found that he could use a VFD sized specifically for the combined load of the five fans. "I first looked at buying five small VFDs, but since all the fans are at the exact same duty cycle and running at exactly the same speed, I decided it was a better idea to buy one big VFD and program it to run all five fans," says Deumling.
He installed a relay for each fan motor that trips if the motor overheats. Those five relays are wired in series back to a control circuit on the VFD. If any of the motors has an issue, the VFD shuts everything down. Deumling used his Fluke 87V Industrial Multimeter to verify current in the relay circuit and to check to make sure that tripping the relays did in fact cut the current off. He makes sure that the system is de-energized and the capacitors have been discharged and disconnected before he tests with the 87V.
Consistent performance and energy savings
Once installed, the VFD allowed Deumling to control the speed of the fans at various points in the drying process. "During the last ten days of the four-week drying cycle, the fans are much less critical. With the VFD, I can turn down the RPMs of the fans and save a significant amount of electricity," Deumling says.
During those last stages, he reduces the amp draw from 11 amps to 8 amps, which reduces energy use by about 27 percent. But that wasn't the only savings. By installing the VFD, Zena Forest Products also got a cash rebate from Energy Trust of Oregon. Energy Trust is an independent nonprofit organization that helps individuals and businesses benefit from saving energy by reducing costs and building a sustainable energy future.
Additional information
Watch a video showing capacitor troubleshooting at Zena Sawmill