Temperature sensors are often calibrated to ensure product quality, maintain proper flow or to meet safety requirements. Degradation of sensors, which can be exposed to temperature cycling as well as vibration, can be accounted for during the tests.
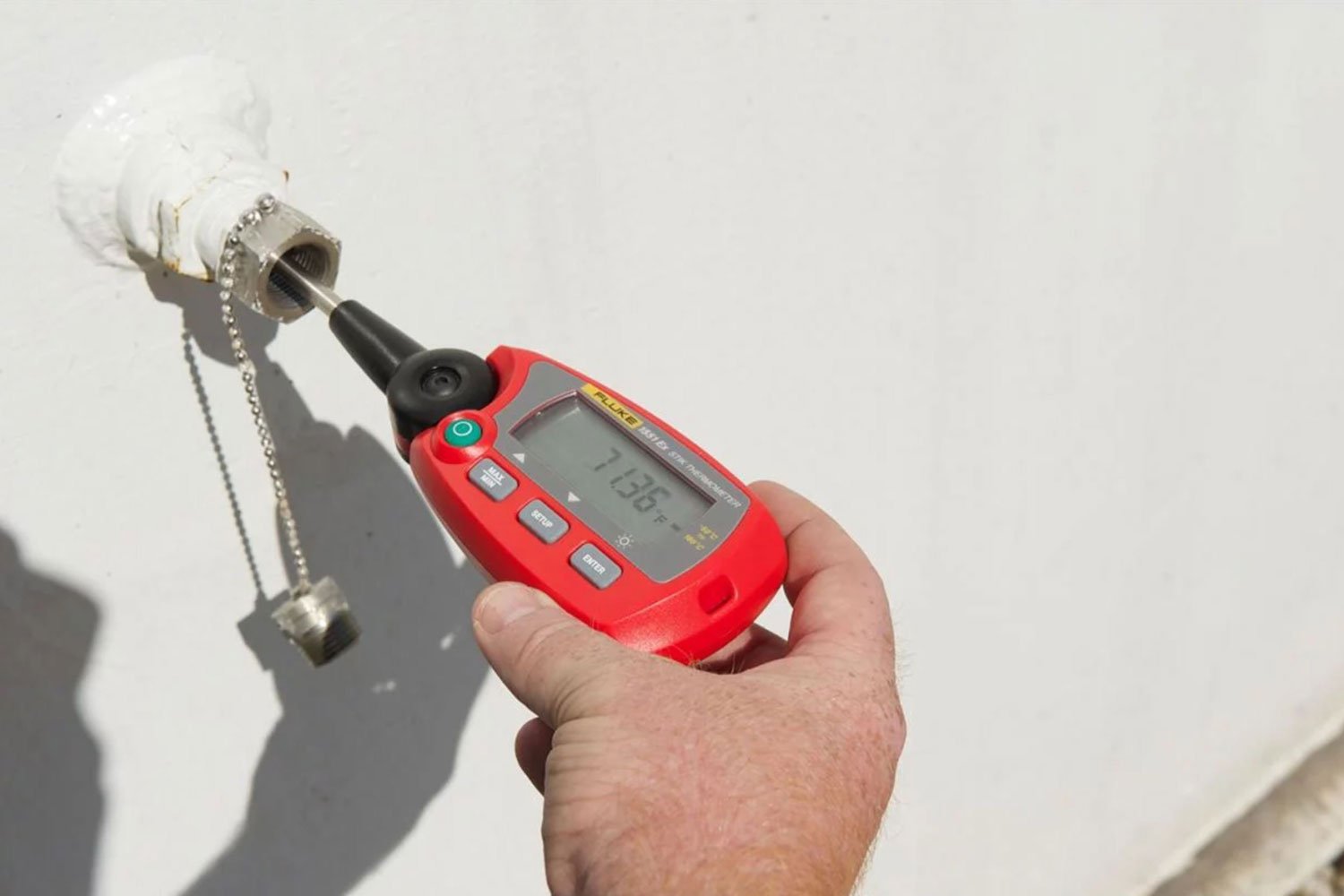
Indeed, the cost of not calibrating temperature equipment can be extreme—inferior products, unscheduled equipment downtime, regulatory penalties and even potentially tragic accidents with tremendous legal liability.
The type of sensor used often depends on accuracy requirements. For example, RTDs (resistance temperature detectors) and PRTs (platinum resistance thermometers) are used when a high degree of accuracy is important. Thermocouples are inexpensive and can be used over wider temperature ranges but are less accurate than PRTs or RTDs.
Whether a PRT, TC or RTD, testing the sensor is an important practice in complete temperature calibration. Testing the sensor and transmitter together verifies sensor and transmitter electronics adding a test of the control system input completes a full loop calibration.
Fluke offers temperature calibration tools well suited to the rigorous demands of industry, including specialty handheld temperature calibrators and the more advanced — but still portable — dry-block metrology wells with accredited calibration accuracy.
Intrinsically safe "Stik" thermometers, such as the Fluke 1551A, is precise enough to act as a reference thermometer and were designed with the oil and gas, chemical processing and other potentially explosive environments in mind.
Pairing a Fluke dry well with a handheld documenting calibrator allows for a complete field temperature calibration solution. You can test the entire tempeloop—the temperature sensor and all measurement electronics—in order to optimize performance.
Most advanced Fluke documenting process calibrators can also test and calibrate both temperature and pressure instruments. That keeps the number of instruments a technician needs to carry to a minimum.