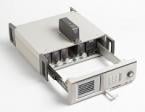
From a high level view, all pressure calibration systems perform these actions:
- Generate and control a pressure.
- Measure the pressure.
- Observe and record the output of the device under test (DUT).
In a traditional pressure calibration system, one device performs more than one of these functions. In a modular system, each function is performed by a separate module. Why might you prefer a modular solution?
Why might you prefer a modular solution?
- You have a wide workload to calibrate. Pressure calibrators come in a variety of pressure ranges. If you need to cover multiple ranges, you might need to purchase multiple traditional systems to calibrate them. With a modular system, you can purchase measurement modules to cover the ranges you need. Ideally, your modular system could accommodate multiple modules with multiple ranges simultaneously.
- Your workload changes over time. This year you may need to go up to 7 MPa (1000 psi). But next year you may need to go to 20 MPa (3000 psi) or even 107 MPa (15 500 psi). A modular system is easier to expand than a traditional system.
- You can’t afford downtime. At some point, your calibrator has to be calibrated, and while that is happening you can’t use it. With a modular system you have options to reduce or even eliminate downtown. For example, you can purchase spare modules, or stagger module calibration so some are out for calibration while others are still in use.
Fluke Engineer Demonstrating the Calibration of a Dial Gauge using the Fluke 8370A High Pressure Controller / Calibrator
Things to look for in a modular system
- The calibrator must be able to accommodate multiple modules with multiple ranges simultaneously, to maximize your workload coverage.
- Each module must fully encapsulate its particular function and all steps necessary to perform it, otherwise the modules become dependent on each other the modularity is lost.
- Modules must be quick and easy to swap out.
- Modules must have the required accuracy and performance for your application.
- System cost should be split across the modules. For example, if the module represents 80 to 90 percent of the system’s cost, then it would not be economical to purchase additional modules.
- System calibration should be on the modular level, allowing the module to provide the same output when it is removed from the chassis and installed in a different chassis or calibration sled.
If you decide that a modular system is the right solution for you, you will want to learn more about the Fluke Calibration family of modular pressure controller/calibrators:
- The 8270A measures and controls pressures from vacuum to 44 MPa (6400 psi). It can be configured with ranges as low as 100 kPa (15 psi). Fluke Calibration’s unique control technology enables you to use the 8270A at low or high pressures, all in the same instrument. Control precision is 0.002% of active range.
- The 8370A measures and controls pressures from atmosphere to 107 MPa (15 500 psi). It can be configured with ranges as low as 700 kPa (100 psi). Fluke Calibration’s unique control technology enables you to use the 8370A at low or high pressures, all in the same instrument. Control precision is 0.002% of active range.
- The 6270A features pressure ranges from low differential pressure to 20 MPa (3000 psi). Three levels of accuracy, 0.02 % FS, 0.01 % reading from 50% to 100 % or 0.01 % reading from 30 % to 100 %, let you balance your need for accuracy with the limits of your budget.
- The 2271A features pressure ranges from low differential pressure to 20 MPa (3000 psi). Two levels of accuracy, 0.02 % FS and 0.01 % reading from 50 % to 100 %. Its unique form factor and Electrical Measurement Module simplify calibration and testing of analog dial gauges and pressure transmitters.