Au cours des 45 dernières années, l'entreprise Linamar Corporation, basée à Guelph, dans l'Ontario, au Canada, a acquis dans le monde entier la réputation bien méritée de concepteur de classe mondiale et de fabricant diversifié de composants métalliques de précision et de systèmes pour le secteur automobile, le secteur de l'énergie et pour le marché industriel mobile.
Au début de l'année 2011, l'Advanced Systems Group (ASG) de l'entreprise a été contacté par le groupe de fabrication Linamar Camtac à propos d'un problème récurrent sur les moteurs de compresseur. Il semblait que les moteurs des trois compresseurs d'air 300 ch de l'usine étaient tous tombés en panne à un moment donné dans les trois ou quatre années précédentes. Les moteurs étaient relativement neufs, ils avaient été mis en service à l'ouverture de l'usine en 2002. Ils étaient tous révisés régulièrement, il était donc peu probable qu'il tombe en panne, mais que les trois tombent en panne en si peu de temps l'était encore moins. « Une panne, c'est un hasard, deux, une coïncidence, mais au bout de trois fois, on se doute qu'il y a anguille sous roche », affirme Leigh Copp, l'ingénieur en chef et responsable de la division opérationnelle de Linamar Advanced Systems Group.
Le coût de rebobinage des moteurs se situe en moyenne entre 6 000 et 8 000 $ chacun. Il faut également ajouter le coût de temps d'arrêt. « Si un temps d'arrêt non programmé est inévitable pour remplacer un moteur tombé en panne, vous risquez de perdre facilement des dizaines ou des centaines de milliers de dollars d'un coup », ajoute Copp.
Non seulement cela coûte cher, mais en plus une panne soudaine de compresseur peut être contagieuse. Les problèmes de faible pression qui en découlent peuvent provoquer des pannes sur d'autres machines de l'installation. « Généralement, pour qu'une installation fonctionne, il faut trois choses : de l'électricité, de l'air comprimé et de l'eau de refroidissement, explique Copp. Si l'une d'elles tombe en panne, tout s'arrête. Cette défaillance peut coûter très cher. »
Linamar a eu de la chance. Les moteurs n'étant pas en panne simultanément, l'équipe pouvait continuer à travailler pendant les réparations. Mais lorsque le troisième moteur est tombé en panne, Camtac a demandé à l'ASG de l'aider à trouver la cause du problème. L'ASG supervise et dépanne des problèmes particulièrement complexes dans les 25 usines de l'entreprise dans la région de Guelph ainsi qu'aux États-Unis, au Mexique, en Allemagne, en Hongrie, en France et en Chine.
Suivre les indices

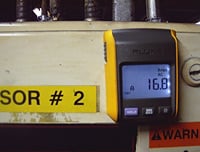
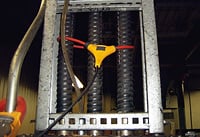
L'alimentation entre dans l'usine Camtac par le biais d'un transformateur de 5 000 kVA qui fournit une alimentation principale de 5 000 A et 600 V. Les alimentations secondaires de 1 200 A sont alors distribuées dans les usines, y compris celle qui alimente les trois compresseurs en question. Le support des câbles d'alimentation secondaire porte deux câbles à un conducteur parallèles pour chacune des trois phases et un fil de masse au milieu du support.
Copp et son équipe ont commencé leur inspection des moteurs de compresseurs à l'aide d'une pince multimètre Fluke 381 avec iFlex pour mesurer les tensions et courants. « Nous avons observé qu'il existait un faible déséquilibre, peut-être de 1 ou 2 %, dans la tension du moteur et un déséquilibre de près de 10 % dans le courant du moteur, ce qui peut provoquer une surchauffe importante », dit Copp.
Les ingénieurs étaient perplexes car, généralement, un déséquilibre de tension de 1 % n'entraîne pas un déséquilibre de courant de 10 %. Ils ont mesuré la tension au niveau de la distribution principale et ont constaté qu'il était bien équilibré ; le déséquilibre de 1 ou 2 % présent dans l'alimentation secondaire n'était pas présent au niveau de l'alimentation principale. Ils ont alors effectué un examen plus approfondi à l'aide d'une Pince multimètre de mesure de la qualité du réseau électrique Fluke 345 pour rechercher des harmoniques dans le courant du moteur, mais n'ont trouvé que très peu de distorsions harmoniques. Ils ont également testé l'isolement du moteur de compresseur à l'aide d'un testeur d'isolement numérique Fluke 1550B et n'ont observé aucune détérioration, ni aucun problème d'isolement.
Ils ont ensuite comparé les moteurs récemment rebobinés aux moteurs en service et ont remarqué que la résistance entre les phases avait une meilleure correspondance sur les nouveaux moteurs. Cela les a amenés à penser que les moteurs en services étaient soumis à un effet de chaleur qui endommageait les enroulements.
Détecter un courant à la terre élevé
En allant des moteurs à l'alimentation secondaire, l'équipe a observé un courant à la terre très élevé (environ 160 A) circulant dans le câble entre l'alimentation secondaire 1 200 A et l'alimentation principale. « Même si une valeur de 160 A est autorisée, il ne devrait généralement pas y avoir de courant à la terre, à moins qu'il n'y ait une fuite », déclare Copp.
L'équipe a ensuite vérifié que la prise neutre est solidement attachée et que les raccords de terre fonctionnaient correctement. Ils ont également utilisé le testeur de terre GEO Fluke 1625 pour vérifier que la grille de terre était présente et qu'elle fonctionnait correctement.
Cependant, lorsqu'ils ont mesuré les courants à la terre qui circulent entre chaque compresseur d'air à travers le support de câbles et le tuyau d'air métallique, avec le Fluke 381, ils ont découvert d'autres mauvais signes. « Ces mesures révèlent de multiples chemins de terre avec une quantité importante de courant circulant entre chaque compresseur, dit Copp. Nous avons utilisé un ScopeMeter® Fluke 190-204 avec quatre transducteurs de courant à enroulement Rogowski pour mesurer l'amplitude et la phase des composants des courants à la terre qui circulent dans les conducteurs et dans le support de câbles adjacent. Il est devenu évident que certains effets inductifs favorisaient le courant à la terre et que ces courants pouvaient favoriser le déséquilibre de la tension dans l'alimentation secondaire. »
Les mesures effectuées au niveau de l'alimentation principale indiquaient qu'un courant à la terre de près de 200 A circulait dans les différents fils de mise à la terre au niveau du service. À ce moment-là, ils n'ont pas pu aller plus loin, jusqu'à la prochaine fermeture planifiée de l'usine. En attendant, Copp et deux autres ingénieurs ont passé beaucoup de temps à faire des croquis des scénarios possibles et à analyser la source probable du courant. Ils soupçonnaient la présence d'une boucle de terre dans laquelle le courant à la terre était induit par des courants de phase.
Test de la cause présumée
À la fin décembre 2011, Copp et son équipe ont profité d'un arrêt de 8 heures de l'usine de Camtac pour effectuer le plus de tests statiques possible afin de découvrir l'origine du problème. Ils ont vérifié l'absence de conducteurs cassés dans le câble entre l'alimentation secondaire et l'alimentation principale. Ils ont mesuré la résistance des câbles parallèles à l'aide d'un micro-ohmmètre et ont constaté qu'ils correspondaient les uns aux autres. Ils ont également retiré et nettoyé toutes les connexions de masse, de liaison et de conducteur de phase.
Une fois que l'usine a été remise en service, le courant à la terre élevé était cependant toujours présent.
Grâce aux tests effectués pendant le temps d'arrêt, l'équipe de l'ASG a conclu que le problème provenait de l'agencement des conducteurs entre l'alimentation principale et l'alimentation secondaire de 1 200 A. « Nous pensions que la position physique du conducteur de liaison dans le support était incorrecte, et que cela entraînait une interaction entre les champs magnétiques du conducteur de terre et du conducteur de phase, ce qui provoquait un courant à la terre, dit Copp. Le conducteur de terre était placé conformément aux conseils des fabricants de câbles et aux codes NEC/CEC, mais cette recherche laisse penser que ceux-ci devraient peut-être être reconsidérés. »
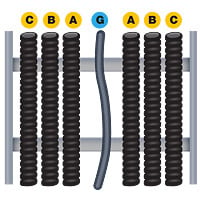
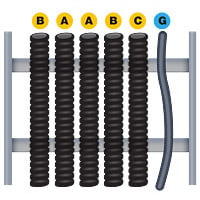
En poursuivant les tests, l'équipe de l'ASG et celle de Camtac supposaient que rapprocher le conducteur de terre du rail de côté du support de câbles permettrait d'atténuer les courants à la terre induits. Mais pour cela il fallait couper l'alimentation des compresseurs. Là encore, ils ont attendu le moment opportun où la production pouvait être arrêtée pendant quelques heures. Quelques mois plus tard, cette occasion s'est présentée : les ingénieurs de Camtac se sont alors occupés du déplacement.
Juste après la remise en fonctionnement, les ingénieurs ont mesuré les courants à la terre et le courant du rail de côté.
Une réduction important du courant à la terre a été immédiatement observée après le déplacement du conducteur de terre. « Nous continuons de surveiller le système pour voir si les effets se sont améliorés sur le long terme et si la dégradation des bobines moteurs est réduite. Pour l'instant nous n'avons pas détecté d'augmentation du courant à la terre, ni aucune autre panne du moteur de compresseur. Nous continuons de surveiller l'installation afin de vérifier comment le moteur fonctionne dans le temps. »
Équipement | Courant | |
---|---|---|
Avant le déplacement | Après le déplacement | |
Conducteur de mise à la terre | 160 A | 45 A |
Rail de côté du support de câbles | 70 A | 20 A |