Les moteurs électriques sont l´élément clé de nombreux procédés industriels. Ils peuvent représenter jusqu’à 70 % de l’énergie totale consommée sur un site industriel et consomment eux-mêmes jusqu’à 46 % de l’électricité générée à l’échelle mondiale. De par leur rôle fondamental dans les procédés industriels, le coût entraîné par les temps d'arrêt dus aux moteurs défectueux peut atteindre des dizaines de milliers de dollars par heure. S´assurer du fonctionnement efficace et sûr des moteurs est l´une des tâches les plus importantes que doivent accomplir les techniciens et ingénieurs de maintenance quotidiennement.
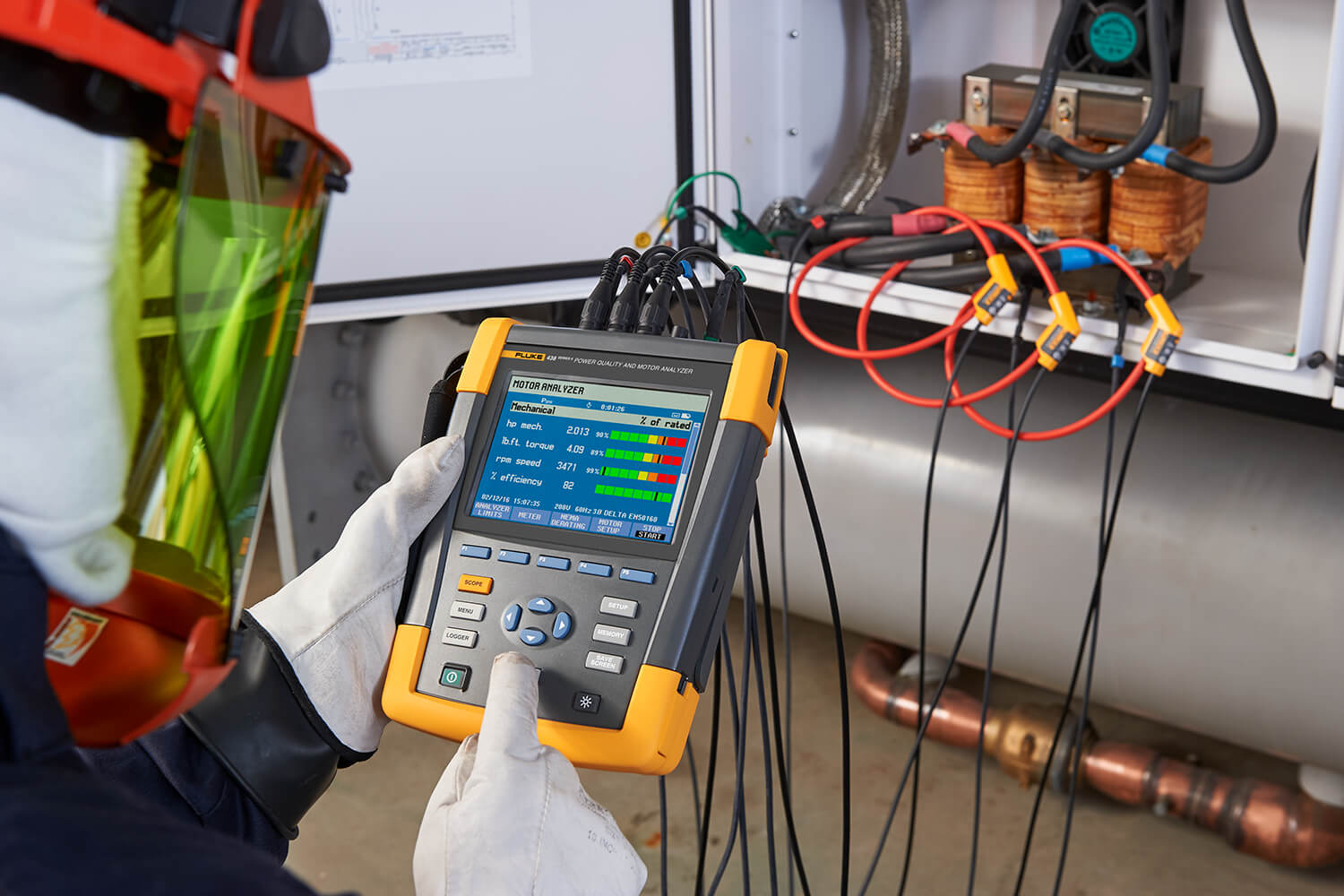
Une utilisation efficace de l'électricité n'est pas un simple « plus ». Dans de nombreux cas, l'efficacité énergétique peut faire la différence entre rentabilité et pertes financières. Étant donné que les moteurs consomment une partie importante de l'énergie dans l'industrie, ils sont devenus la pierre angulaire des économies potentielles et du maintien de la rentabilité. En outre, la volonté d'identifier des économies en améliorant l'efficacité et de réduire la dépendance vis-à-vis des ressources naturelles conduit de nombreuses entreprises à adopter certaines normes du secteur, telles que la norme ISO 50001. Cette norme définit un cadre et des exigences pour établir, mettre en œuvre et maintenir un système de gestion de l'énergie en vue d'assurer des économies durables.
Méthodes d'évaluation traditionnelles du moteur
La méthode traditionnelle pour mesurer les performances et l'efficacité d'un moteur électrique est bien définie, mais le processus peut s'avérer coûteux à mettre en place et difficile à intégrer aux procédures de travail. En réalité, les contrôles de performance des moteurs nécessitent très souvent un arrêt total du système, ce qui est susceptible d'entraîner des temps d'arrêt coûteux. Pour mesurer l'efficacité d'un moteur électrique, la puissance électrique d'entrée et la puissance mécanique de sortie doivent toutes deux être vérifiées dans une grande variété de conditions de fonctionnement dynamiques. La méthode traditionnelle de mesure exige, dans un premier temps, des techniciens qu'ils installent le moteur sur un banc d'essai. Le banc d'essai se compose du moteur testé, monté sur un générateur ou un dynamomètre.
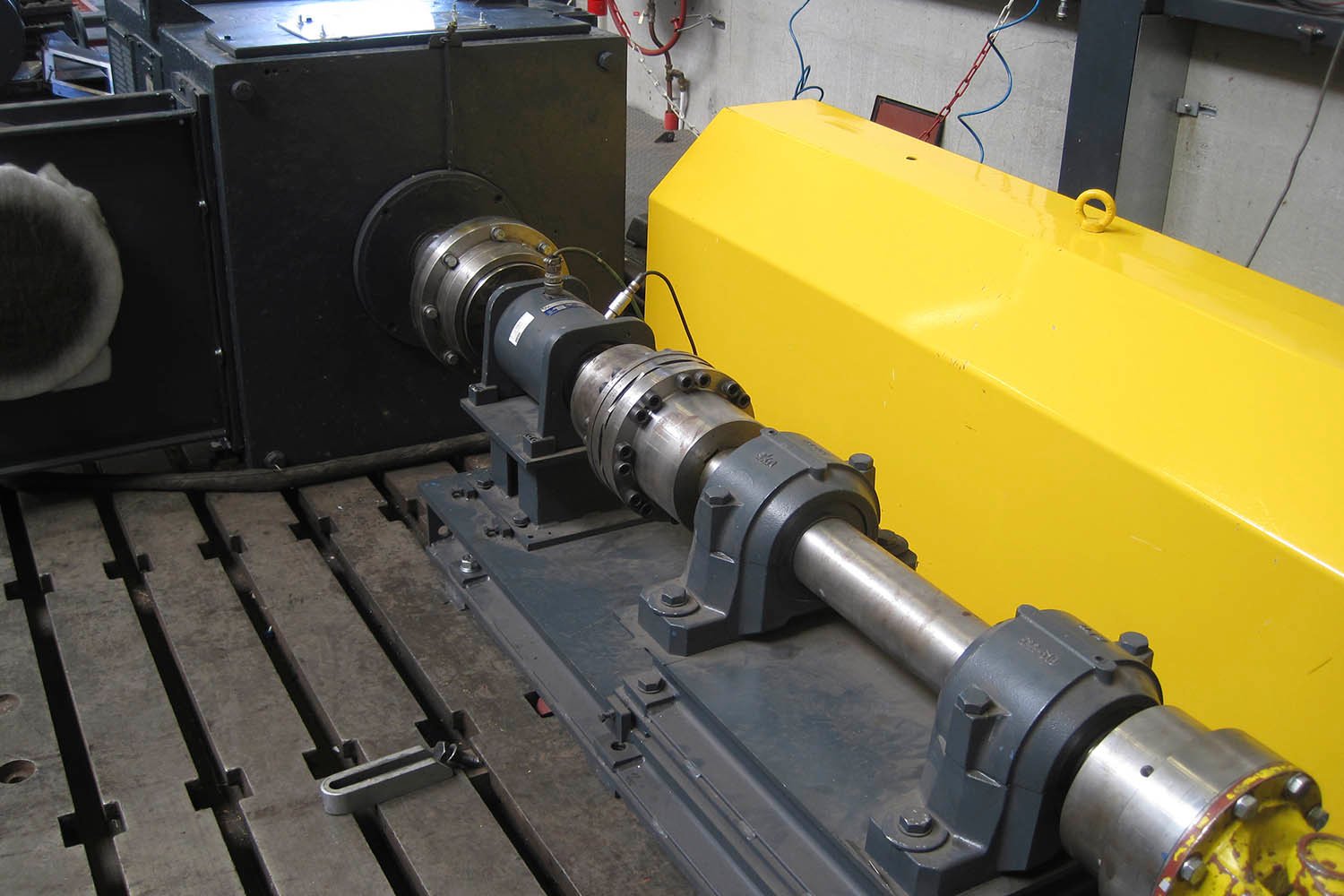
Le moteur testé est ensuite relié à la charge par un arbre. Un capteur de vitesse (tachymètre) est fixé à l'arbre, qui comporte en outre un ensemble de capteurs de couple dont les données permettront de calculer la puissance mécanique. Ce système fournit des informations sur la vitesse, le couple et la puissance mécanique. Certaines installations permettent également de mesurer la puissance électrique afin de calculer l'efficacité du moteur.
L'efficacité est calculée comme suit :
ɳ(efficacité) =
Puissance mécanique
Puissance électrique
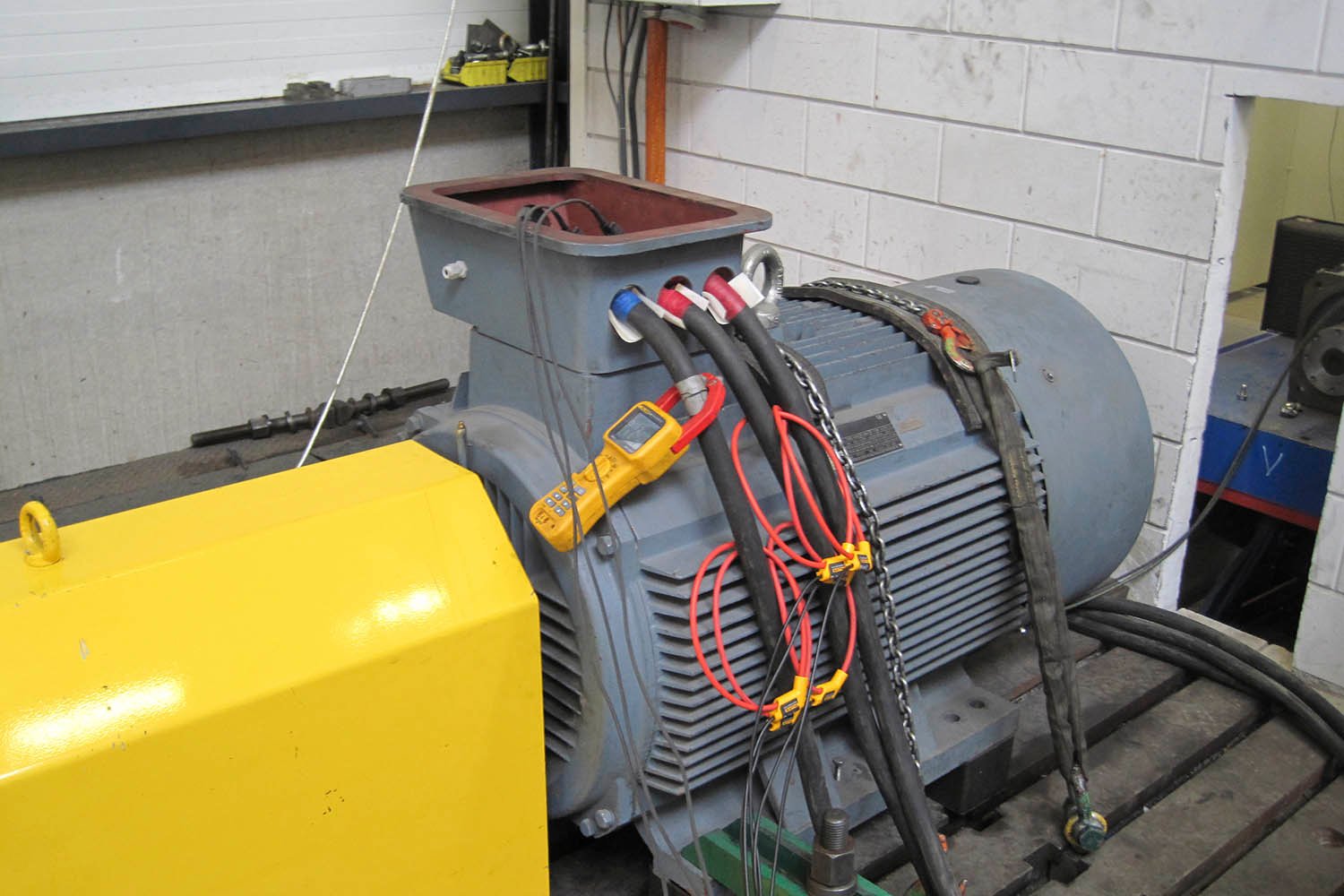
Pendant le test, la charge varie en vue de déterminer l'efficacité du moteur avec différents modes de fonctionnement. Le banc d'essai peut sembler simple, mais il implique quelques inconvénients inhérents au système :
- Le moteur doit être mis hors service.
- La charge du moteur n'est pas vraiment représentative de la charge réelle du moteur lorsque celui-ci est en service.
- Sur toute la durée du test, le fonctionnement doit être interrompu (ce qui implique un temps d'arrêt) ou un moteur de remplacement doit être installé temporairement.
- Les capteurs de couple sont coûteux et présentent une plage de fonctionnement limitée, si bien qu'il faudrait plusieurs capteurs pour tester les différents moteurs.
- Un banc d'essai capable de couvrir une large gamme de moteurs est onéreux et les utilisateurs de ce type d'équipement sont généralement des entreprises spécialisées dans la conception ou la réparation de moteurs.
- Les conditions « réelles » de fonctionnement ne sont pas prises en compte.
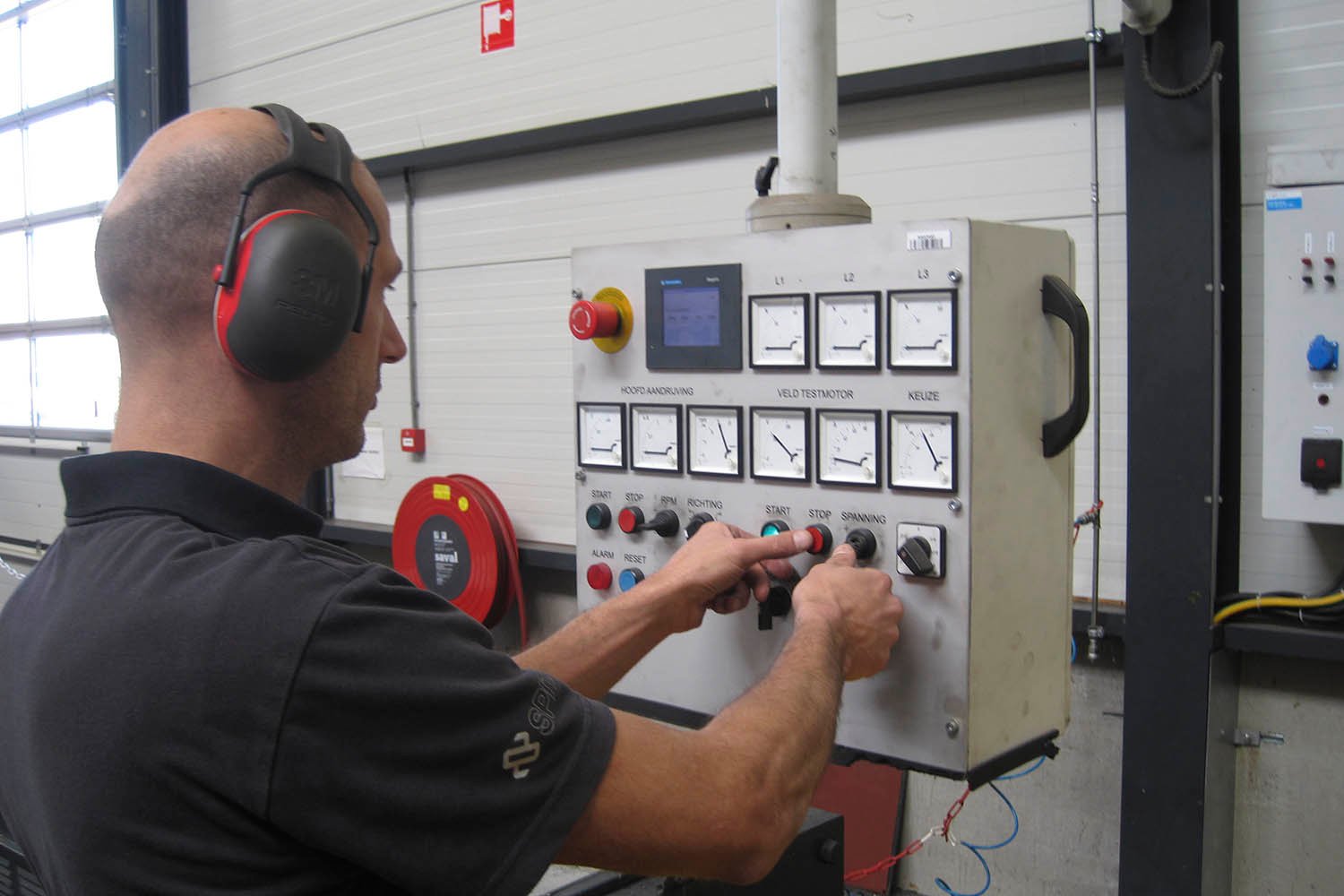
Paramètres des moteurs électriques
Les moteurs électriques sont conçus pour des types d'applications spécifiques en fonction de la charge et, à ce titre, chaque moteur possède des caractéristiques qui lui sont propres. Ces caractéristiques, classées selon les normes NEMA (National Electrical Manufacturers Association) ou CEI (Commission électrotechnique internationale), ont des conséquences directes sur le fonctionnement et l'efficacité du moteur. Chaque moteur comporte une plaque signalétique qui indique ses principaux paramètres de fonctionnement et les informations relatives à son efficacité, conformément aux recommandations de la NEMA ou de la CEI. Les données de la plaque signalétique peuvent ensuite être exploitées pour comparer les exigences du moteur avec les conditions réelles dans lesquelles il est utilisé. Par exemple, en comparant ces valeurs, vous pouvez découvrir qu'un moteur dépasse la vitesse prévue ou la limite du couple, ce qui risque d'écourter la durée de vie du moteur ou de causer des défaillances prématurées. D'autres effets, comme le déséquilibre de tension ou de courant, ou encore la création d'harmoniques dûs à une mauvaise qualité du réseau électrique, peuvent également affecter les performances du moteur. Si l'un ou l'autre de ces phénomènes apparaît, le moteur doit être « déclassé », c´est-à-dire que la performance attendue de ce moteur doit être réduite. Le risque qui en découle est une interruption du processus si la puissance mécanique produite n'est pas suffisante. Le déclassement est calculé à partir de la norme NEMA, en fonction des données spécifiées pour le type de moteur concerné. Les normes NEMA et CEI présentent quelques différences, mais suivent globalement la même approche à ce sujet.
Conditions réelles de fonctionnement
Évaluer un moteur électrique sur un banc d'essai signifie généralement que le moteur est testé dans les meilleures conditions possible. Or, lorsque le moteur est utilisé sur site, il ne jouit généralement pas des « meilleures » conditions d'exploitation. Toutes ces variations du mode de fonctionnement contribuent à la dégradation de la performance des moteurs. Par exemple, au sein d'un même site industriel, diverses charges peuvent être mises en place et avoir un effet direct sur la qualité du réseau électrique, provoquant par là même un déséquilibre dans le système ou la création d'harmoniques. Chacune de ces configurations peut impacter sérieusement les performances des moteurs. En outre, la charge entraînée par le moteur risque de ne pas être optimale ou compatible avec la valeur de charge initialement prévue pour ce modèle. La charge peut être trop élevée pour être gérée correctement par le moteur, voire surchargée en cas de contrôles insuffisants du processus. Elle peut même être entravée par des frictions excessives causées par un corps étranger bloquant la turbine d'une pompe ou d'un ventilateur. La détection de ces anomalies peut s'avérer difficile et chronophage en vue d'une résolution efficace des problèmes.
Nouvelle approche
L'analyseur de moteur et de la qualité du réseau électrique Fluke 438-II offre une méthode rationalisée et rentable pour évaluer l'efficacité des moteurs en évitant les temps d'arrêt coûteux et le recours à des capteurs mécaniques externes. Le Fluke 438-II, inspiré des EnergiMètres et analyseurs de qualité du réseau électrique Fluke 430 série II, a la pleine capacité d'évaluer la qualité du réseau électrique tout en mesurant les paramètres mécaniques des moteurs électriques à démarrage direct. En associant les données de la plaque signalétique (données NEMA ou CEI) aux mesures de la puissance triphasée, le Fluke 438-II calcule les performances du moteur en temps réel, notamment la vitesse, le couple, la puissance mécanique et l'efficacité, sans nécessiter de couple supplémentaire ni de capteurs de vitesse. Le 438-II calcule aussi directement le facteur de déclassement du moteur en fonction du mode de fonctionnement.
Les données nécessaires au Fluke 438-II pour effectuer ces mesures sont saisies par le technicien ou l'ingénieur. Elles comprennent la puissance nominale en kW ou ch, la tension nominale et le courant, la fréquence nominale, le facteur de puissance ou cos φ, le coefficient de service nominal et le type de conception du moteur (à partir des classes NEMA ou CEI).
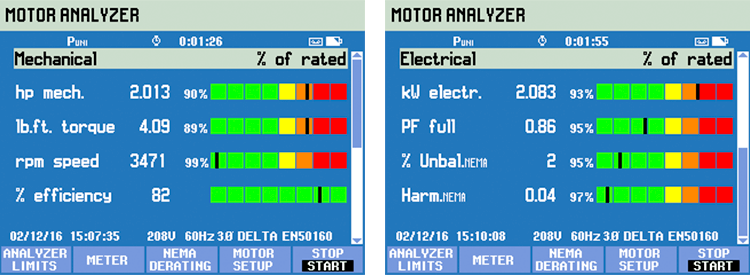
Principes de fonctionnement
Le Fluke 438-II fournit des mesures mécaniques (vitesse de rotation du moteur, charge, couple et efficacité) en appliquant des algorithmes propriétaires aux signaux de forme d'onde électriques. Les algorithmes recoupent plusieurs modèles basés sur la physique et sur des données d'un moteur à induction sans requérir aucune des mesures généralement nécessaires en amont pour estimer les paramètres du modèle du moteur, comme la résistance du stator. La vitesse du moteur peut être évaluée à partir des harmoniques du rotor présents dans les formes d'onde de courant. Le couple de l'arbre du moteur peut être associé à la tension et au courant des moteurs à induction et réduit grâce à des relations physiques complexes bien connues. La puissance électrique est mesurée à l'aide des formes d'onde d'entrée du courant et de la tension. Une fois les estimations du couple et de la vitesse obtenues, la puissance mécanique (ou charge) est calculée à partir des deux valeurs. L'efficacité du moteur est calculée en divisant la puissance mécanique estimée par la puissance électrique mesurée. Fluke a procédé à une série de tests approfondis en utilisant des moteurs pour entraîner des dynamomètres. La puissance électrique réelle, le couple de l'arbre et la vitesse du moteur ont été mesurés et comparés aux valeurs enregistrées par le Fluke 438-II afin de déterminer le niveau de précision de l'appareil.
Résumé
Si les méthodes traditionnelles permettant de mesurer les performances et l'efficacité des moteurs électriques sont bien définies, elles ne sont pas nécessairement mises en œuvre à grande échelle. Ce constat est en grande partie dû aux coûts des temps d'arrêt, autrement dit à l'interruption des moteurs, et parfois même des systèmes entiers, à des fins de test. Le Fluke 438-II fournit des informations très utiles qui, jusqu'à maintenant, étaient extrêmement difficiles et coûteuses à obtenir. En outre, le Fluke 438-II utilise ses capacités avancées d'analyse pour mesurer la qualité du réseau électrique pendant que le système fonctionne en conditions réelles. L'opération majeure qui consiste à mesurer l'efficacité des moteurs est simplifiée du fait que l'appareil élimine le recours à un couple externe et à des capteurs de vitesse distincts. Il devient ainsi possible d'analyser le rendement de la plupart des processus industriels entraînés par moteur alors qu'ils sont en fonctionnement. Ce système permet aux techniciens de réduire les temps d'arrêt et de déterminer l'évolution des performances d'un moteur au fil du temps, et donc de mieux appréhender la santé et les performances globales du système. En estimant ces performances, il devient possible de déceler les changements susceptibles d'indiquer une panne imminente du moteur et, par conséquent, de procéder à son remplacement en temps utile.