Pour réaliser des économies d´énergie, les bonnes intentions doivent être appuyées par un plan efficace. La gestion énergétique n´est pas un simple vœu pieux aux Etats-Unis. L´objectif est de : Réduire la consommation d´énergie globale, ou maintenir la consommation tout en augmentant la quantité produite par kW utilisé.
Le plan ? C´est parfois là que se trouve le problème.
Dans le secteur de la fabrication, un plan fonctionne quand il combine une vision guidée par la sagesse de l´expérience et les chiffres du retour sur investissement pour soutenir l´effort. Quand il s´agit d´énergie, les responsables d´installations industrielles ne disposent pas des travaux de recherche nécessaires pour les aider à définir des bases de références quant à une consommation « raisonnable » d´énergie dans une usine de fabrication. Alors, comment estimer quelle part d´énergie actuellement utilisée est raisonnable ou gaspillée et, sur cette énergie gaspillée, comment savoir quelle installation propose un retour sur investissement suffisamment important pour que cela en vaille la peine ?
Ici, le retour sur investissement en question est le coût au kWh, tel qu´il est facturé par le fournisseur. Ces unités possèdent des taux différents selon le moment de la journée et de l´année. Les économies à réaliser correspondent à la baisse de ces dépenses. L´investissement correspond aux matériaux et à la main-d´œuvre requis pour modifier la consommation d´énergie. Le retour sur investissement est le temps nécessaire pour que les économies réalisées sur la facture d´électricité remboursent l'investissement. Le profit commence lorsque toutes les dépenses sont payées.
Si l´on revient au plan, comment obtenir une estimation du retour sur investissement lorsqu´il n´existe pas de normes industrielles quant à la consommation raisonnable d´énergie ?
Profil de la consommation d´énergie dans une application industrielle
La consommation d´énergie dans une application industrielle varie en fonction de différents facteurs :
- âge de l´usine
- type et taille de la charge
- planning opérationnel, heures par semaine et intensité de la charge
- nombre d´employés
- climat
- philosophie de maintenance.
Voici la réponse : N´essayez pas de gérer chaque kW consommé par votre installation. C´est la partie « sagesse de l´expérience » de l´équation. Divisez l´installation en une infrastructure électrique, puis en systèmes clés.
Les économies d´énergie reposent sur deux tactiques fondamentales : (1) inspection générale des systèmes clés et (2) collecte de données ciblée, notamment des relevés de la consommation d'énergie au niveau des alimentations électriques principales et des charges clés.
Identifiez combien le système est censé consommer, déterminez sa consommation actuelle et identifiez les gaspillages, soit dans l'exploitation, horaires et types, soit au niveau de l´équipement ou du système. Pour réaliser des économies, l´installation doit s´attaquer au gaspillage, soit en modifiant son exploitation et sa maintenance, soit ses équipements et ses commandes.
Composantes énergétiques
Avant d´expliquer comment suivre la consommation d´énergie, revoyons notre définition et notre manière de mesurer l´énergie.
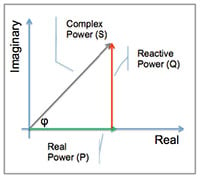
L´énergie est exprimée en puissance active, réactive et apparente (Figure 1).
Le flux d´énergie est décrit par :
- la puissance réelle (P) ou active en watts (W)
- la puissance réactive (Q) en voltampères réactifs (VAR)
- la puissance complexe (S) en voltampères (VA)
- la puissance apparente, magnitude de la puissance complexe (VA)
La relation mathématique entre la puissance réelle, réactive et apparente peut être représentée par des vecteurs ou exprimée avec des nombres complexes, S = P + jQ (j étant l´unité imaginaire).
La puissance réactive ne transfère pas d´énergie, aucun travail n´est produit ; elle est donc représentée en tant qu´axe imaginaire du diagramme vectoriel. La puissance réelle déplace de l´énergie ; il s´agit donc de l´axe réel.
La vitesse du flux d´énergie dans un système dépend de la charge : est-elle résistive, réactive, ou les deux ?
Avec une charge purement résistive, la polarité de la tension et du courant s´inverse en même temps, le produit de la tension et du courant est positif à chaque instant et seule la puissance réelle est transférée : du travail est produit.
Si la charge est purement réactive, la tension et le courant sont déphasés et leur produit peut être positif ou négatif, ce qui indique qu´une partie de l´énergie est transférée à la charge tandis qu´une partie est réacheminée. Le transfert net d´énergie vers la charge est de zéro : aucun travail n´est produit.
En réalité, les charges comportent une combinaison de résistance, d´inductance et de capacité électriques, ce qui crée de la puissance réelle et de la puissance réactive dans un système. Pour cette raison, les systèmes électriques sont conçus pour tolérer une certaine quantité de puissance réactive. Un problème se déclare lorsque trop de puissance réactive est générée. Non seulement il n´y a pas assez de puissance réelle pour produire le travail requis, mais la capacité globale de production de travail du système est compromise. C´est pourquoi les fournisseurs d´électricité pénalisent leurs clients si leurs charges produisent trop de puissance réactive : c´est de l´énergie gaspillée et inutilisable dont la création engendre des coûts. La plupart des factures d´énergie traquent les VAR (puissance réactive) et certaines calculent le facteur de puissance, qui évalue de combien un système est passé en dessous de la puissance réelle de 100 %. La plupart des fournisseurs exigent que leurs clients restent au-dessus de 0,95 FP (facteur de puissance).
Suivre la consommation d´énergie
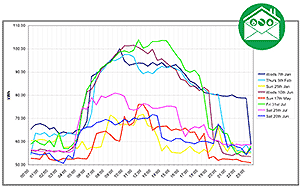
Comprendre les bases des composants de l´énergie permet à un électricien de mettre en place des équipements de relevé d'énergie pour mesurer le niveau global et la qualité de la consommation, puis de savoir quand et par quoi de l´énergie est consommée (Figure 2).
Relevez la consommation énergétique au niveau des panneaux principal et secondaire et au niveau des charges principales. Enregistrez les kW, les kWh et le facteur de puissance sur une période de temps représentative.
Cela vous fournit une idée très précise de la consommation d´énergie réelle sur des circuits et des charges triphasés.
Les plus grandes économies d´énergie reposent sur l´identification du pic de consommation, l´évaluation du facteur de puissance et de la consommation d´électricité globale par rapport aux factures du fournisseur et, lorsque cela est possible, du rééquilibrage de vos charges. Deux petites minutes de pic de consommation peuvent augmenter le coût de l´installation pendant quelques heures, jours ou semaines.
Replanifier les charges peut permettre à une entreprise de profiter des moments de la journée où l´énergie est moins chère. Vérifiez si votre facteur de puissance est fort en dessous de 1 et examinez vos factures d´électricité pour déterminer si vous êtes pénalisé en raison d´un facteur de puissance médiocre. Si c´est le cas, l´enregistreur de qualité d´énergie peut vous aider à repérer les sources du problème. Ensuite, après avoir effectué des améliorations éco-énergétiques, reconnectez l´enregistreur pour vérifier les avantages de vos améliorations en termes d´efficacité.
Comprendre les points de pertes énergétiques
Chaque système et exploitation peuvent potentiellement représenter un point de gaspillage qui peut être atténué ou rectifié. Il est bon de commencer par les sous-systèmes électriques, les systèmes d´air comprimé, de vapeur et électromécaniques spécifiques, mais chaque exploitation présente des points potentiels de gaspillage d´énergie qui doivent être mesurés.
Le but est de cartographier la consommation d´énergie de chaque équipement et processus spécifique pour rechercher les points de gaspillage d'énergie, quantifier l´énergie perdue et donner la priorité aux améliorations ou aux remplacements en fonction de la durée de vie de l´équipement et des modifications qui peuvent fournir le meilleur retour sur investissement.

La cartographie de la consommation d´énergie fournit également une référence à partir de laquelle il est possible de mesurer l'efficacité des projets relatifs à l´économie d´énergie pour justifier les coûts engagés (Figure 3).
Gaspillages courants dans les sous-systèmes électriques :
- Charges habituellement laissées actives après les heures normales ou en fonctionnement inutile pendant les heures de pointe.
- Absence de contrôle du moteur pouvant signifier une création de puissance de sortie plus importante que nécessaire.
- Conditions de surtension/surintensité provoquant une consommation électrique excessive en guise de compensation.
- Déséquilibre de phase entraînant une consommation d´électricité par la charge sinutilisable.
Identifier et quantifier :
- Effectuez une analyse thermique du tableau électrique et de la charge mécanique en cas de surchauffe.
- Relevez la consommation d´énergie au fil du temps : Quelle quantité d´énergie est consommée à quel moment de la journée et avec quelle quantité de pertes ?
Les gaspillages courants et les points à inspecter dans des systèmes électromécaniques.
- Une friction excessive résultant de problèmes d´alignement, de roulements, d´équilibrage et de desserrage entraîne une surcharge du moteur et une consommation d´électricité excessive.
- Les charges non contrôlées sont laissées actives après les heures normales, fonctionnent aux heures de pointe, créent une puissance de sortie plus importante que nécessaire et subissent les conditions de surtension/surintensité et de déséquilibre de phase.
- La consommation de vieux dispositifs mécaniques est tellement plus importante que celle des nouveaux modèles à haute efficacité, que la réduction de la consommation en kWh suffit à justifier un remplacement prématuré.
Identifier et quantifier :
- Effectuez une analyse thermique du tableau de commande et de la charge mécanique en recherchant les surchauffes, un signe sûr indiquant une inefficacité électrique.
- Relevez la consommation d´énergie au fil du temps : vérifiez la consommation totale en kWh, le facteur de puissance, la consommation de pointe, les déséquilibres et les harmoniques.
- Testez les niveaux de vibration conformément aux normes et identifiez les solutions de maintenance, telles que le rééquilibrage.
- Effectuez une analyse thermique des couplages/arbre/courroies, roulements et ventilateur.
- Vérifiez les niveaux de courant et de tension.
- Effectuez une analyse thermique du boîtier de terminaison/de raccordement et des enroulements, et effectuez des tests de résistance d´isolement.
Gaspillages courants et points à inspecter dans des systèmes d´air comprimé :
- Des fuites excessives dans les conduites d´air comprimé entraînent un fonctionnement superflu afin de maintenir l´alimentation.
- Les compresseurs maintenus en activité en dehors des heures d´utilisation gaspillent de l´énergie.
Identifier et quantifier :
- Effectuez un relevé énergétique au niveau du compresseur en guise de référence pour la consommation.
- Mesurez la pression au niveau du compresseur et du point d´utilisation pour déterminer le niveau de chute.
- Il est possible d´utiliser les ultrasons pour identifier les fuites.
Gaspillages courants et points à inspecter dans des systèmes à vapeur :
- Des purgeurs de vapeur défectueux combinés à une isolation insuffisante entraînent des pertes de vapeur, causant une surproduction pour maintenir l´alimentation nécessaire.
Identifier et quantifier :
- Effectuez un relevé énergétique au niveau d´une chaudière en guise de référence pour la consommation.
- Effectuez une analyse thermique des tuyaux et des purgeurs pour identifier les trous et les blocages au niveau de l´isolation
Valider le retour sur investissement
En raison de l´absence de normes dans l´industrie précédemment mentionnée, comment savoir quels systèmes possèdent le retour sur investissement le plus intéressant ? Les exemples de cas qui représentent des situations courantes sont nos meilleurs outils. Voici plusieurs exemples pour des systèmes industriels courants.
Inspection électromécanique
Type d´installation : usine de recyclage de l´acier en Allemagne
Type d´équipement : ventilateur à courroie, pour le refroidissement des procédés
Mesures prises : test des vibrations
Problèmes constatés : un déséquilibre modéré, un mauvais alignement ainsi qu´une usure de roulement.
Economies : Un rééquilibrage était nécessaire. Un moteur de 350 kW fonctionnait à 80 % de sa puissance nominale, la puissance mesurée était d´environ 280 kW. Après le rééquilibrage, la consommation d´énergie a été réduite de 3 %. Au prix de 0,11 euro/kWh, les économies annuelles ont atteint 8 094 euros.
Inspection air comprimé
Type d´installation : fabrication
Type d´équipement : circuit d´air comprimé
Mesures prises : inspection par ultrasons du circuit d´air comprimé (enregistrement complet recommandé des données du compresseur)
Problèmes constatés : la quantité d´air comprimé produite par rapport à la demande réelle.
Economies : Plusieurs points d´amélioration ont été détectés. Les économies annuelles totales sont de 50 600 $. Arrêt du compresseur les week-ends : économies annuelles de 32 700 $. Installation de solénoïdes pour couper la circulation d´air lorsque les machines sont arrêtées : économies annuelles de 7 100 $. Réparation de 36 fuites : économies annuelles de 4 800 $. Installation de filtres dans le système pour un coût de 6 000 $ ; économies annuelles de : 6 000 $.
Inspection du purgeur de vapeur
Type d´installation : fabrication
Type d´équipement : chaudières et conduites de vapeur
Mesures prises : inspection thermique des conduites de vapeur
Problèmes constatés : six purgeurs de vapeur ne fonctionnent pas correctement ; fuites de bobines dans les réservoirs de placage ; fuites de vapeur au niveau des conduites de placage ; opportunités de récupération des condensats
Economies : Six purgeurs défectueux ont été remplacés à un coût individuel de 500 $. Economies réalisées : 3 200 $ par purgeur grâce à des calculs de coût de génération de vapeur et de perte de chaleur connus. Economies totales : 16 200 $.
Etape suivante : Effectuer un relevé d´énergie au niveau du panneau d´alimentation de la chaudière avant et après réparation des fuites et des problèmes de condensats.
Productivité en hausse ou réduction de frais ?
Il est intéressant de répondre à la question suivante : Une fois que vous avez identifié un moyen de réduire la consommation d´énergie, utilisez-vous ces économies pour augmenter le rendement de l´usine (même consommation de kWh, mais production plus importante) ou pour d´autres stratégies commerciales (marges bénéficiaires, niveaux de prix) ?
Dans tous les cas, réduire la consommation d´énergie est une bonne affaire. En effectuant un relevé énergétique de chaque système majeur et en cartographiant les coûts par rapport aux factures du fournisseur d´énergie pour quantifier où et quand les consommations excessives ont lieu, les entreprises réalisent souvent des économies simplement en changeant leur exploitation et leurs plannings. En identifiant les équipements inefficaces ou obsolètes, les entreprises peuvent justifier et prioriser leur remplacement. De plus, en réduisant la consommation totale d´énergie, les entreprises réduisent leurs coûts opérationnels et augmentent ainsi leur compétitivité sur le marché.
Télécharger cet article au format PDF