Un electricista tenía un cliente con un problema muy habitual: uno de los paneles eléctricos se sobrecalentaba. Lo que hacía que la situación fuera inusual era el hecho de que el sobrecalentamiento no era el resultado de ninguna de las causas habituales.
Se llamó a un electricista para que solucionara el problema de un panel eléctrico con 42 disyuntores que suministraba energía a docenas de servidores y otras cargas no lineales. El técnico de TI del cliente observó que la parte frontal del disyuntor principal de 225 A, que se suponía que era blanca, era claramente amarilla. Al tocarla, se percató de que no solo había perdido color sino de que estaba extremadamente caliente.
Aunque no se habían producido cortes eléctricos, los recursos que se alimentaban a través de ese panel eran cruciales, por lo que el cliente no podía esperar a que se produjera una incidencia para ocuparse del problema.
Resolución de problemas con la alimentación encendida
Puesto que incluso un apagón intencionado hubiera sido muy difícil de programar, el proceso de solución de problemas se llevó a cabo con la alimentación encendida. En un estudio inicial del entorno, el electricista observó que el conductor neutro contaba con dos conductores de 4/0, que son conductores neutros sobredimensionados que suelen encontrarse en los tableros de paneles destinados a la transferencia de las cargas no lineales. Esto le indicó que el sistema se había diseñado correctamente.
Lo siguiente que hizo fue tomar su multímetro de aislamiento Fluke 1587 para medir la tensión de fase a fase y de fase a neutro en lado de línea del disyuntor principal de 225 A. Buscaba anomalías que pudieran conducirlo hasta el problema. Todas las mediciones resultaron dentro de los límites normales, ni demasiado altas ni demasiado bajas.
A continuación, observó la corriente que entraba en cada uno de los conductores de fase con la pinza amperimétrica Fluke 376 y detectó que la corriente se encontraba muy por debajo de los 225 A en las tres fases, entre los 108.9 A y los 130.3 A. Puesto que el panel alimentaba cargas no lineales, el siguiente paso lógico era observar los armónicos en la corriente. El electricista fijó el 376 al conductor neutro y se dio cuenta de que la corriente era bastante baja, de solo unos 38.9 A. Si los armónicos estuvieran dando problemas, la corriente en el neutro hubiera sido igual o más alta que una de las corrientes de las fases.
Armónicos descartados
¿Y las cargas que alimentaba el panel? ¿Quizás había armónicos de tensión ahí? Esta vez el electricista sacó su analizador de energía eléctrica Fluke 434 para comprobar los armónicos en las cargas procedentes del panel en cuestión. El contenido de armónicos concordaba con el tipo de cargas abastecidas. La tensión era buena y la corriente no era ni demasiado alta ni había ningún exceso de armónicos; una vez más, había llegado a un callejón sin salida.
Pero no había terminado. A continuación, registró la caída de tensión en toda la línea y de los conductores de fase del lado de carga del disyuntor principal (consulte la Tabla 1). Una conexión suelta o mala, o un problema interno con el circuito podían producir una gran caída de la tensión, un poco más de 100 milivoltios.
Medidas | |
---|---|
Fase A: 51.1 milivoltios | Fase A: 122.9 amperios |
Fase B: 41.6 milivoltioss | Fase B: 108.9 amperios |
Fase C: 137.1 milivoltios | Fase C: 130.3 amperios |
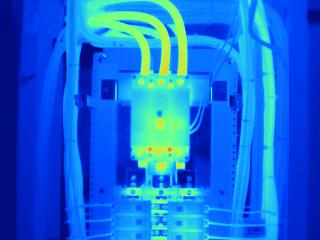
Las tensiones medidas en las fases "A" y "B" se encontraban dentro del intervalo correcto. Sin embargo, al obtener la medición de la fase "C" de 137 mV, fue bastante evidente de dónde provenía el calor. Puesto que el problema aún no justificaba cortar el suministro, el electricista sacó su cámara termográfica de Fluke, que sorprendentemente no indicaba que la fase C evidenciaba una temperatura más alta que las fases A y B (consulte la figura 1).
En la parte superior del disyuntor, el cable estaba muy caliente, pero se notaba cada vez más frío a medida que la cámara se alejaba del disyuntor. Esto indicaba que lo más probable era el problema se hallara en el terminal de cables o en el punto en que este se conectaba al disyuntor.
Antes de abandonar el sitio, el electricista conectó el registrador trifásico de calidad de energía Fluke 1735 a los conductores que alimentaban el disyuntor principal de 225 A y lo dejó midiendo la corriente durante una semana. Ello tampoco mostró anomalía alguna en la corriente. (Consulte la figura 2)
Puesto que durante el proceso de solución de problemas se había aislado la ubicación del problema pero no se había detectado la causa exacta, el cliente y los asesores eléctricos decidieron sustituir todas las conexiones del panel, incluidos todos los disyuntores, y tender conductores nuevos. "Tomamos esas medidas porque el costo del tiempo de inactividad y el nivel de importancia del sistema son tales que el cliente quiere que lo arreglemos. No quieren tener que organizar otro en el futuro cercano", explica el electricista.
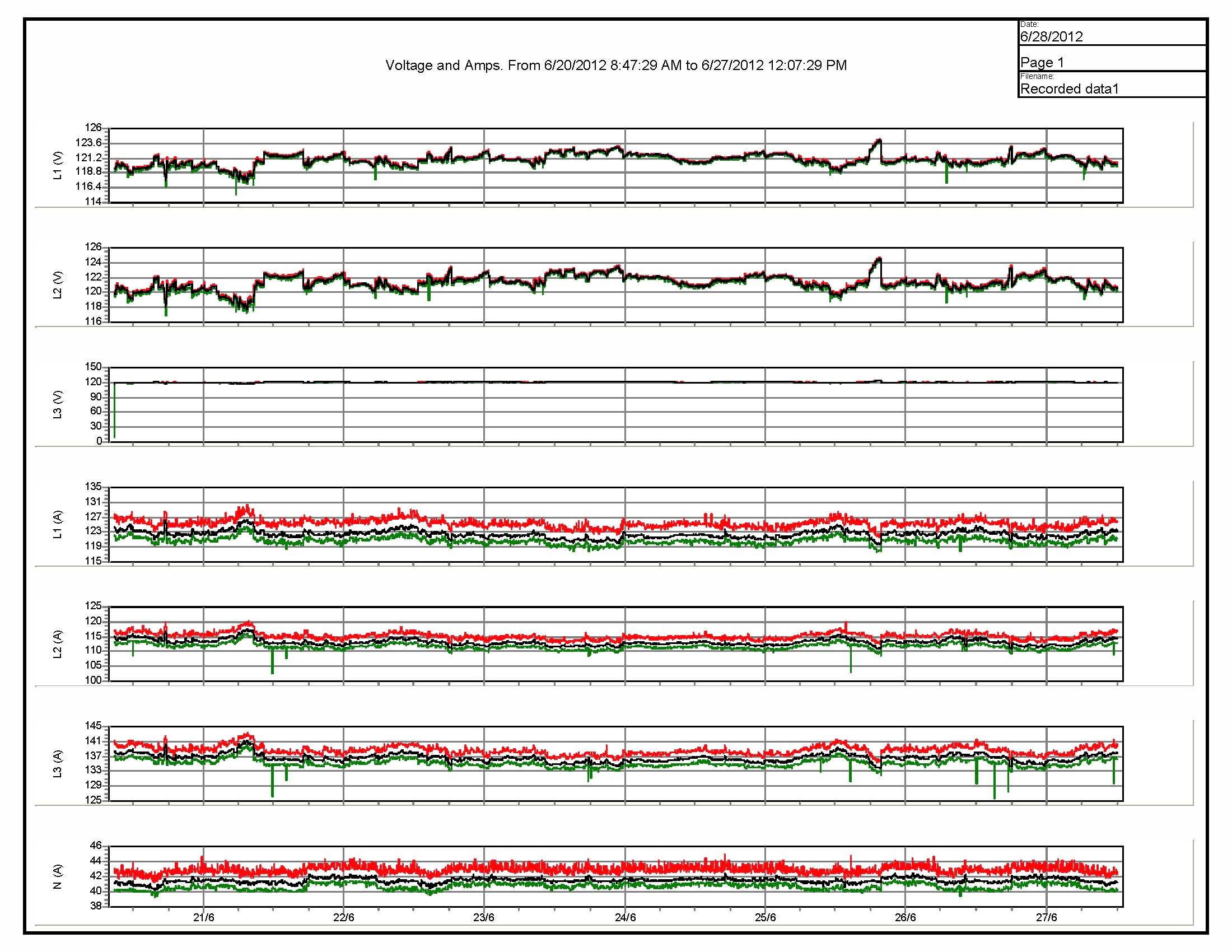
La solución
Más tarde, el cliente tuvo la oportunidad de desconectar el panel y remplazarlo. Aun así, los técnicos no quisieron correr riesgos. Antes de programarse la desconexión del panel, el interior del nuevo panel, ya completado con disyuntores principales y disyuntores de circuitos derivados, se envió a una empresa de pruebas independiente. La empresa de pruebas ajustó todas las conexiones internas según las especificaciones y realizó una prueba digital con el ohmímetro de baja resistencia para verificar la integridad de las conexiones internas.
Teniendo luz verde en relación con el estado del panel nuevo, los consultores pusieron manos a la obra. Desenergizaron el panel antiguo, desconectaron todos los conductores y quitaron las conexiones internas. Llegado este punto, efectuaron un examen visual y detectaron signos graves de sobrecalentamiento en el punto en el que el bus de la fase A se conecta con el disyuntor principal. [Consulte la figura 3]
A continuación, los electricistas instalaron nuevos buses de fase interiores, disyuntores de circuitos derivados, disyuntores principales y conductores de fase, y volvieron a conectar todos los conductores. Después de volver a conectar el panel al suministro, lo probaron para verificar que el panel nuevo funcionaba según lo especificado. Usando el multímetro de aislamiento Fluke 1587, tomaron una serie de mediciones de la tensión, incluidas la caída de tensión en toda la línea y del lado de carga del disyuntor principal, el cual indicaba las siguientes caídas de tensión:
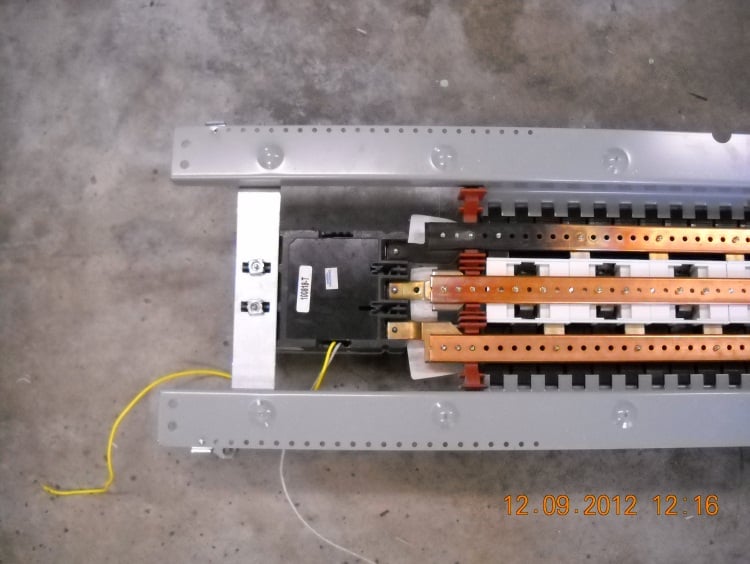
- Fase A: 50.4 milivoltios
- Fase B: 48.8 milivoltios
- Fase C: 41.4 milivoltios
Estas mediciones se encontraban dentro del intervalo normal, por lo que a continuación midieron la carga de amperios en los conductores de las fases con la pinza amperimétrica Fluke 376:
- Fase A: 144.1 amperios
- Fase B: 133.7 amperios
- Fase C: 132.6 amperios
Estas lecturas quedaban también dentro del requisito estipulado como aceptable de 80 %.
Finalmente, se procedió a escanear los conductores de fase del disyuntor principal sometido a cargas usando la cámara termográfica Fluke. El escáner mostraba cargas equilibradas en las tres fases.
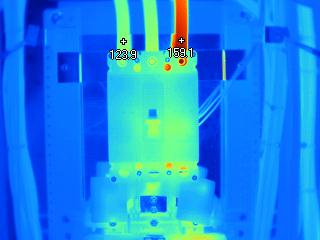
Hacia adelante
Aunque las mediciones mostraban que el nuevo panel funcionaba dentro de la estipulación de la carga de 80 %, los asesores esperaban que se acercara pronto al umbral de 80 %. A medida que la carga aumentaba, así lo hacía la temperatura, por lo que recomendaron al cliente hacer un seguimiento de la situación y plantearse la instalación de un nuevo alimentador de potencia en un futuro no muy lejano.