Qué elementos hay que buscar y cómo mejorar el funcionamiento ininterrumpido de los equipos
Los motores se utilizan en todo tipo de entornos industriales y cada vez son más complejos y técnicos, por lo que a veces, mantenerlos funcionando al máximo rendimiento supone todo un desafío. Es importante recordar que las causas de problemas de motores y variadores no se limitan a un solo ámbito de competencia. Tanto los problemas mecánicos como los eléctricos pueden causar un fallo del motor, por lo que disponer de los conocimientos adecuados puede marcar la diferencia entre tiempos de inactividad costosos y un mayor tiempo de funcionamiento ininterrumpido.
La ruptura del aislamiento del bobinado y el desgaste de los rodamientos son las dos causas más comunes de las averías del motor, si bien esas condiciones se producen por muchas razones diferentes. Este artículo muestra cómo detectar las 13 causas más comunes de avería en el aislamiento del bobinado y en los rodamientos con antelación.
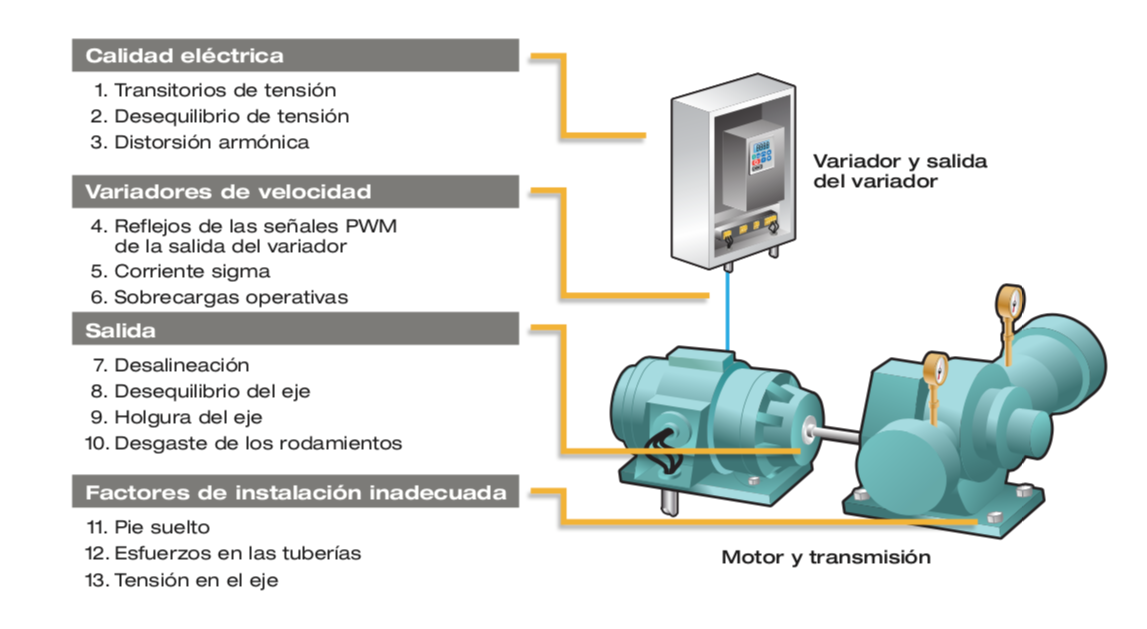
Calidad eléctrica
1
Transitorios de tensión
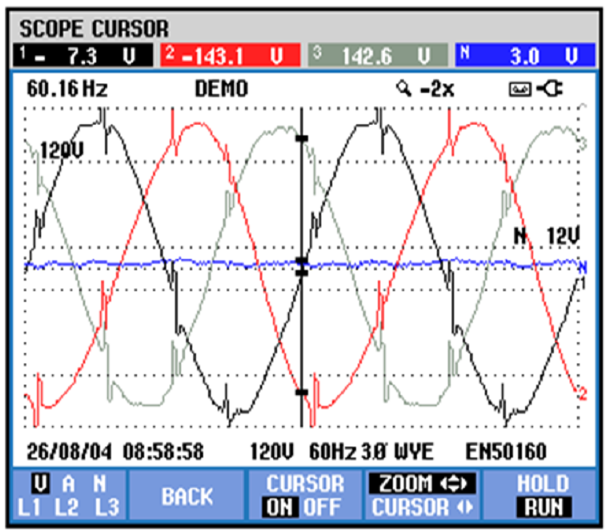
Los transitorios de tensión pueden proceder de varias fuentes ya sea dentro o fuera de la planta. El activar o desactivar cargas adyacentes, los bancos de condensadores de corrección de factor de potencia o incluso condiciones meteorológicas lejanas pueden generar transitorios de tensión en sistemas de distribución. Estos transitorios, que varían en la amplitud y frecuencia, pueden erosionar o causar el deterioro del aislamiento de los bobinados del motor. Encontrar la causa de estos transitorios puede resultar difícil debido al carácter aleatorio de estas incidencias y al hecho de que los síntomas pueden presentarse en diferentes formas. Por ejemplo, un transitorio puede aparecer en cables de control que no necesariamente causan daños en los equipos directamente, pero podrían perturbar las operaciones.
Consecuencias: una ruptura del aislamiento del bobinado tiene como consecuencia un fallo del motor prematuro y un tiempo de inactividad no planeado
Instrumento de medición y diagnóstico: analizador trifásico de calidad eléctrica Fluke 435-II
Importancia: alta
2
Desequilibrio de tensión
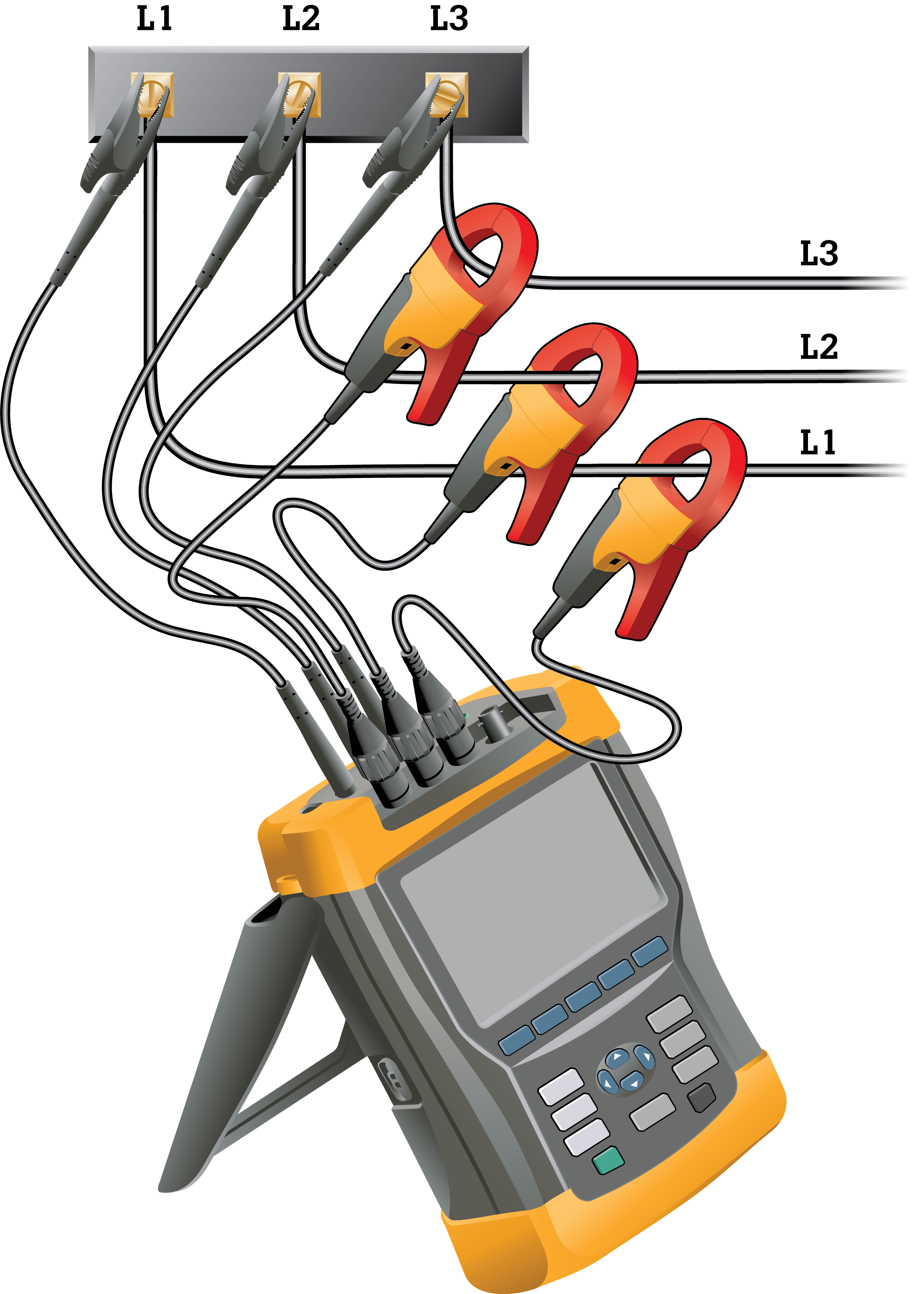
Los sistemas de distribución trifásicos a menudo alimentan cargas monofásicas. Un desequilibrio en la impedancia o distribución de la carga puede contribuir a un desequilibrio en las tres fases. Los posibles fallos pueden encontrarse en los cables que van al motor, las terminaciones en el motor o las propias bobinas. Este desequilibrio puede provocar esfuerzos en cada uno de los circuitos de fase en un sistema eléctrico trifásico. La norma básica es que las tres fases de tensión deben tener siempre la misma magnitud.
Consecuencias: el desequilibrio crea un flujo de corriente excesivo en una o más fases que a continuación aumenta las temperaturas de funcionamiento, lo que lleva a una ruptura del aislamiento
Instrumento de medición y diagnóstico: analizador trifásico de calidad eléctrica Fluke 435-II
Importancia: media
3
Distorsión armónica
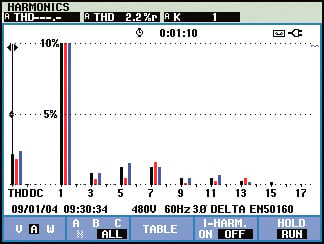
En pocas palabras: los armónicos son cualquier fuente adicional no deseada de tensiones CA o corrientes que suministran energía a las bobinas del motor. Esta energía adicional no se utiliza para hacer girar el eje del motor, sino que circula en las bobinas y en última instancia contribuye a pérdidas internas de energía. Estas pérdidas se disipan en forma de calor, el cual, con el tiempo, deteriorará la capacidad de aislamiento de los devanados. Un poco de distorsión armónica de la corriente es normal en cualquier parte de un sistema que alimente cargas electrónicas. Para empezar a investigar la distorsión armónica, utilice un analizador de calidad eléctrica para controlar los niveles de corriente. Igualmente, verifique las temperaturas en los transformadores para asegurarse de que no se sobrecargan. Cada armónico tiene un nivel aceptable de distorsión diferente, que se define mediante normativas como la IEEE 519-1992.
Consecuencias: reducción de la eficacia de los motores que se traduce en costes añadidos y aumento de las temperaturas de funcionamiento
Instrumento de medición y diagnóstico: analizador trifásico de calidad eléctrica Fluke 435-II
Importancia: media
Variadores de velocidad
4
Reflejos de las señales PWM de la salida del variador
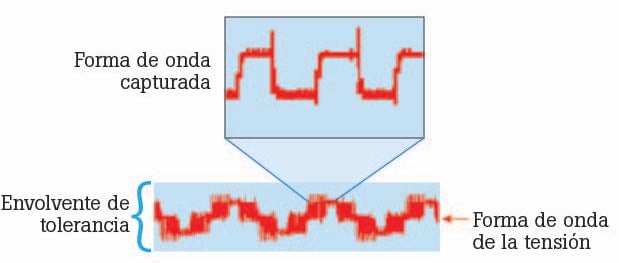
Los variadores de velocidad utilizan una técnica de modulación del ancho de pulso (PWM) para controlar la tensión de salida y la frecuencia que alimenta un motor. Los reflejos se generan cuando hay una discrepancia en la impedancia entre la fuente y la carga. Las discrepancias de impedancia pueden producirse como resultado de una instalación inadecuada, una selección inadecuada de componentes o una degradación de los equipos a lo largo del tiempo. En el circuito de una unidad de motor, la cresta del reflejo puede ser tan alta como el nivel de tensión del bus de CC.
Consecuencias: una ruptura en el aislamiento del bobinado tiene como resultado tiempos de inactividad no planeados
Instrumento de medición y diagnóstico: osciloscopio portátil de muestreo rápido de 4 canales ScopeMeter® de Fluke.
Importancia: alta
5
Corriente sigma
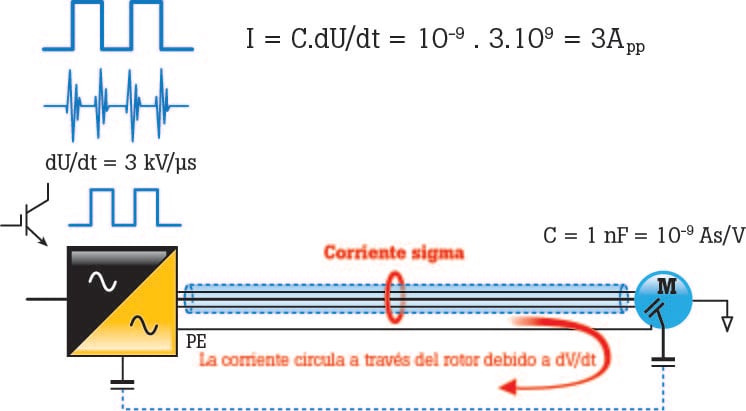
Las corrientes sigma en esencia son corrientes de fuga que circulan en un sistema. Las corrientes sigma se crean como resultado de la frecuencia de la señal, el nivel de tensión, la capacitancia y la inductancia de los conductores. Estas corrientes que circulan pueden atravesar sistemas de protección a tierra, causando desconexiones o en algunos casos un exceso de calor en el bobinado. La corriente sigma puede encontrarse en el cableado del motor y es la suma de la corriente de las tres fases en un momento dado en el tiempo. En una situación perfecta, la suma de las tres corrientes sería cero. En otras palabras, la corriente de retorno de la unidad sería igual a la corriente a la unidad. También se puede entender la corriente sigma como señales asimétricas en varios conductores que pueden acoplar capacitivamente corrientes en el conductor de puesta a tierra.
Consecuencias: el circuito se dispara de forma misteriosa debido al flujo de corriente de protección a tierra
Instrumento de medición y diagnóstico: osciloscopio portátil aislado de 4 canales con pinza de corriente (Fluke i400 S o similar) de ancho de banda amplio (10 kHz) ScopeMeter 190-204 de Fluke.
Importancia: baja
6
Sobrecargas operativas

La sobrecarga del motor se produce cuando un motor se encuentra bajo una carga excesiva. Los síntomas principales que acompañan a la sobrecarga del motor son un exceso de consumo de corriente, par insuficiente y sobrecalentamiento. Un calor excesivo del motor es una de las causas principales del fallo del motor. En caso de sobrecarga del motor, es posible que los componentes individuales como los rodamientos, los bobinados y otros componentes funcionen bien; pero el motor seguirá funcionando a una temperatura elevada. Por este motivo, tiene sentido comenzar la investigación comprobando si el motor está sobrecargado. Debido a que el 30 % de averías del motor están causadas por sobrecarga, es importante comprender cómo medir e identificar la sobrecarga del motor.
Consecuencias: desgaste prematuro del motor y sus componentes mecánicos, que producen una avería permanente
Instrumento de medición y diagnóstico: multímetro digital Fluke 289
Importancia: alta
Salida
7
Desalineación
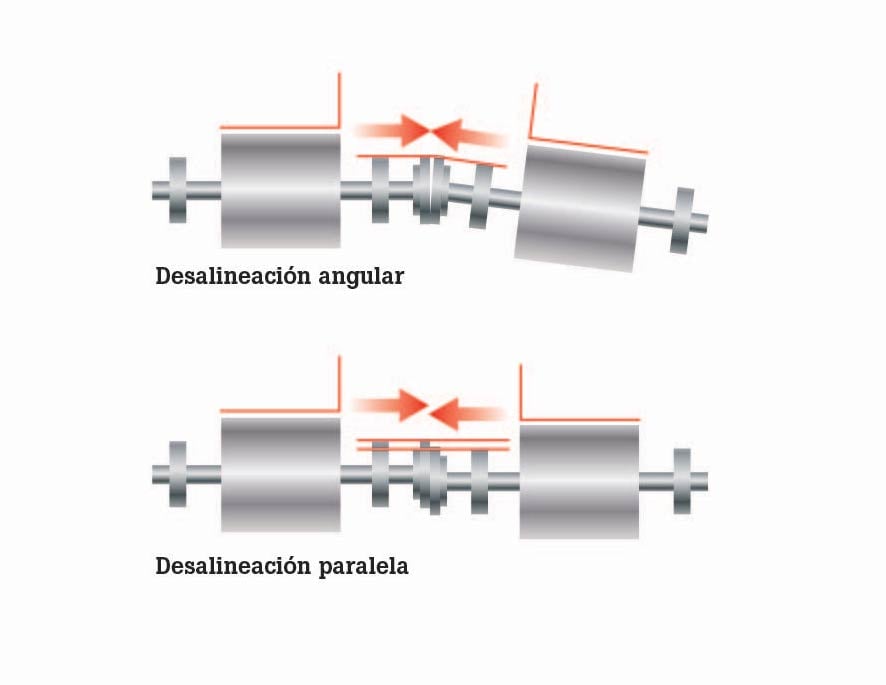
Se produce una desalineación cuando el eje de la unidad del motor no está alineado correctamente con la carga, o el componente que acopla el motor a la carga está desalineado. Muchos profesionales creen que un acoplamiento flexible elimina y compensa la desalineación, pero un acoplamiento flexible solo protege de la desalineación al acoplamiento. Incluso con un acoplamiento flexible, un eje desalineado transmitirá fuerzas cíclicas dañinas por el eje y dentro del motor, teniendo como consecuencia un desgaste excesivo del motor y aumentando la carga mecánica aparente. Además, la desalineación puede transmitir vibraciones tanto en la carga como en el eje del motor. Hay varios tipos de desalineación:
- Desalineación angular: las líneas centrales del eje se intersectan pero no son paralelas
- Desalineación paralela: las líneas centrales del eje son paralelas pero no concéntricas
- Desalineación compuesta: una combinación de desalineación paralela y angular. (Nota: Casi toda la desalineación es desalineación compuesta, pero los profesionales hablan de desalineación como si hubiera dos tipos separados porque es más fácil corregir la desalineación al abordar las componentes angulares y paralelas por separado).
Consecuencias: un desgaste prematuro en los componentes de la unidad mecánica que tiene como consecuencia averías prematuras
Instrumento de medición y diagnóstico: herramienta láser de alineación de ejes Fluke 830
Importancia: alta
8
Desequilibrio del eje
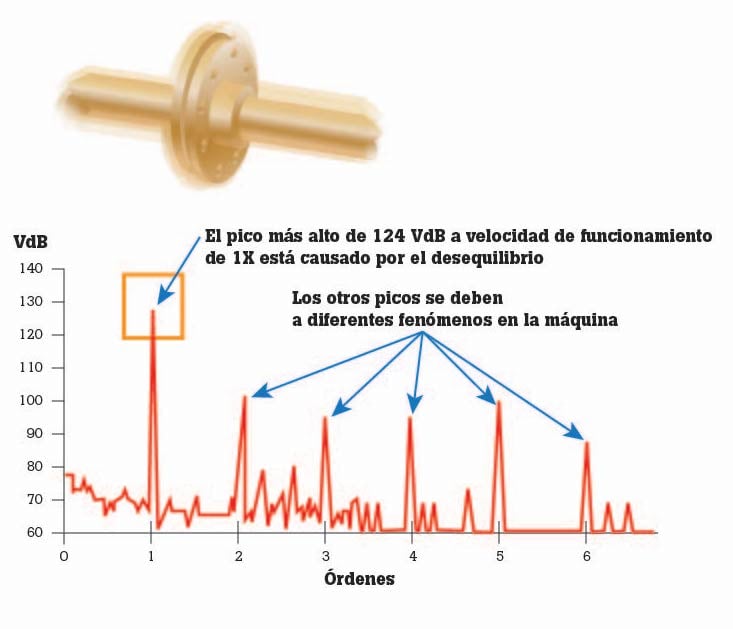
El desequilibrio es una condición de una pieza giratoria cuando el centro de la masa no se encuentra en el eje de rotación. En otras palabras, hay un “punto pesado” en alguna parte del rotor. Aunque nunca se puede eliminar por completo el desequilibrio del motor, se puede identificar cuando está fuera del rango normal y actuar para rectificar el problema. El desequilibrio puede deberse a numerosos factores, entre los que se incluyen:
- Acumulación de suciedad
- Falta de contrapesos
- Variaciones de fabricación
- Una masa desigual en los bobinados del motor y otros factores relacionados con el desgaste.
Un analizador o comprobador de vibraciones puede ayudarle a determinar si una máquina rotatoria está equilibrada.
Consecuencias: un desgaste prematuro en los componentes de la unidad mecánica que tiene como consecuencia averías prematuras
Instrumento de medición y diagnóstico: analizador de vibraciones Fluke 810
Importancia: alta
9
Holgura del eje
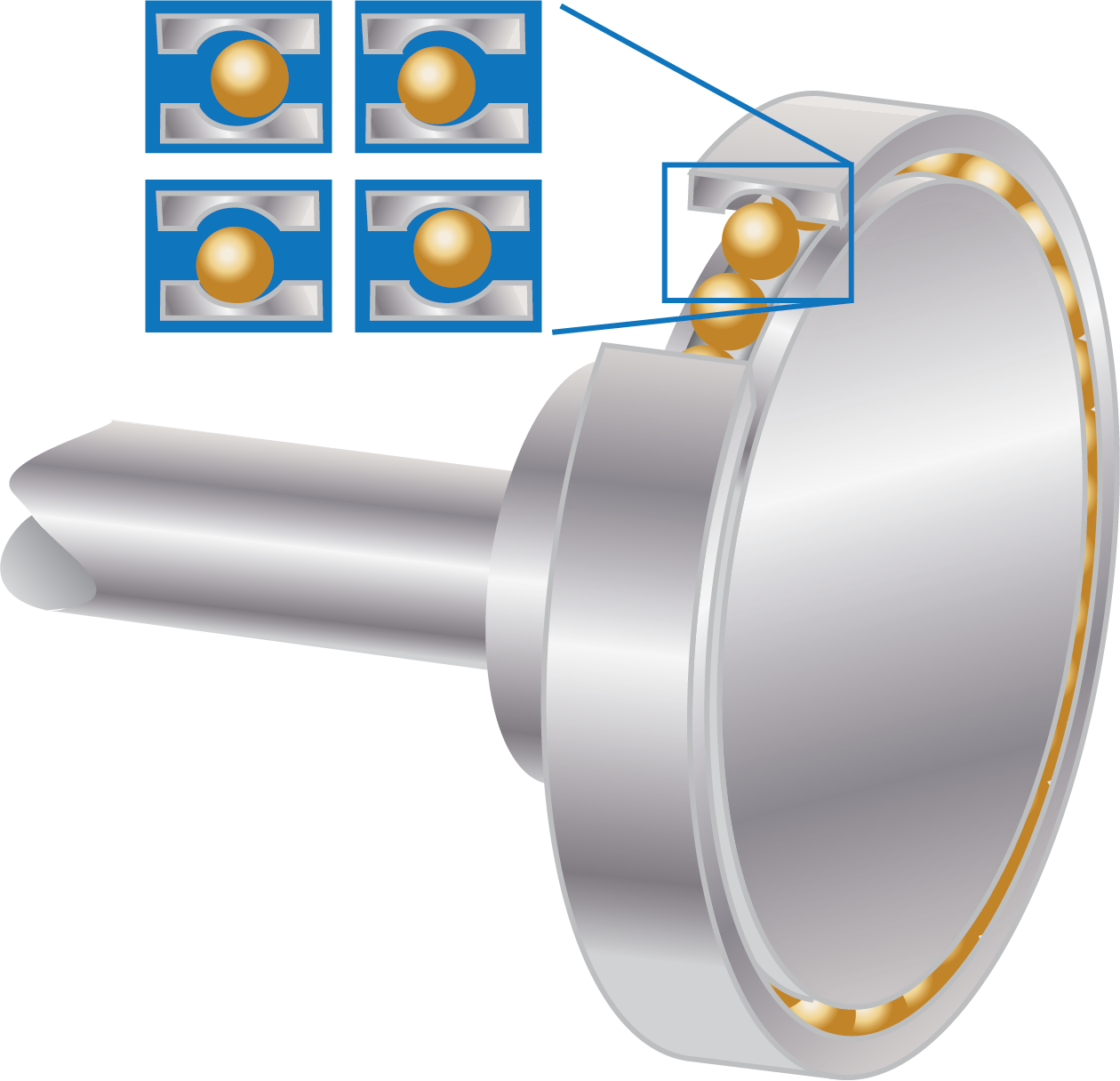
La holgura se produce cuando hay demasiado espacio entre las piezas. La holgura puede ocurrir en varios lugares:
- La holgura rotativa se produce debido a una separación excesiva entre los elementos rotatorios y fijos de la máquina, como sucede en un rodamiento.
- La holgura no rotativa se produce entre dos piezas normalmente fijas, como una pata y la base, o la carcasa de un rodamiento y una máquina.
Como con todas las demás fuentes de vibración, es importante saber cómo identificar la holgura y resolver la incidencia para minimizar los costes. Un analizador o comprobador de vibraciones puede determinar si una máquina rotatoria sufre de holgura.
Consecuencias: desgaste acelerado en componentes rotatorios que se traduce en un fallo mecánico
Instrumento de medición y diagnóstico: analizador de vibraciones Fluke 810
Importancia: alta
10
Desgaste de los rodamientos
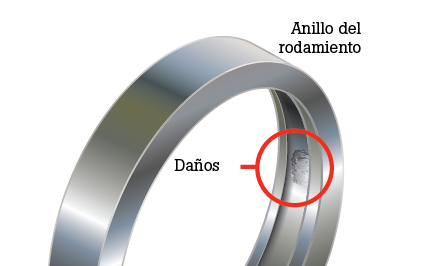
Un rodamiento averiado tiene un mayor arrastre, emite más calor y tiene una eficiencia menor debido a un problema mecánico, de lubricación o de desgaste. Un fallo en un rodamiento puede deberse a varios factores:
- Una carga más pesada que para la que se diseñó
- Lubricación inadecuada o incorrecta
- Sellado ineficaz del rodamiento
- Desalineación del eje
- Ajuste incorrecto
- Desgaste normal
- Tensiones inducidas en el eje
Una vez que comienza la avería en el rodamiento, también se crea un efecto cascada que acelera el fallo del motor. El 13 % de las averías de los motores se deben a fallos en los rodamientos, y más del 60 % de los fallos mecánicos en una instalación se deben al desgaste de los rodamientos, por lo que es importante aprender a detectar y solucionar estos posibles problemas.
Consecuencias: desgaste acelerado en componentes rotatorios, lo que se traduce en averías en los rodamientos
Instrumento de medición y diagnóstico: analizador de vibraciones Fluke 810
Importancia: alta
Factores de instalación inadecuada
11
Pie suelto
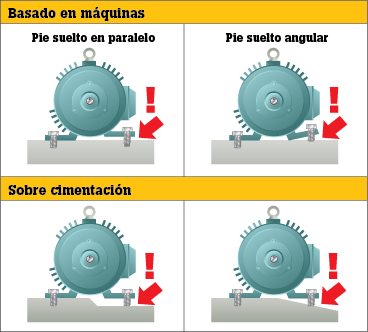
El pie suelto hace referencia a una condición en la cual los pies de montaje de un motor o componente accionado no son uniformes, o la superficie sobre la que descansan los pies de montaje no es uniforme. Esta condición puede crear una situación frustrante en la que apretar los tornillos de fijación en los pies en realidad produce nuevas tensiones y desalineación. Un pie suelto a menudo se manifiesta entre dos tornillos de fijación situados en diagonal, de la misma forma que una silla o mesa coja tiende a balancearse en una dirección diagonal. Hay dos tipos de pie suelto:
- Pie suelto en paralelo: el pie suelto en paralelo se produce cuando uno de los pies de montaje está más alto que los otros tres
- Pie suelto angular: el pie suelto angular se produce cuando uno de los pies de montaje no está paralelo o "normal" respecto a la superficie de montaje.
En ambos casos, el pie suelto puede deberse a una irregularidad en los pies de montaje de la máquina o en la base de montaje sobre la que descansan los pies. En ambos casos es necesario descubrir cualquier situación de pie blando y corregirla antes de que se pueda lograr una alineación adecuada de los ejes. Una herramienta de alineación láser de calidad suele determinar si hay un problema de pie suelto en una máquina rotativa determinada.
Consecuencias: desalineación de los componentes del sistema mecánico
Instrumento de medición y diagnóstico: herramienta de alineación láser de ejes Fluke 830
Importancia: media
12
Esfuerzos en los tubos
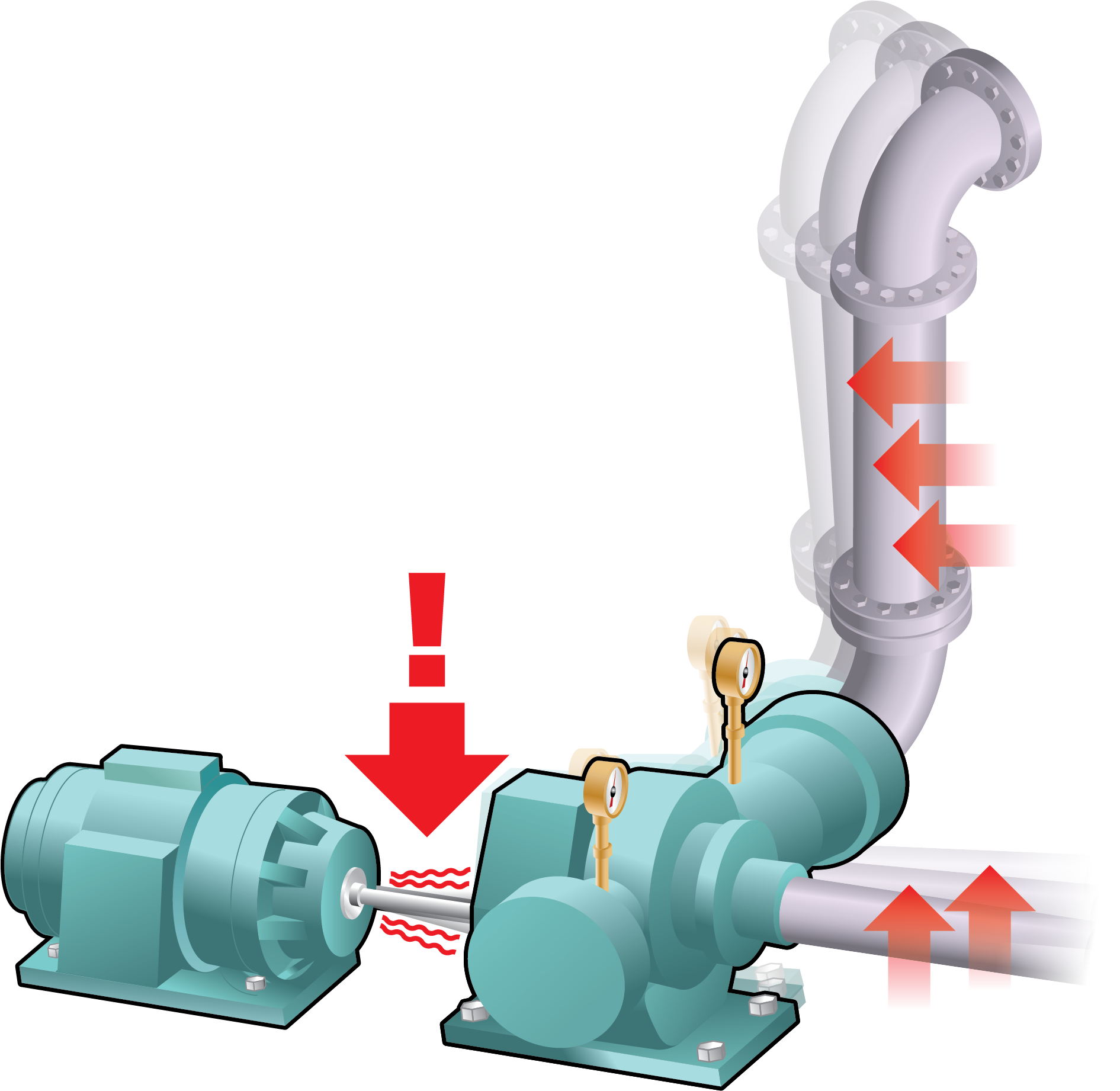
Los esfuerzos en las tuberías pueden estar provocados por esfuerzos, tensiones y fuerzas que actúan en el resto de los equipos e infra- estructura y se pueden transferir al motor y su unidad, provocando así una situación de desalineación. El ejemplo más común de esto se ve en combinaciones sencillas de motor/bomba, donde algo aplica fuerza a las tuberías como:
- Un cambio en la base
- Una válvula u otro componente recién instalado
- Un objeto que golpea, dobla o solo presiona una tubería
- Soportes para tuberías o accesorios para montaje en pared rotos o ausentes
Estas fuerzas pueden aplicar tensiones angulares o descompensación sobre la bomba, que a su vez provoca que el eje del motor/bomba quede desalineado. Por este motivo es importante comprobar la alineación de la máquina no solo cuando se instala; la precisión de la alineación es una condición temporal que puede cambiar con el tiempo.
Consecuencias: desalineación del eje y consiguientes esfuerzos en los componentes rotatorios, que se traducen en fallos prematuros.
Instrumento de medición y diagnóstico: herramienta láser de alineación de ejes Fluke 830
Importancia: baja
13
Tensión del eje
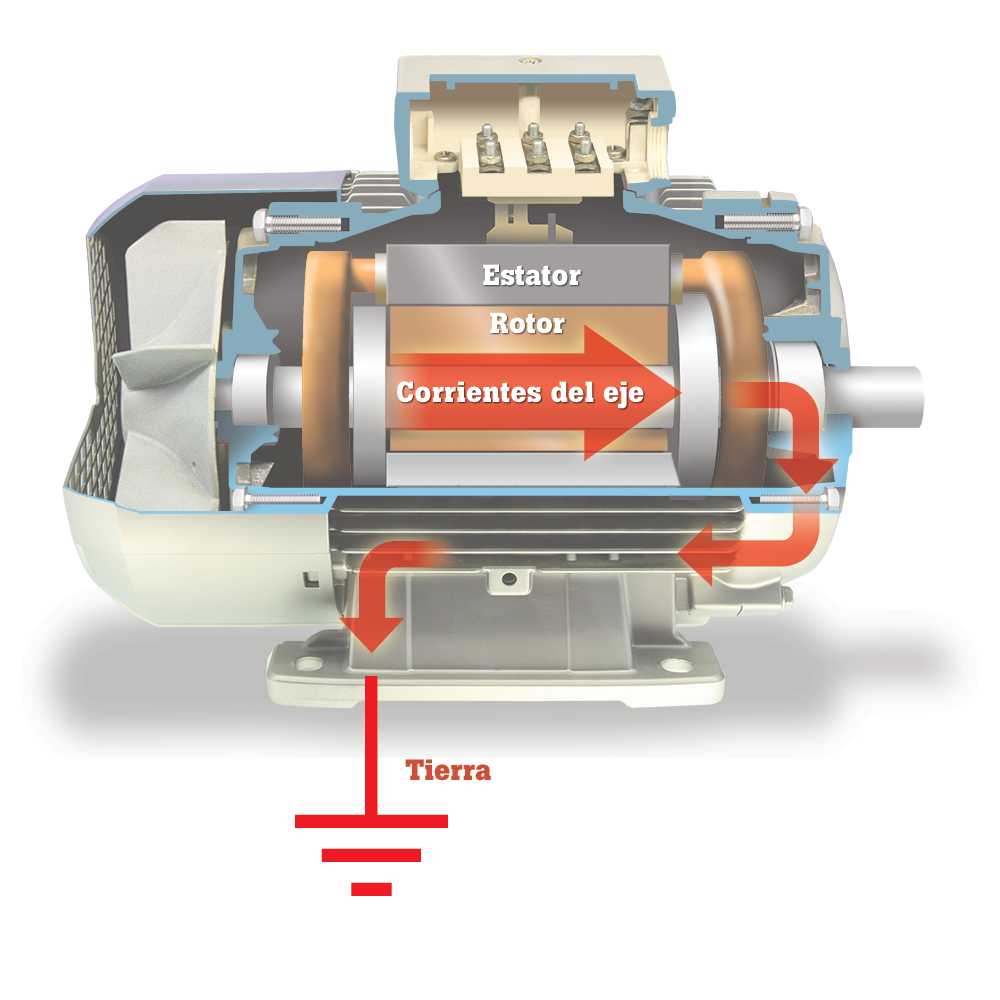
Cuando las tensiones en el eje del motor exceden la capacidad de aislamiento de la grasa del rodamiento, se producen descargas de corriente hacia el rodamiento exterior, lo que produce picaduras y marcas en los anillos de los rodamientos. Los primeros signos de este problema son el ruido y el sobrecalentamiento cuando los rodamientos comienzan a perder su forma original y algunos fragmentos de metal se mezclan con la grasa y aumentan la fricción del rodamiento. Esto puede provocar la destrucción de los rodamientos con apenas unos meses de funcionamiento del motor. Un fallo en el rodamiento es un problema caro tanto desde el punto de vista de reparación del motor como del tiempo de inactividad provocado, por lo que ayudar a prevenir esto al medir la tensión del eje y la corriente del rodamiento es un importante paso de diagnóstico. La tensión en el eje solo está presente mientras el motor recibe energía y gira. Un accesorio con sonda de escobilla de carbono permite medir la tensión del eje mientras el motor gira.
Consecuencias: El arco a través de las superficies del rodamiento crea picaduras y marcas que como consecuencia provocan un exceso de vibraciones y finalmente una avería en el rodamiento
Instrumento de medición y diagnóstico: Osciloscopio portátil aislado de 4 canales Fluke 190-204 con sonda de escobilla de carbono para medir la tensión en el eje AEGIS
Importancia: alta
Cuatro estrategias para el éxito
Los sistemas de control del motor se utilizan en procesos críticos a lo largo de las plantas de fabricación. Los fallos en los equipos pueden conllevar grandes pérdidas monetarias tanto por la posible sustitución del motor o piezas como por el tiempo de inactividad de los equipos del sistema que alimenta dicho motor. Dotar a los ingenieros y técnicos de mantenimiento de los conocimientos adecuados, priorizar la carga de trabajo y gestionar el mantenimiento preventivo para controlar los equipos y solucionar problemas intermitentes y escurridizos puede, en algunos casos, evitar fallos debido a los esfuerzos normales del funcionamiento del sistema y reducir los costes generales de los tiempos de inactividad.
Hay cuatro estrategias fundamentales que puede llevar a cabo para restaurar o evitar fallos prematuros en motores y componentes rotativos:
- Documentar las condiciones de funcionamiento, las especificaciones de la máquina y los rangos de tolerancia de rendimiento.
- Capturar y registrar las mediciones fundamentales en el momento de la instalación, antes y después del mantenimiento y de forma rutinaria.
- Crear un archivo de referencia de las mediciones para facilitar el análisis de tendencias e identificar cambios en las condiciones de estado.
- Marcar las mediciones individuales para establecer una tendencia de referencia. Cualquier cambio en líneas de tendencia de más del + /- 10 % al 20 % (o cualquier otro porcentaje determinado basado en el rendimiento o la importancia de su sistema) debería investigarse hasta encontrar la causa raíz para entender por qué se produce ese problema.