Machine health monitoring baselining and trending with Fluke Connect® Assets allows you to organize data in one place, associate it with equipment, and compare baselines with trend information.
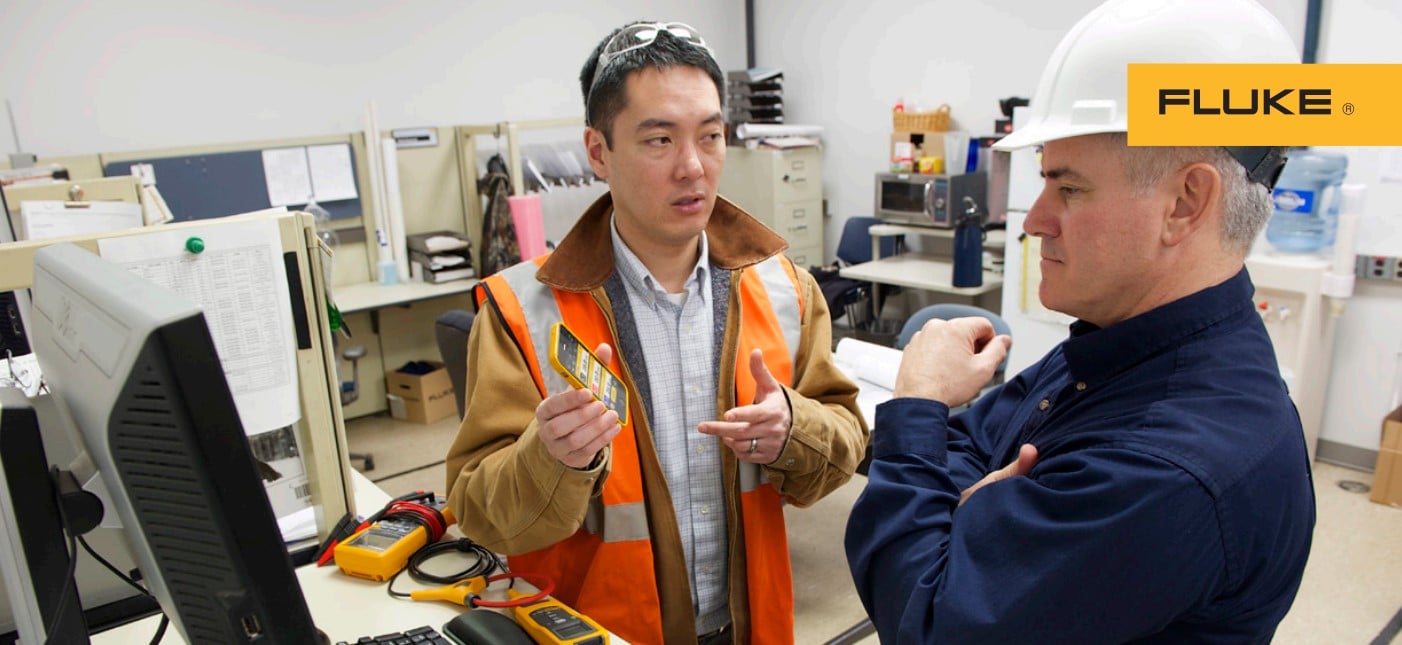
This kind of strategy uses wirelessly connected handheld test instruments that send measurements directly to smartphones and store the information in the cloud. Managers, engineers, and technicians can then employ software to organize the data into a machine health monitoring matrix. Along with associated analytical tools, a matrix helps organize preventive and predictive maintenance. This kind of condition-based program can also aid troubleshooting and root cause determination.
“To be able to group those technologies together [vibration, thermographic, and electrical meters] is kind of a utopian vision of condition monitoring,” says Eric K, a reliability engineer with a Fortune 500 food company. “So often, I find myself looking, where do I grab this data? Who has this piece of information? And to have it all in one shot makes it a lot easier to make business decisions based on that information.”
The following control applications benefit from baseline and trending analyses:
- Variable Frequency Drives (VFD’s) and associated rotating equipment (motors, pumps, etc.)
- Control loops
- Programmable automated controllers (PACs) and programmable logic controllers (PLCs)
- Pneumatic components
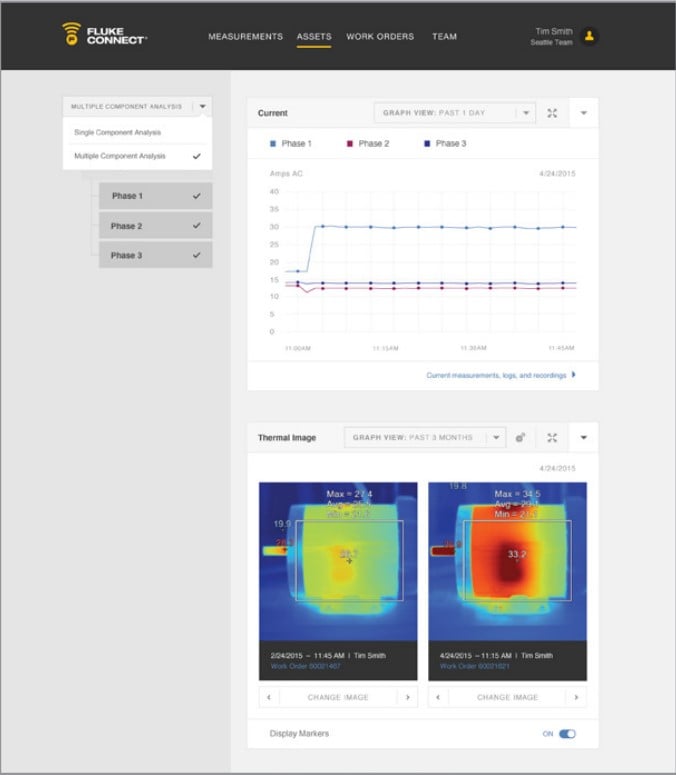
Fluke Connect® Assets software provides the ability to organize all data in one place, associate with equipment and compare baselines with trend data.
Organize data all in one place
The sheer volume of data produced in today’s plants can pose a challenge, and on-premise storage solutions can risk data loss from corrupted hard drives, fire, or other disasters. Plus, it’s often a struggle to organize all the data and securely provide access to the people who need it. As time marches on, software evolves, and so does data storage.
Even with a computerized maintenance management system (CMMS) in place, it’s difficult to analyze data collected by the typical range of technologies–voltage, temperature, current and vibration. It’s a time-consuming task to assemble a holistic view of failure patterns for all plant assets.
For example, failing to isolate the source of an intermittent voltage spike on a PLC input at a critical line, may cause troubleshooting teams to overcompensate by recommending the replacement of the whole device, while only one element was at fault. Yet that still doesn’t solve the underlying problem.
Consider how technologically advanced and wirelessly connected tools such as thermal imagers, power quality analyzers, digital multimeters, handheld oscilloscopes, resistance testers, and more would enable systematic data collection along the line.
The goals:
1. Create baselines of critical equipment during normal operations
2. Capture the same measurements over time so when failure occurs, the data can be used to determine failure mode patterns.
How to create a baseline with connected test instruments
A team is assigned to create and catalog test points for each individual piece of equipment in web-based software–painted targets on motors and near belts where infrared images are taken, voltage inputs and outputs on the PLC, motor couplings, and power to the compressor. Those test points are associated with their respective equipment in the software.Technicians are then equipped with test instruments–vibration meters, infrared cameras, voltage or current modules, handheld oscilloscopes – even power quality analyzers—as well as software that can organize, save, and correlate data about multiple test points and many of equipment.
They start when the line is running at normal operating conditions, technicians take baseline measurements at each test point with the connected test instruments and move on down the line. The initial test samples could be averaged across several identical pieces of equipment operated in the same application to create a standard deviation (one sigma).
With a smartphone loaded with the app, the technician saves data to the specific test point and machine, then automatically uploads data from the test instruments to the cloud. (In some cases, engineers may choose to log measurements, with a voltage module or power quality analyzer, for example, over longer periods of time.) Those measurements are immediately sharable anywhere via the app or web-based desktop software.
How to continue to capture data in one place
Each test point is associated with equipment for identification online and all data from individual equipment is stored in secure data servers in the cloud for easy retrieval.In a month (or week, or three months) the technician takes the same measurements at the same point at the PLC and the other pieces of equipment in the route. For the best results, the measurements are made under consistent, repeatable operating conditions, ideally at the same time of day, in order to create apples-to-apples comparisons.
When there is a problem on the line, record measurements not only from the device under test but also other machinery that might be impacting that device.
In the software, use analytical tools to compare the measurements and asset performance over time and use that information to make more informed predictive decisions.
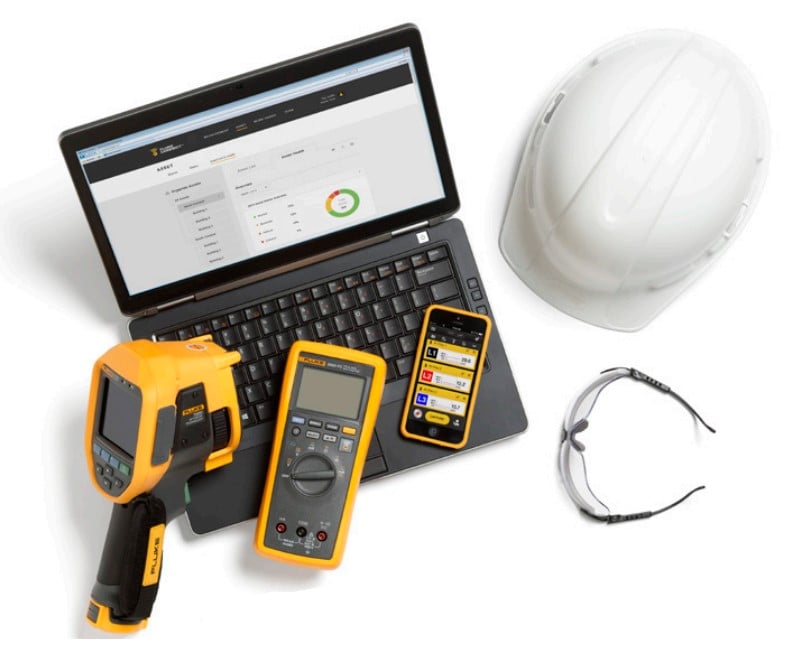
Machine health comparison and analysis
Compare the measurement trends, identifying any abnormal conditions like overcurrent or events that correlate to a system’s stress condition.- Check for a change in state from the baseline data
- Check status changes
- Check exceeded threshold settings
Answer questions such as: Were the voltage waveforms on the PLC outputs malformed? Did infrared inspection test point show temperature spikes? Did the level of vibration increase on the motor powering the conveyor?
Creating a matrix of timestamped data from multiple test instruments over time facilitates driving to the root cause of failures in a system. Rather than viewing one measurement on one machine, you can correlate data and analyze multiple types of measurements from individual machines as well as compare with other critical equipment in the same system.
Benefit of wireless test tools and cloud-based software for baselining and trending
- Aggregate all data without the errors prone with manual data collection or the cost of labor associated with collecting and organizing the data
- Gather historic performance data, and establish valuable performance baselines
- View all the data on one screen, not trying to manage multiple pieces of software
- Correlate multiple data points, such as voltage, current and thermal images, allows you to quickly spot irregularities
- Get multiple data points and trend graphs to compare each piece of equipment, which helps preventive maintenance planning and meets uptime goals
- Access immediate updates on asset status from the field because techs can use their mobile phones to change the status of suspect equipment from normal to at-risk
- No matter what shift works on a problem every technician will with consistency collect system characteristics and supporting information
- Has this happened before?
- Has anyone looked into this previously?
- 5 ways condition monitoring can improve your maintenance program
- How to streamline maintenance, reduce costs, and improve asset performance with Fluke Mobile
- Easy-to-install Fluke sensors help you track conditional change
- Fluke Connect Condition Monitoring Dashboard provides insight at a glance