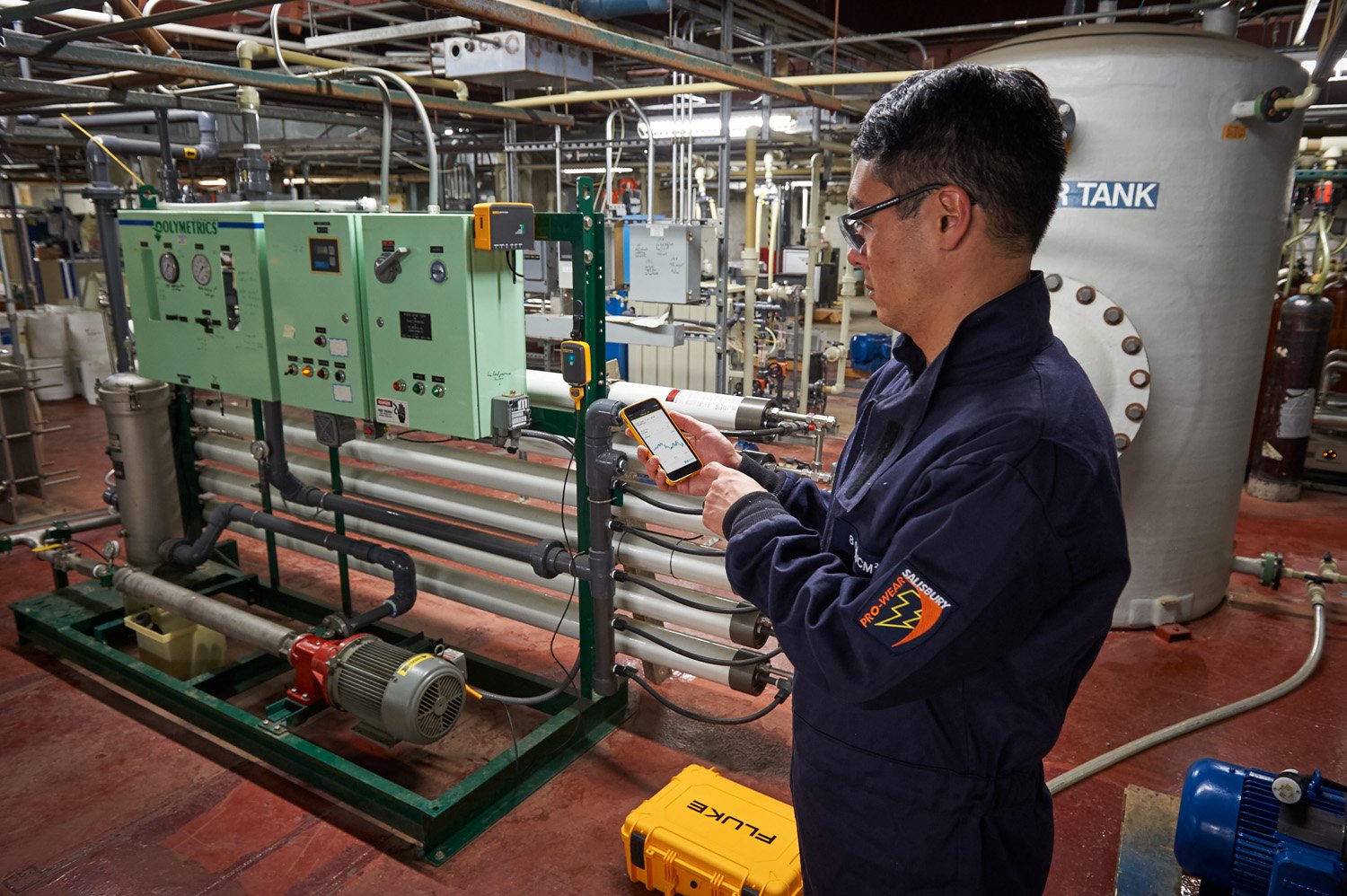
There are many reasons why organizations may not have plans to implement industrial internet of things (IIoT) devices into their maintenance program. However, it’s becoming more and more evident that teams need to start planning for a Connected Reliability future. Efficiencies that benefit workers on the shop floor will inevitably improve the business.
1. Connecting people to data and systems
Connected Reliability isn’t about replacing maintenance and reliability (M&R) professionals but augmenting them to better meet the needs of organizations. Providing workers with the data they need and access to facility systems is vital for a Maintenance 4.0 program.
“The flexibility of current and emerging technology leaves no room for barriers,” said Kevin Clark, VP, Fluke Accelix. “M&R personnel must be able to collect asset and system measurements however they want, be that with a handheld meter, a wireless sensor, a supervisory control and data acquisition (SCADA) system, or any other condition/ process data.”
Information that is sequestered or inaccessible tells teams nothing. When teams have the right data at hand and have access to operational systems in a unified view, they are better able to make data-driven, results-oriented decisions. Connecting people, data, and systems is the cornerstone of Connected Reliability and empowers people to make the right choices at the right time.
2. Automate data collection for safety
Removing interaction between people and hazardous places—called “Hazard Controls” or “Engineering Controls”—is a common way to improve safety in facilities. Safety and health hazards can be from routine, non-routine, or emergency tasks, including routine measurement taking or emergency repairs due to failure.
According to Clark, M&R teams haven’t benefited from the massive amounts of route-based data they collect. Day-to-day maintenance activities “remain manual and often reactive”, particularly with Tier 2 or lower category assets. Fans near ceilings, motors in areas with excessive heat or noise, pumps under grating, and other inaccessible assets are ripe for installation of remote monitoring sensors to reduce manual routes. Keeping people out of harm’s way not only improves efficiency but increases workplace morale1, too.
3. Improve asset life
Repairing equipment on a schedule wastes resources. Lubricants or components may not have reached the end of their lifecycle by the time scheduled maintenance comes around. Conditionbased maintenance with remote monitoring allows teams to extend the amount of time between repairs, improving asset uptime and availability.
Condition-based maintenance works hand-inhand with continuous improvement programs, such as Lean, Sigma-6, 5S, and more. Continuous improvement programs seek to reduce costs, streamline processes, and do more with existing programs. Failure can introduce foreign bodies into lubricants, cause premature wear on components, or even produce unsafe hazards for people. When assets aren’t getting to the point of critical failure, they’re less likely to cause serious safety concerns. Not only will condition-based maintenance improve asset life-cycle and availability, it will also improve worker morale as well.
4. Keep workforces on-the-go
Connected Reliability also means keeping workers as mobile as possible while still providing them with the vital information they need. After IIoTenhanced devices upload data to the cloud, connected reliability software allows access to data and systems via smart devices.
Integrating multiple sources of data enables reliability teams to make faster and better maintenance decisions, said Gregory Perry (CMRP/ CRL), senior consultant at Accelix. Ultimately, he continues, the EAM/CMMS system should integrate with existing databases to provide actionable, event-driven insights.
Of course, staying mobile is only half the battle. Receiving information from assets with a mobile workforce is another important aspect of a Connected Reliability program.
Many software systems that automatically aggregate measurements from sensors can also send alarms. When measurements exceed user-set thresholds, an alarm is generated by software and sent to maintenance teams’ mobile devices. Whether teams are on the shop floor or at home, they’ll have instant notification of asset problems. This helps teams keep assets from ever becoming critical in the first place, improving uptime and workplace safety
5. Future-proof maintenance programs
The Industrial Revolution 4.0 is coming. Industrial internet of things (IIoT) technologies are already being used in factories across the globe. An SAP study2 found that organizations who implemented IIoT-enhanced systems were more likely to be industry leaders and “world-class” organizations. More importantly, they were more likely to have larger profits than similar companies that did not implement IIoT devices.
Maintenance isn’t just something that has to be done, it can be a business value engine. Maintenance efforts are not just financial burdens, they are financial drivers. Proper maintenance keeps companies in regulatory compliance, keeps them producing effectively, keeps their workers happier, and improves the organization’s bottom line. Ensure that M&R teams are better able to meet the demands of future facilities by enhancing maintenance programs with Connected Reliability, today.
Do this... | Skip that... |
---|---|
Automatically aggregate asset measurements to a cloud-based repository | Send personnel out on routes for manual measurements |
Get the full life out of resources by knowing the right time to do repairs | Waste resources by completing premature maintenance |
Look at a smart device to view real-time or historical asset data | Run back and forth from the office to assets to get data for individual tasks |
Connecting your plant to the future
The future isn’t just about connecting asset data to a storage system, it’s about improving the lives and workflows of maintenance engineers and technicians—those on the shop floors and remote locations—providing them with the information they need to succeed. When workers succeed, the organizations employing them succeed. And for the organization, success usually equates improved bottom lines.
To speak with a Fluke representitive about Connected Reliability, please head to www.Fluke.com.
- Occupational Safety and Health Administration (OSHA). (2016, October). Recommended Practices for Safety and Health Programs. Retrieved January 20, 2019, from https://www.osha.gov/shpguidelines/ docs/8524_OSHA_Construction_Guidelines_R4.pdf
- “Catch up with IoT Leaders,” SAP, https://www.sap. com/cmp/dg/crm-xm17-gtm-1sc-pgm161/index. html?url_id=ctabutton-Leverage_IoT_Now_TR-blogDigitalist-2018_IoT_MPI-Report1.