Here we look closely at the first segment in a typical three-phase motor and drive system: from the mains supply at the drive input to the drive itself, concentrating on input measurements. This application note maps common problems to the measurements used to diagnose them . We show you what tools to use for a given situation and how to apply them to a problem, to enable you to troubleshoot more quickly and accurately.
Here are the different blocks in a typical three-phase motor drive system (Figure 1):
- First, the drive input is the ac power entering the drive from the mains.
- Second, the drive and its output, where the ac to dc converter, the dc filter, and the dc to ac inverter provide the three phase power to the motor.
- Finally, the motor and drive train itself.
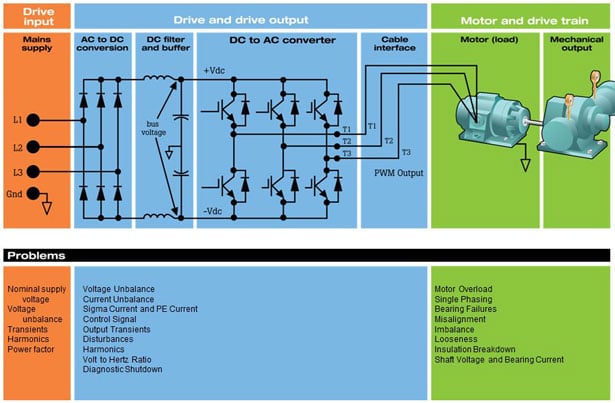
Note that this article is about troubleshooting three-phase motors and drives. The content here does not translate well to single-phase motors.
Introduction to input measurements
When troubleshooting a system as complex as a motor and drive, sometimes it's hard to know where to start. By checking the supply voltage, current, and frequency first, you can rule out problems that might affect the motor drive or breaker circuits. This can save time and lead to faster problem resolution. In addition, by identifying over or under voltage conditions, you can avoid nuisance tripping of drive fault circuits and eventual damage to the motor drive itself.
You can make input measurements at a number of locations. Figure 2 shows different input points going from the main service entrance to subpanel or disconnect switch to the power input at the drive. Potentially each of these measurement points could provide different results, because the measurement points may be affected by other loads on the circuits.
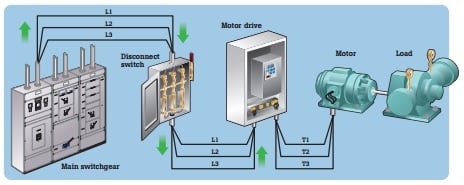
There are three reasons to make input measurements:
- To establish that there is enough capacity to power the motor and drive system.
- To establish that the power is of suitable quality.
- To make sure that drive load is not adversely affecting power quality in the system overall. For example, to verify that the motor drive is not generating harmonics or creating dips that could disrupt other operations.
You should start your diagnostic efforts at the input side of the motor drive because the voltage, current, and frequency of the electricity that powers a variable speed motor system can affect its operation in the short term and its longevity and reliability over the long term.
What are the nominal voltage, current, and frequency?
Nominal supply voltage, current, and frequency are the three primary measurements for the voltage supplied to the motor drive under normal operating conditions. In general, "nominal" means "named." So, the nominal voltage is the named (or rated) voltage of a piece of electrical equipment; in other words, the voltage at which the device is designated to operate. The actual values can vary from the nominal values; the nominal values provide a basis for comparison with the measurements you make (Figure 3).
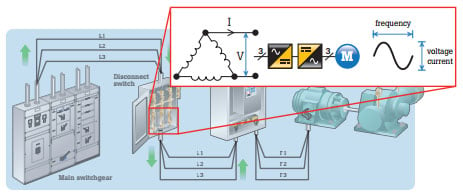
Starting at the input of the motor drive, measure voltage, current, and frequency, then compare your measurements with nominal values. (Nominal values are expected values - for example, 480 volts for a 480-volt line, the current listed on motor's nameplate, and a frequency of 50 or 60 Hz, depending on your locale).
You can make these measurements with a digital multimeter and a current clamp, just as you would on a single-phase circuit, but making the measurements with a three-phase power quality analyzer makes the job easier (Figure 4). Measuring three phases at the same time can also reveal interactions between the phases that can't be seen with single-phase measurements. Be sure to connect the power quality analyzer correctly for the circuit type (wye or delta).
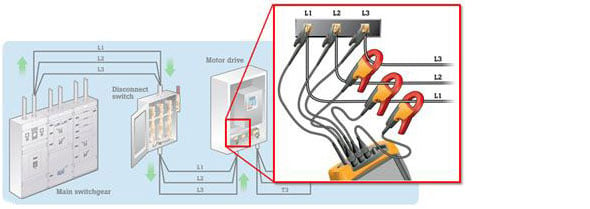
The amount of deviation from nominal that is considered acceptable varies by locale, but as a rule:
- Voltage should be within plus or minus 10 percent of nominal.
- Current should never exceed the nameplate rating of the load.
- Frequency should be within 0.5 Hz of nominal.
Evaluating the measurements
- If the voltage is consistently too high, consult with the electric utility (Figure 5).
- If the voltage is too low, check whether the local circuit is overloaded. Do this by comparing your current measurements with the circuit breaker rating. If the measured current is within the range of the breaker, check the size of the cable that supplies the drive to make sure it conforms to NEC requirements.
- If your voltage measurements are within an acceptable range and the circuit appears to be correctly configured but there are still problems such as the motor drive resetting or circuit breakers opening, there may be intermittent power supply problems. To detect problems that are happening over a longer time period than your initial measurements, use your power quality analyzer or a power quality recorder to log any power quality disturbances on the circuit over a longer measurement period or until the next fault occurs.
- If all voltage, current, and frequency measurements are within an acceptable range, check for voltage and current unbalance.
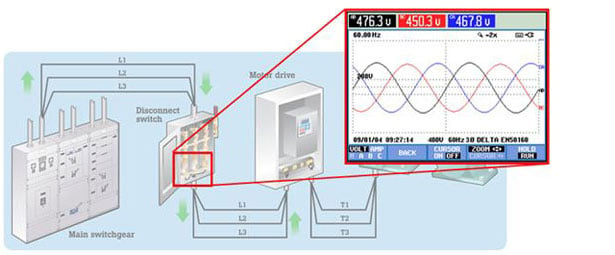
Voltage and Current Unbalance
Ideally, the voltages that you measure in each phase of a three-phase system should be the same. This is also true for current measurements. Because voltage or current unbalance can cause downtime or damage to a motor drive, learning how to interpret these measurements is important (Figure 6).
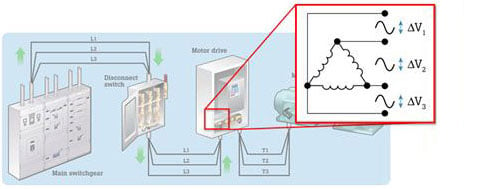
Expressing the amount of voltage or current unbalance as a percentage enables you to describe the size of the problem simply and quickly with a single number. To get the percentage of unbalance, divide the biggest deviation measured on one phase by the average of three phases and multiply by 100. For example, if you measured 480 v, 485 v, and 490 v, the average voltage is 485 volts and the biggest deviation is 5 volts. Five volts divided by 485 volts is .01, which gives a 1percent voltage unbalance when multiplied by 100.
(480v + 485v + 490v) / 3 = 485 average voltage
(5 v maximum deviation from average * 100) / (485 v average) = 1 percent voltage unbalance
As little as a two percent voltage unbalance at the input of a motor drive can cause voltage notching and excessive current flow in one or more phases going to the motor. Voltage unbalance can also cause tripping of the motor drive's current overload fault protection.
Current unbalance is a measure of difference in current drawn by a motor on each leg of a three-phase system. Correcting current unbalance helps prevent overheating and the deterioration of motor-winding insulation. The draw on each leg should be equal or close to equal. One cause of current unbalance is voltage unbalance, which can cause current unbalance far out of proportion to the to the voltage unbalance itself. When current unbalance occurs in the absence of voltage unbalance, look for another cause of the current unbalance, e.g., faulty insulation or a phase shorted to ground. Current unbalance is calculated the same way as voltage unbalance. It is 100 times the maximum current variation from average divided by the average current of the three phases. So, if the measured current is 30 amps, 35 amps and 30 amps, the average is 31.7 amps, and the current unbalance is
[(35 - 31.7) x 100] ÷ 31.7 = 10.4%
Current unbalance for three-phase motors should not exceed 10 percent.
High neutral current can indicate unbalance. Unbalance current will flow in neutral conductors in 3-phase wye systems.
Harmonics
The 50 or 60 Hz frequency of the voltage supplied by the utility is called the fundamental frequency. In a perfect world, the fundamental frequency is the only one present. Unfortunately, some electrical loads (such as computers, controls, drives, and energy-saving lighting systems) can cause other frequencies to appear in your measurements. These other frequencies, which are multiples of the fundamental (so 120 Hz, 180 Hz, and so on for a 60 Hz fundamental frequency), are called harmonics.
The power at the service entrance of your facility will usually be low in harmonic frequencies (unless they are leaking on to the power lines from a nearby facility). Inside your facility, however, harmonics may be high if there are a lot of harmonic-generating devices in the facility.
Although motor drives can be affected by harmonics, they are often the source of harmonics that affect other devices in the facility. If you detect significant levels of harmonics in your drive measurements, you may need to consider adding filtering to block those harmonics.
Transients
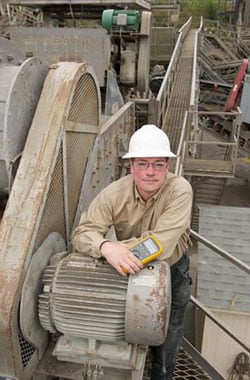
Transients are, as their name suggests, brief events (less than one half cycle, so less than 1/120th of a second in a 60 Hz system) on the ac line. Many people associate transients with external events, such as lightning surges, but transients can also originate within a system or building. Detecting, troubleshooting, and addressing transients is important because transients can damage motors and other parts of the motor circuitry.
Diagnostic Benefits
By checking the supply voltage, current, and frequency first, you can rule out issues that might affect the motor drive or breaker circuits. This can save you time and lead to a faster problem resolution. In addition, by identifying over or under voltage conditions, you can avoid nuisance tripping of drive fault circuits, and eventual damage to the motor drive itself.