Trying to decide on an insulation resistance tester? Not sure exactly which model, what features, or what output test voltage you need?
There are six things to consider when deciding on the best insulation resistance tester for your needs, including:
- What equipment needs to be tested?
- What are the voltage requirements?
- Where are the tests going to take place?
- What questions will an insulation resistance tester help me answer?
- What is the experience level of the technician performing the tests?
- What role does safety play in selecting a new tool?
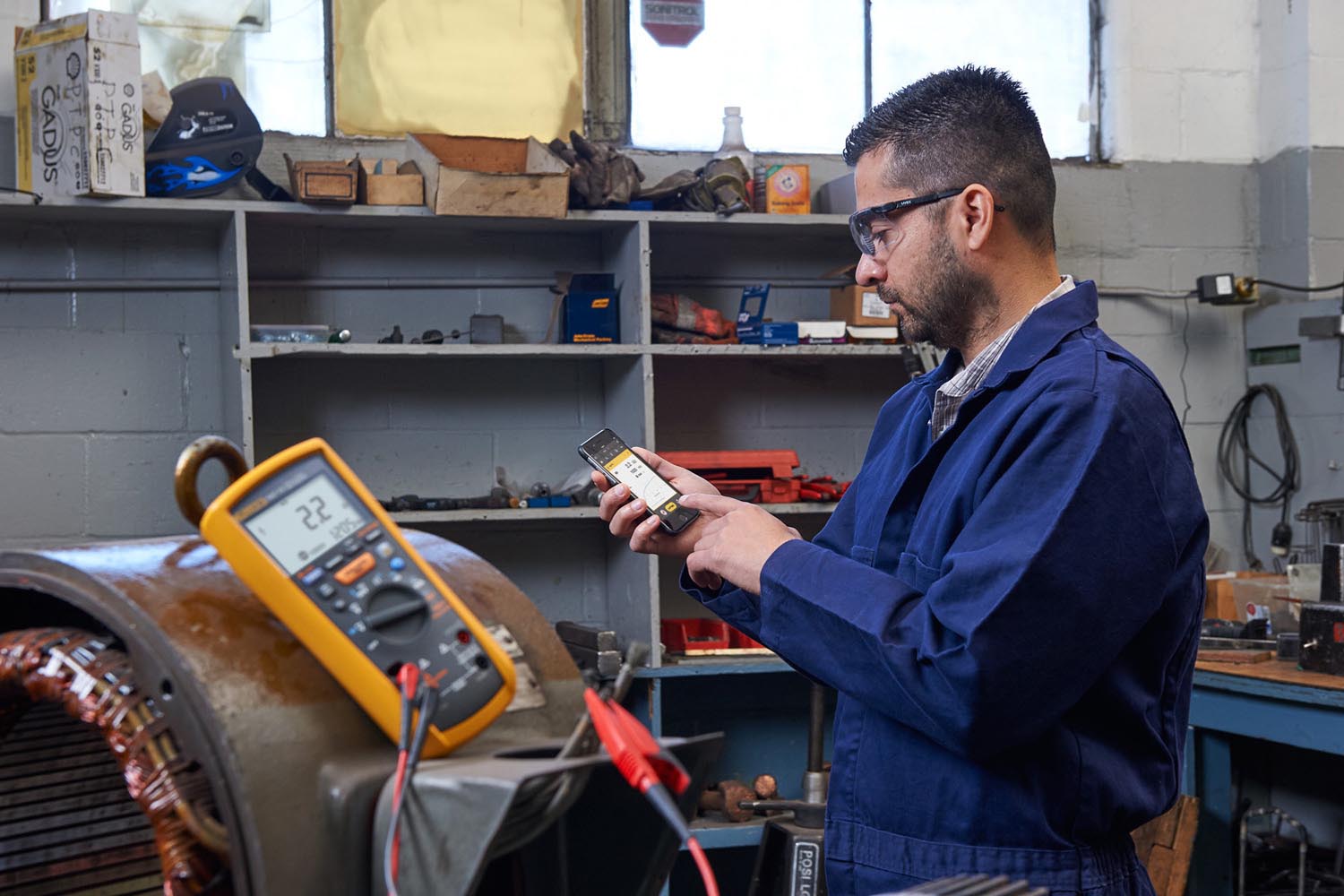
The insulation tester you choose should match your testing requirements. Many handheld insulation testers can supply test voltages up to 1000 volts.
A look at the products
Before examining these six issues, let’s look at the relevant products.
Insulation tester features | Two-in-one tools: insulation test plus digital multimeter | Stand-alone tools: dedicated insulation testers | ||||
---|---|---|---|---|---|---|
Fluke 1587 FC Insulation Multimeter | Fluke 1577 Insulation Multimeter | Fluke 1503 Insulation Resistance Meter | Fluke 1507 Insulation Resistance Tester | Fluke 1550C FC 5 kV Digital Insulation Tester | Fluke 1555 FC 10 kV Insulation Tester | |
Test voltages | 50 V 100 V 250 V 500 V 1,000 V | 500 V 1,000 V | 500 V 1,000 V | 50 V 100 V 500 V 1,000 V | 250 V 5,000 V | 250 V 10,000 V |
Insulation resistance range | 0.01 MΩ to 2 GΩ | 0.01 MΩ to 600 GΩ | 0.01 MΩ to 2,000 GΩ | 0.01 MΩ to 10 GΩ | 200 k to 1 TΩ | 200 k to 2 TΩ |
PI/DAR | x | x | x | |||
Auto discharge | x | x | x | x | x | x |
Timed ramp test (breakdown) | x | x | ||||
Pass/fail comparison | x | x | x | |||
Est. # of IRT tests | 1,000 | 1,000 | 2,000 | 2,000 | Various | Various |
Voltage >30 V warning | x | x | x | x | x | x |
Memory | x | x | ||||
Remote test probe | x | x | x | x | ||
Lo ohms/earth-bond continuity | 200 mA source (10 mΩ resolution) | 200 mA source (10 mΩ resolution) | ||||
Display | Digital LCD | Digital LCD | Digital LCD | Digital LCD | Digital LCD/analog | Digital LCD/analog |
Hold/lock | x | x | x | x | x | x |
Multimeter Features | ||||||
1577: ac/dc volts, current, resistance, continuity beeper, backlight | ||||||
1587 only: temperature (contact), lo-pass filter, capacitance, diode test, frequency, MIN/MAX |
What equipment needs testing?
First, make a list of the equipment that you expect to require insulation resistance testing. Write down the equipment's nominal voltage rating (found on the nameplate of the equipment) and the approximate number of insulation resistance tests that you plan to perform annually. The nominal voltage will help determine what test voltage is needed from the tester. The annual number of insulation resistance tests estimated may be surprising. When more tests need to be conducted, the overall quality, durability, and convenience features of the test instrument become more important.
What are the voltage requirements?
The output test voltage applied to equipment should be based on the manufacturer's recommended DC insulation resistance test voltage. If test voltage is not specified, use industry best practice data. (See the table for recommendations of the International Electrical Testing Association.) Make sure you choose an insulation resistance tester that will supply the needed output test voltage. Not all insulation resistance testers are the same: some will supply only up to 1,000 V DC, while others may supply 5,000 V DC test voltage or more.
Where are the tests going to take place?
Considering the testing environment and other possible uses for the insulation resistance tester will help in selecting additional features. For example, the ability to use one instrument for insulation resistance tests and as a typical digital multimeter can add convenience. Because all circuits and equipment must be verified as electrically de-energized before an insulation resistance tester is connected to the equipment, it is often less convenient to carry both a digital multimeter for voltage testing and an insulation resistance tester to various locations.
Nominal voltage rating of equipment | Minimum insulation resistance DC test voltage | Recommended minimum insulation resistance in megohms |
---|---|---|
250 | 500 | 25 |
600 | 1,000 | 100 |
1,000 | 1,000 | 100 |
5,000 | 2,500 | 1,000 |
15,000 | 2,500 | 5,000 |
Recommended test voltages and minimum insulation values. The International Electrical Testing Association (NETA) provides representative test and minimum insulation values for various voltage ratings of equipment for use when manufacturer's data is not available.
When thinking about the environment for testing, ask yourself these questions:
- Will the insulation resistance tester be used for troubleshooting, preventive maintenance, or both?
- Where will the test instrument be used — only in a shop environment or in an industrial plant?
Some insulation resistance testers can be relatively large and not very portable, while others can be carried easily.
HVAC service technicians not only test for failed insulation, but they also commonly test for open fuses and failed capacitors. Technicians who often perform voltage checks, capacitor checks, temperature measurements, and insulation resistance tests may prefer a test tool that combines all these functions into one instrument.
Consider also the features you need based on the type of insulation resistance test to be performed. In fact, this one question may come to mind: If you need only one simple insulation test, why purchase an insulation resistance tester at all, since a standard multimeter already has the ability to read resistance? To help answer that question and better understand some of the features that may be required in an insulation resistance tester, it is necessary to understand what happens in the process of measuring insulation resistance and what the test is designed to accomplish.
What you learn from an insulation resistance test
Insulation resistance testing puts a qualitative value on the condition of conductor insulation and the internal insulation of different pieces of electrical equipment. As an insulation resistance test begins, apply a DC voltage to the conductor or equipment under test. Some current flows out of the test equipment into the conductor and begins to charge the insulation. This current is called capacitive charging current and can be observed on the meter face.
As the charging current first begins to build, the resistance reading on the meter face will indicate a low value. Think of this as electrons beginning to flow into and become stored in the insulation itself. The more current that flows out of the test set, the lower the megohm reading. The insulation becomes charged quickly and the meter indication will begin to settle out at a higher megohm value, provided the quality of the insulation is good.
The next current that flows is the absorption — or polarization — current. The amount of absorption current is dependent upon the contamination of the insulation. For example, if moisture is present in the insulation, absorption current will be high, indicating a lower resistance value. However, it is important to realize this absorption current takes longer to build than the capacitive charging current. Therefore, an insulation tester operated for too short a period will observe only the capacitive charging current and not begin to show the presence of contaminants in the insulation.
Finally, the current that leaks through deteriorated insulation and into the non-current carrying metal components is the leakage current. This current is most often considered in an insulation resistance test. However, for more accurate troubleshooting and maintenance, the absorption or polarization current must also be considered. Some insulation resistance testers can be programmed to perform the tests needed to consider all currents.
Will you measure polarization current?
Since the polarization current takes longer to build, the insulation resistance tester must run for a longer period. The industry standard for this test is ten minutes. To help determine the contamination and overall condition of insulation, take a reading on the insulation resistance tester at one minute and another reading at ten minutes. The ten-minute reading is divided by the one-minute reading to provide the polarization index. As part of a routine maintenance program, you should record both spot reading test values and the polarization index values. Always compare the most recent readings to previous readings. The polarization index should never be less than 1.0.
Will you measure leakage current?
While all insulation resistance testers will indicate leakage current and provide the information to help estimate contamination of the insulation, for industrial environments you should consider those testers that automatically obtain this data. You obtain leakage current by applying the test voltage to the component under test, then taking a resistance reading after one minute. This is often called the spot reading test. The spot reading test allows capacitive charging currents to stabilize and is the industry standard to determine leakage current through insulation. Minimum insulation resistance values in megohms should be based on the spot reading test.
What is your experience level?
Any test instrument is only as good as the knowledge and experience level of the person using the equipment and interpreting its readings. When selecting an insulation resistance tester, consider the expertise of the individuals who will be performing the insulation resistance tests. Obviously, simplicity and limited functions should be considered if application needs and experience levels are minimal. However, training on insulation resistance testing need not be extensive. Manufacturers' manuals and basic texts are available to serve the purpose. For inexperienced personnel, consider on-the-job training for proper and safe use of insulation resistance testers. Make sure the insulation resistance tester purchased will meet the application needs for output test voltage and other functions. Then, provide training for those who will be performing the tests.
What role does safety play in testing and troubleshooting?
Safety is paramount when it comes to testing and troubleshooting. Because the insulation resistance tester produces significant DC voltages, it can never be connected to an energized circuit. Also, the output of the tester can destroy electronic circuits. Never connect an insulation resistance tester to electronic power supplies, PLCs, VSDs, UPS systems, battery chargers, or other solid-state devices. Some insulation resistance testers have a built-in type of warning system that will let technicians know when voltage is present on a circuit.
Like all test tools, insulation resistance testers should be rated for their application, suitable for the environment in which they will operate, and tested by a nationally recognized testing laboratory. If it will also be used as a multimeter, the insulation resistance tester should be category rated. Test leads should be durable, rated, and tested.
Insulation can hold a significant voltage charge for a period after the insulation resistance test is complete. Most testers will automatically discharge the insulation after the test is complete, but some will not. This is an important point to consider when selecting an insulation resistance tester. Some testers will indicate voltage levels as well as insulation resistance values. On such testers it is possible to watch the voltage level decay to zero after the test output voltage is shut off. Some manufacturers recommend the insulation resistance tester remain connected to the circuit or component under test after the test is complete for up to four times as long as the test was conducted to ensure safe discharge. Most technicians will ground the circuit under test after the test is complete to verify the insulation is discharged. Research the tester's self-discharge feature carefully when selecting an insulation resistance tester.
The next step in selecting your insulation resistance tester
Selecting the correct insulation resistance tester provides for troubleshooting efficiency and accurate, complete maintenance records over time. Make a list of equipment that requires insulation resistance testing and determine the test voltages needed for that equipment and insulation. Identify the testing environment and think carefully about any special features that are needed. Examine the safety features of the test equipment and review the experience level of the technicians who will be using it. An insulation resistance tester is a valuable tool for HVAC technicians — but only if it's the right insulation resistance tester for the job.