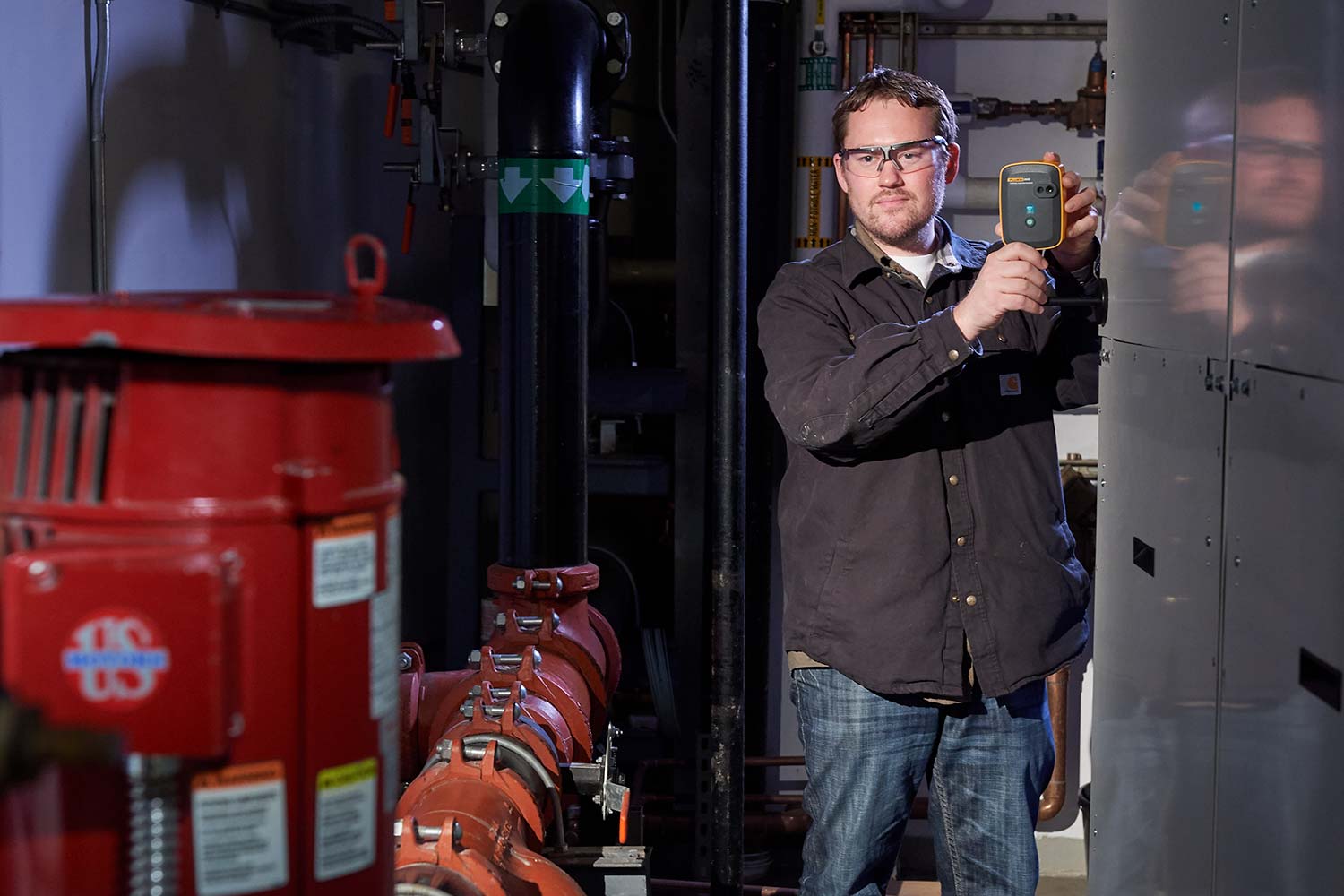
Limited resources can make monitoring all vital plant equipment difficult, if not impossible. That’s where condition monitoring with wireless sensors comes in.
Monitoring all plant equipment can be difficult, especially when working with shrinking budgets and limited personnel. Quite often, critical equipment in commercial and industrial settings may display symptoms that indicate a future failure, but those indications go undetected. That’s because, while many critical pieces of equipment may have fixed monitoring systems, many other important assets, such as pumps, heat exchangers, compressors, motors and blowers, may not be monitored and can require an extra level of monitoring to identify intermittent events. For this less critical, but still essential equipment, it isn’t always possible to catch events before they result in failure or downtime even when operating under “run-to-failure” maintenance. This is where condition monitoring can help.
Modern condition monitoring systems are changing the way the industrial world performs maintenance activities with portable, wireless sensors and connectivity gateways. This technology enables teams to continuously monitor assets so they can log vibration, electrical and/or temperature data from anywhere in a facility. These measurements can be monitored via real-time alarms sent to your phone or mobile device.
Here are three diagnostic challenges associated with unmonitored equipment that a condition monitoring system can help resolve:
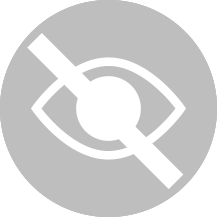
Unnoticed problems until failures occur
Equipment that isn’t monitored often stays that way — under the radar. Condition monitoring is an industrial system of wireless sensors and a gateway that your team can easily move around the plant. Its versatility provides a monitoring solution for when a second opinion is needed or when you need to identify an intermittent fault or check a fixed sensor. You can log measurements 24/7 and set up alarms so that you can leave the plant with the peace of mind that your equipment is being watched.
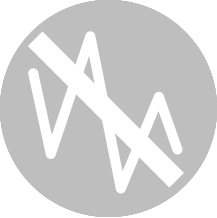
Limited trending and analysis capabilities
The inability to track vital equipment over time results in fragmented information and data that is siloed, inconsistent or impossible to analyze. Machines that aren’t monitored can become the weakest link in your production chain, thereby increasing the risk of failure or downtime. Condition monitoring allows you to capture baseline data and trend¬ing on equipment so you can identify problems quickly. By correlating historical trends and tracking current conditions, you can detect faults and increase equipment uptime.
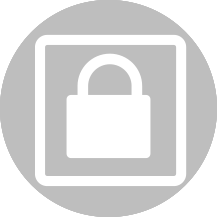
Some sensors miss the root cause of downtime
Some fixed sensors require a sizable investment in design, engineering and IT, and retrofitting can be cost prohibitive for less-critical equipment. In addition, by definition fixed sensors are limited by their location. A condition monitoring system equipped with connected tools and software provides a flexible, cost-effective and easy-to-setup alternative. Whether taking simple electrical and temperature measurements or power monitoring, modern condition monitoring systems are designed to deliver the equipment insight you need when you need it. This puts you in front of a potential issue so you can avoid costly downtime or failure and track the root cause more easily.
To learn more about Fluke Condition Monitoring and how a condition monitoring system will improve your predictive maintenance program, please call our sales team or visit our condition monitoring page.