In a short time, hand-held infrared (IR) thermometers have gone from exotic to commonplace. Portable and convenient, they are useful for troubleshooting and checking both product quality and process quality. Fluke's family of IR thermometers offers users speed and convenience.
In addition, Fluke's newest IR thermometer adds improved targeting for increased accuracy. The Fluke 62 MAX+ provides two targeting lasers to help users better see "the spot." The most common IR thermometers use a single laser in the in the center of the spot. But the Fluke 62 MAX+ uses dual, rotating lasers to show the outside of the circle that defines the measurement spot.
Temperature measurement strategies
In general, there are three ways to use any kind of infrared, non-contact thermometer:
- Measuring the temperature at a spot
This type of measurement is used to measure and track temperature at a single spot. It is useful for trending the temperature of an object or comparing a measurement to a speci?cation. A thermometer with high repeatability helps ensure consistency for this kind of measurement. - Comparing the temperature of two spots
This type of measurement might be used to check the functioning of a steam trap by measuring the temperature of the inlet and outlet. No change indicates the trap has failed open. A very large change indicates the trap has failed closed. - Scanning an object and detecting changes within a continuous area on it
This capability allows the user to ?nd hot or cold spots on housings, panels, and structures. For example, one can check the heat sink of air-cooled transformers for cool tubes that indicate a restricted ?ow or a lack of ?ow.
Applications for infrared thermometers
Infrared thermometry can be used for process monitoring, plant predictive and preventive maintenance, electrical applications, quality assurance, and other applications.
Infrared (IR) non-contact thermometers are ideal for moving targets and machinery, hazardous and inaccessible or distant targets, electrical components, "big picture" evaluations of machinery or surfaces, trending records, and even protection against litigation and insurance claims. In fact, insurance companies are encouraging their customers to implement preventive infrared scanning.
IR thermometers and imagers can save time and money for contractor and customer alike, as well as perform diagnostics that were previously impossible without shutting down systems.
Here are some suggestions for applications in which IR non-contact thermometers have proven useful.
Electrical maintenance
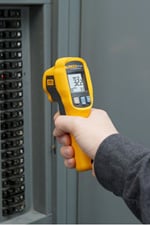
Check for heat buildup created by loose connectors. Troubleshoot problems in battery banks and power panel terminations, ballasts, switchgear and fuse connections. Identify hot spots in the output ?lters on dc battery connections.
Use an IR thermometer to inspect supply power connections and circuit breakers (or fuses) for equal temperatures. An IR thermometer is effective in determining the source of the problem when a thermal overload protection device does not work and the motor shuts down.
Because electrical currents generate heat, temperature monitoring is an efficient way to predict potential equipment failure.
Equipment maintenance
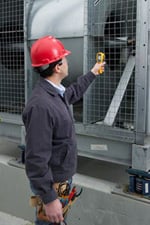
Check moving parts and housings in motors and gear boxes for hot spots. Temperature change can indicate developing problems in many types of equipment, from ovens and boilers to freezers. Routine temperature audits of generators and their bearings can prevent expensive repairs. Scanning bearing temperatures with an infrared thermometer allows the maintenance engineer to detect hot spots and schedule repairs or replacements before the problem leads to an equipment failure.
Building controls
Monitor HVAC/R components for quick energy audits and room balancing in a short time. An IR thermometer with a 60:1 distance-to-spot ratio makes elevated vents and returns more accessible.
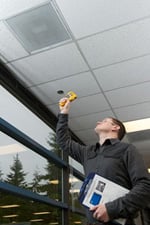
For example, if a thermometer has a 10:1 distance to spot ratio, one can stand 10 inches away from the target and measure the temperature of a one-inch circle. At 10 feet away from the target, the measurement spot will be a one-foot circle.
An IR thermometer can quickly survey compressor head temperatures, compressor oil sump temperatures, evaporator coil and suction line temperatures, discharge line temperatures, condenser coil and liquid line temperatures, and fan motor temperatures.
Insulation on all surfaces can be scanned for leakage and losses. Higher temperatures are indicated by a shift toward white. Lower temperatures are indicated by a shift toward black.
Process/product
Monitor process lines. Check the temperature of different products on production lines. These can vary from rubber tires to plastic, from concrete to chocolate bars.
Other useful features
A lighted display makes it easier to view results in poorly lit areas.
High temperature alarm warnings call attention to temperatures that exceed a specified threshold. Alarms that are both audible and visible are more effective even in loud environments.